Transitioning to 100% renewable energy globally would be cheaper and simpler using firebricks, a form of thermal energy storage with roots in the Bronze Age, to produce most of the heat needed for industrial processes, according to a new Stanford study.
Today’s industries require high temperatures for manufacturing, which are achieved largely by continuously burning coal, oil, fossil gas, or biomass. With much of the world focused on reducing emissions by transitioning away from fossil fuels to renewable sources like wind, solar, and hydro, the question is how to provide industries with on-demand continuous heat in a 100% renewable world.
In a recently published study, researchers from the Department of Civil and Environmental Engineering at Stanford University proposed that an ancient solution, firebricks, could be the answer.
“By storing energy in the form closest to its end use, you reduce inefficiencies in energy conversion,” said Daniel Sambor, a postdoctoral scholar in civil and environmental engineering and a study co-author. “It’s often said in our field that ‘if you want hot showers, store hot water, and if you want cold drink, store ice’; so, this study can be summarized as ‘if you need heat for industry, store it in firebricks.'”
As energy from wind and solar fluctuates, it’s important that sources replacing combustion fuels are capable of electricity or heat storage. Refractory bricks, which can withstand high temperatures without damage, have been used for thousands of years – likely since the early Bronze Age – to line furnaces, kilns, fireplaces, and ovens.
Similar to refractory bricks, firebricks can store heat or insulate, depending on what they’re made from. Firebricks used for heat storage should have a high specific heat – the amount of heat 1 g of a substance must absorb or lose to change its temperature by 1 °C (1.8 °F) – and a high melting point. Ideal low-cost firebrick materials with these properties include alumina and magnesia or low-grade graphite. Insulating firebricks must withstand high temperatures but have low thermal conductivity to resist heat flow and obtain heat slowly from their surroundings. Silica has a low thermal conductivity, so is regularly used in these types of firebricks.
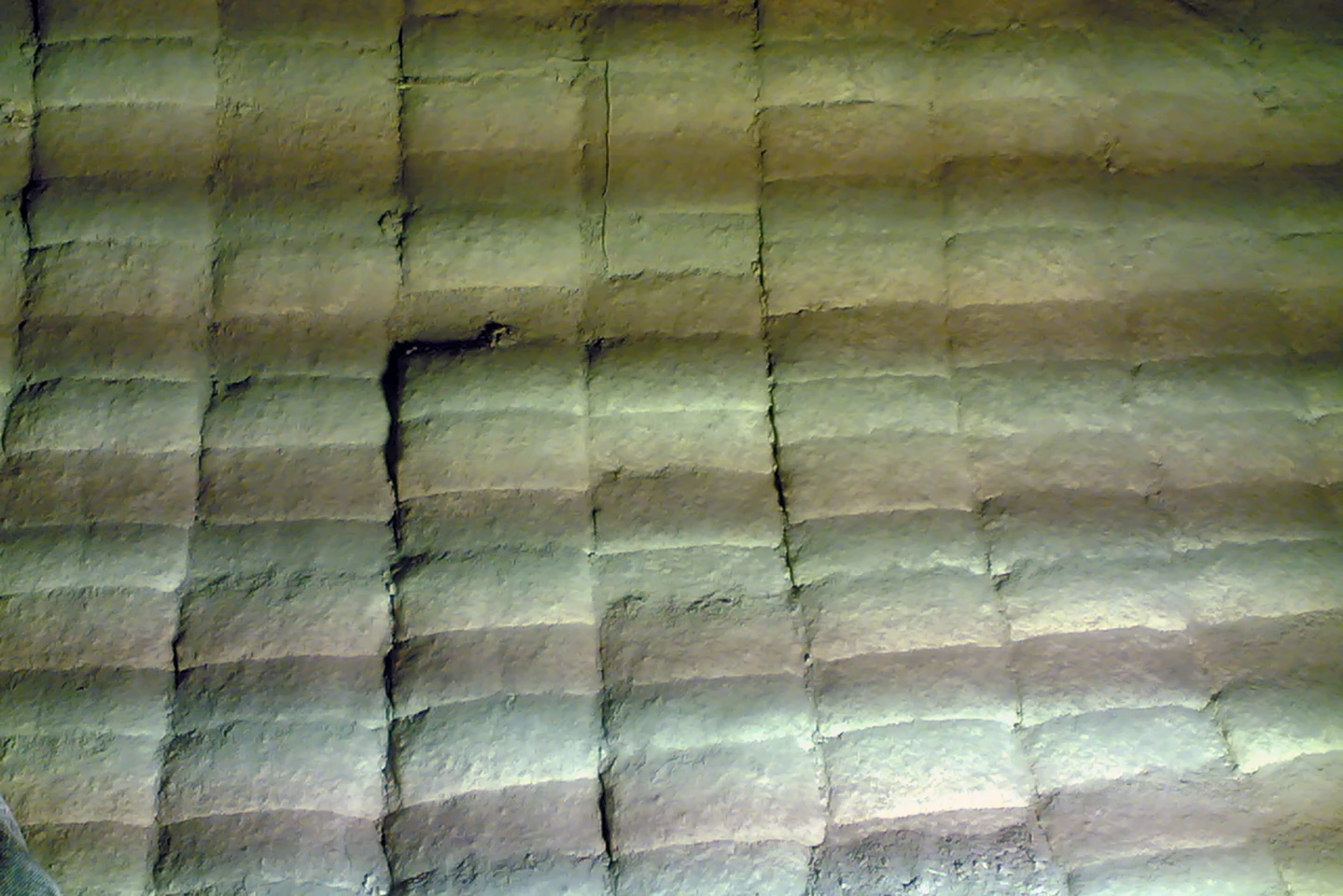
