Researchers at Rice University and Lockheed Martin may have developed a low-cost method of creating longer-lasting, high-capacity lithium-ion batteries. Currently graphite is used as the anode in commercial li-ion products, despite the fact that a silicon anode could potentially store ten times more lithium ions. The team says it has solved one of the problems associated with silicon, which nearly triples the energy density of current li-ion designs.
Engineer Sibani Lisa Biswal and research scientist Madhuri Thakur had been working on a porous silicon film with sponge-like properties, but wanted to create something more applicable to the current battery manufacturing process.
They discovered that by crushing the film, the resulting powder had a surface area 50 times that of regular crushed silicon. The result is an anode material that can hold a charge of 1,000 milliamp hours per gram compared to graphite anodes, which store 350 mAh/g – and that's only a third of its theoretical capacity.
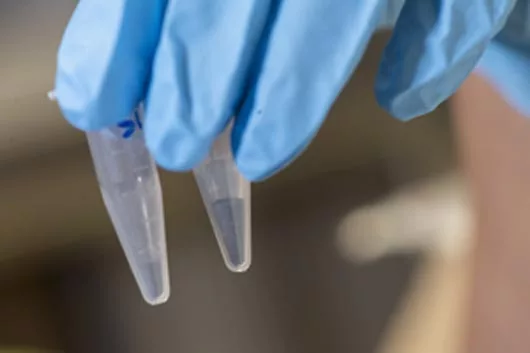
“We’re truly excited about this breakthrough and are looking forward to transitioning this technology to the commercial marketplace,” said Lockheed Martin researcher Mark Isaacson, despite questions of cost and scale that need to be addressed.
The team is working on a completed battery that will test their design, and part of that will be finding the best silicon-friendly cathode material. That said, if all goes well this could be the long overdue breakthrough in battery technology that electric vehicles and mobile electronic device manufacturers have been waiting for.
Source: Rice University