Even when it’s ground into microparticles, 97% of an algae-based plastic biodegrades in compost and water in under seven months, a new study has reported. The researchers hope their plastic will eventually replace existing petroleum-based ones, which have caused concern due to their effects on health and the environment.
In recent years, there has been a great deal of chatter about – and research into – microplastics, the tiny, almost indestructible fragments shed from everyday plastic products. Much of that research has focused on devising ways of collecting and removing microplastics from the environment to prevent the health problems they can cause.
In a new study, researchers from the University of California, San Diego (UC San Diego) and materials-science company Algenesis have attacked the problem from another angle, developing a plant-based polymer that biodegrades, even when it’s ground into a microplastic, in under seven months.
“We’re just starting to understand the implications of microplastics,” said Michael Burkart, professor of chemistry and biochemistry at UC San Diego, Algenesis co-founder and one of the study’s authors. “We’re trying to find replacements for materials that already exist, and make sure these replacements will biodegrade at the end of their useful life instead of collecting in the environment. That’s not easy.”
Biodegradation is the process by which microbes break down polymers into simpler molecules. It requires that the polymer contains chemical bonds that are physically accessible to the plastic-degrading enzymes the microbes produce and that those microbes can consume the molecules released by the polymer’s breakdown. Note: all plastics are polymers, but not all polymers are plastics.
“When we first created these algae-based polymers about six years ago, our intention was always that it be completely biodegradable,” said Robert Pomeroy, also a professor of chemistry and biochemistry, Algenesis co-founder, and study author. “We had plenty of data to suggest that our material was disappearing in the compost, but this is the first time we’ve measured it at the microparticle level.”
Years ago, a project by Pomeroy, Burkart and molecular biology professor Stephen Mayfield to turn algae into fuel morphed into a quest to develop high-performance biodegradable polyurethane. Given that plastics come from petroleum, and petroleum comes from algae – it’s just fossil algae oil, after all – the researchers set about making plastics directly from algae oil? The resulting algae-based polymer, called TPU-FC1, was used to create the world’s first biodegradable shoes. Pomeroy even wrote a book about his algae-based material.
For the current study, the researchers used a belt sander fitted with 80-grit sandpaper to generate microplastics of various materials, including TPU-FC1. Different belt sanders were used on each material to prevent cross-contamination. They used different measures to test whether microbes were digesting the microplastics.