Heat-storing firebricks are surrounded by another type of firebrick that’s more insulating and then by steel, such as a thick steel container, to further reduce heat loss. Process heat can be drawn from the firebricks on demand by passing ambient or recycled air through channels in the bricks to produce low-to-high temperature air or obtained from the emission of infrared radiation directly from the red-hot bricks. Using firebricks avoids the need for battery storage or green hydrogen storage of renewable electricity as electricity storage is replaced by firebrick storage.
The purpose of the present study was to examine the impact of using firebricks to store most industrial process heat in 149 countries that had, in a hypothetical future in the year 2050, transitioned to 100% clean and renewable energy. The 149 countries chosen are responsible for producing 99.75% of fossil fuel carbon dioxide (CO2) emissions globally. The researchers used computer models to compare costs, land needs, health impacts, and emissions for two scenarios: one where firebricks provided 90% of industrial process heat and one in which no firebricks were used.
“Ours is the first study to examine a large-scale transition of renewable energy with firebricks as part of the solution,” said Mark Jacobson, professor of civil and environmental engineering at Stanford’s Doerr School of Sustainability and the study’s lead and corresponding author. “We found that firebricks enable a faster and lower-cost transition to renewables, and that helps everyone in terms of health, climate, jobs, and energy security.”
Across the 149 countries, compared to the scenario where firebricks weren’t used, using firebricks was found to cut capital costs in 2050 by a substantial US$1.27 trillion. Firebricks also reduced the need for energy storage capacity from batteries by around 14.5%, annual hydrogen production for grid electricity by around 27.3%, land needs by about 0.4%, and overall annual energy costs by about 1.8%. For the ‘no firebricks’ scenario, it was assumed that countries would obtain the heat for industrial processes from electric furnaces, heaters, boilers, and heat pumps, with batteries used to store electricity for those technologies.
“The difference between firebrick storage and battery storage is that the firebricks store heat rather than electricity and are one-tenth the cost of batteries,” Jacobson said. “The materials are much simpler, too. They are basically just the components of dirt.”