First, the microplastics were placed in compost, which naturally contains microbes, under the same conditions as would exist in a home compost. After 90 days, examination of compost samples showed a 68% decrease in TPU-FC1 microparticles, whereas the amount of EVA microparticles was virtually unchanged. After 200 days, the particle counts of microplastics in the TPU-FC1 sample showed a 97% overall reduction from the starting count (the EVA count didn’t change).
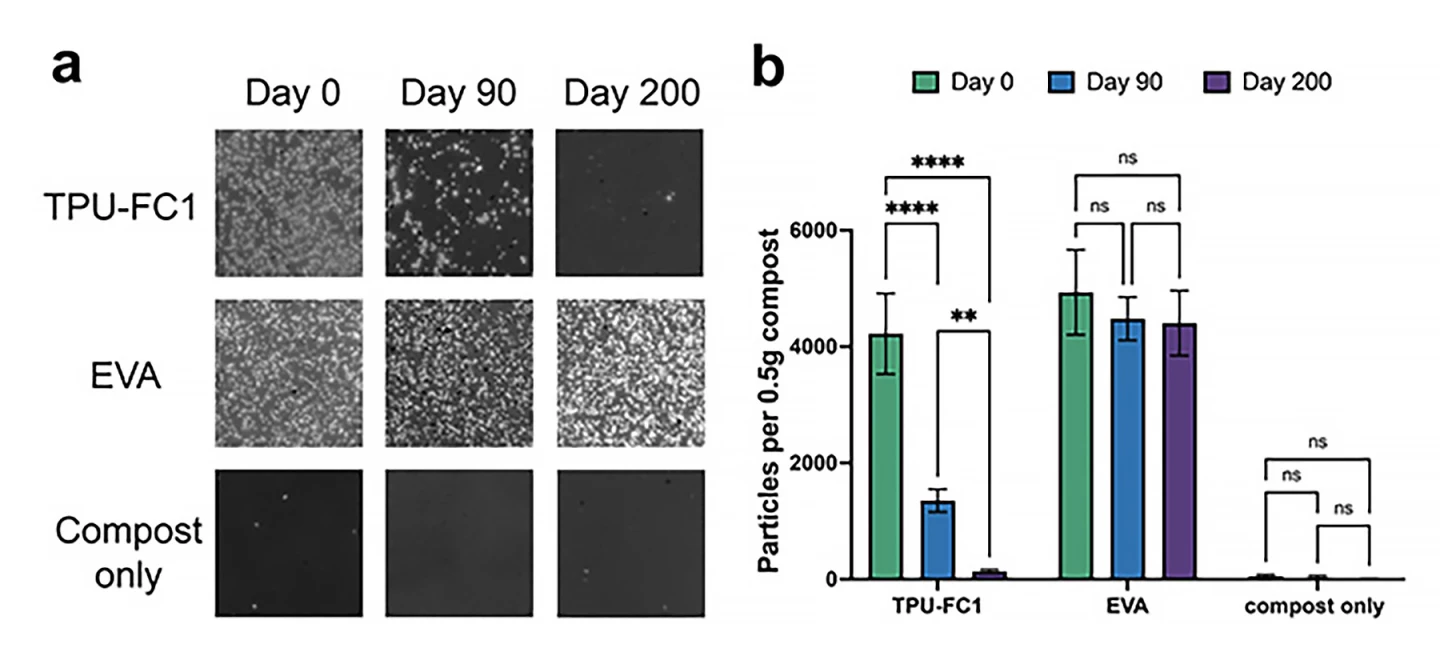
A parallel set of samples with identical microplastics and compost was used to track carbon dioxide (CO2) levels, measured using a respirometer. When microbes break down compost, they release the gas. Cellulose-only samples served as an internal control to monitor background ‘CO2 evolution’, a measurement of the microbial activity in a compost. The cellulose reached 75% CO2 evolution within 45 days, indicating that the compost was sufficiently active. As expected for a non-biodegradable material, EVA microparticles showed no CO2 evolution over the 200-day experiment. TPU-FC1 microplastics displayed significant biodegradation, reaching 76% CO2 evolution at the 200-day time point. Thus, respirometry confirmed the biodegradability of TPU-FC1 and demonstrated that one outcome of that biodegradation was the conversion of the carbon from the microplastics into CO2.
Since plastics aren’t water soluble and float, they can easily be scooped off the surface of water, so the team next tested the microplastics by adding them to water. At intervals of 90 and 200 days, almost 100% of the EVA microplastics were recovered, meaning none had biodegraded. In contrast, after 90 days, only 32% of TPU-FC1 microparticles were recovered, and after 200 days, only 3% were recovered, indicating that 97% had biodegraded.
Chemical analysis of the algae-based plastic detected the presence of the monomers used to make the plastic, indicating that the polymer had been broken down to its starting plant materials. Further analysis identified bacteria capable of using TPU-FC1 as a carbon source and confirmed that they were able to break it down.
“This material is the first plastic demonstrated to not create microplastics as we use it,” said Stephen Mayfield, another of the study’s authors. “This is more than just a sustainable solution for the end-of-product life cycle and our crowded landfills. This is actually plastic that is not going to make us sick.”
Creating the biodegradable plastic using conventional manufacturing equipment has been challenging, but Algenesis is making progress. The company has partnered with Trelleborg to produce coated fabrics and RhinoShield to produce cell phone cases.
“When we started this work, we were told it was impossible,” said Burkart. “Now we see a different reality. There’s a lot of work to be done, but we want to give people hope. It is possible.”
The study was published in the journal Scientific Reports.
Source: UC San Diego