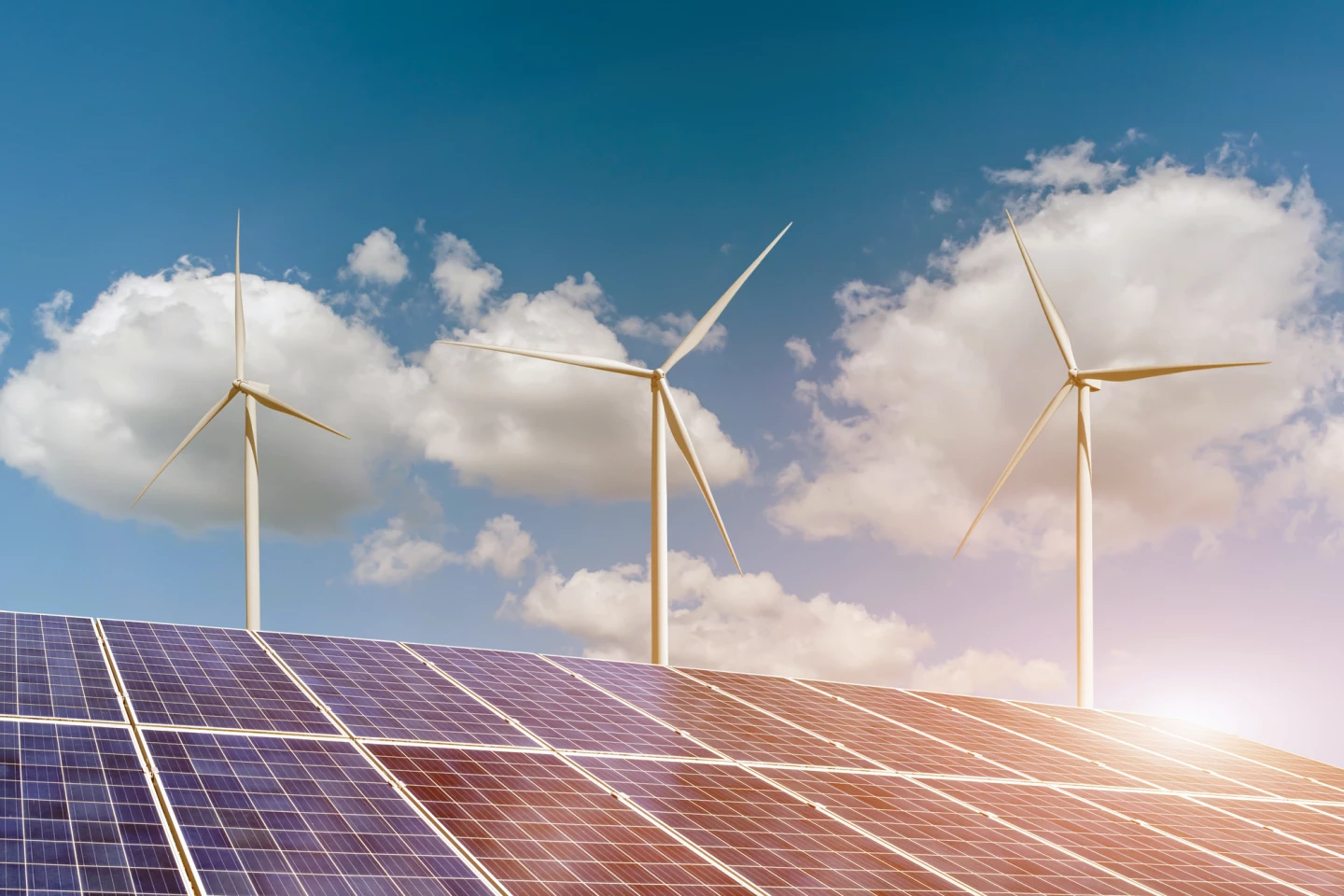
An important question arises out of the study: what about the gases and particles from industrial combustion and CO2 emissions from industrial process chemical reactions – primarily from steel and cement manufacturing – that firebricks don’t address? The researchers propose that electric arc furnaces, resistance furnaces and boilers, induction furnaces, electron beam heaters, and dielectric heaters could cover industrial combustion not covered by firebricks. The CO2 emissions from steel manufacturing could be addressed by using green hydrogen instead of coke or coal to reduce iron ore to pure iron. And, the CO2 from cement production, they propose, could be eliminated by using basalt (calcium silicate rock with no carbon) instead of limestone during ordinary Portland cement (OPC) production and using geopolymer cement instead of OPC. Combining these techniques with firebricks, the researchers say it’s possible to “eliminate most if not all air pollution and CO2 from industrial manufacturing without the need for carbon capture.”
High-temperature heat-storing firebricks are widely commercially available. The researchers say that using them to aid in the transition to renewables would make the process inexpensive and simple, two things that they hope will attract people to support their novel solution.
“Imagine if we propose an expensive and difficult method of transitioning to renewable electricity – we’d have very few takers,” said Jacobson. “But, if this will save money compared with a previous method, it will be implemented more rapidly. What excites me is that the impact is very large, whereas a lot of technologies that I’ve looked at, they have marginal impacts. Here, I can see a substantial benefit at a low cost from multiple angles, from helping to reduce air pollution mortality to making it easier to transition the world to clean renewables.”
The study was published in the journal PNAS Nexus.
Source: Stanford