Researchers have developed a way of recycling one of the most popular but environmentally problematic of fabrics: polyester. Their new method is simple, non-toxic for humans and the environment and, what’s more, it preserves the integrity of the cotton removed from the fabric so that it’s ready for reuse.
Polyester got a bad rap in the ’70s, mainly because it was used to make some horrendous ‘fashion.’ Nowadays, while fashions have arguably improved, we’re more aware of the environmental impact of polyester, the second most used textile in the world.
The fabric has its pros: it’s long-lasting, lightweight, moisture resistant, quick drying and easy to clean. However, on the downside, making the polyethylene terephthalate (PET) and cotton blend relies on fossil fuels and produces a lot of carbon dioxide. And once you’re done wearing it, rather than being recycled, the bulk of polyester ends up in a landfill where it doesn’t degrade (at least, not for a very long time).
Now, researchers from the University of Copenhagen may have developed a solution to the polyester problem, developing a simple, green way of recycling the product.
“The textile industry urgently requires a better solution to handle blended fabrics like polyester/cotton,” said Yang Yang, lead author of the study. “Currently, there are very few practical methods capable of recycling both cotton and plastic – it’s typically an either-or scenario. However, with our newly discovered technique, we can depolymerize polyester into its monomers while simultaneously recovering cotton on a scale of hundreds of grams, using an incredibly straightforward and environmentally friendly approach.”
The game-changing method requires only three things: heat, a non-toxic solvent and hartshorn salt, otherwise known as ammonium carbonate, a product used in baked goods.
“For example, we can take a polyester dress, cut it up into small pieces and place it in a container,” said Shriaya Sharma, a study co-author. “Then, add a bit of mild solvent, and thereafter hartshorn salt, which many people know as a leavening agent in baked goods. We then heat it all up to 160° C [320 °F] and leave it for 24 hours. The result is a liquid in which the plastic and cotton fibers settle into distinct layers. It’s a simple and cost-effective process.”
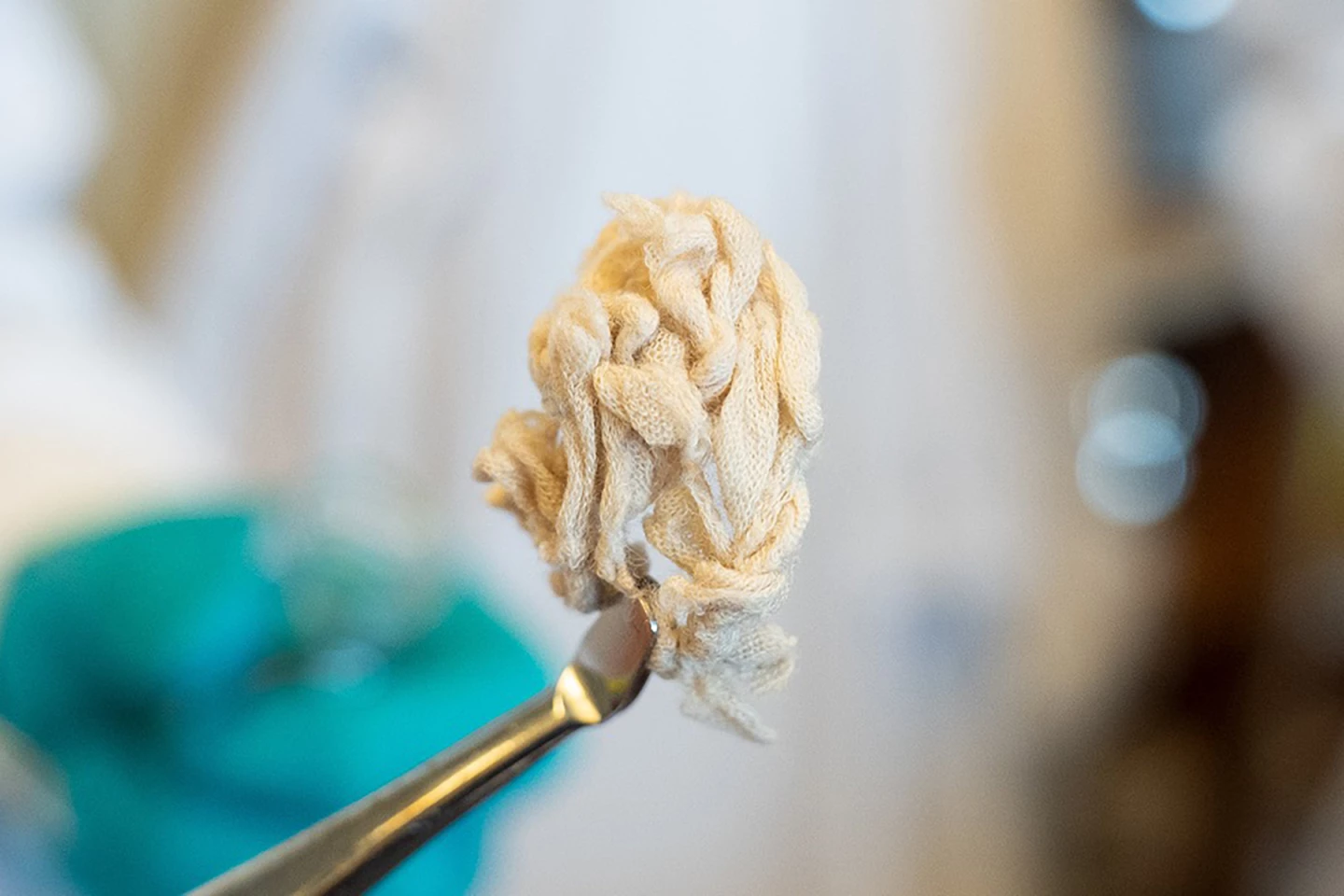
When heated, ammonium bicarbonate breaks down into ammonia, carbon dioxide and water. When ammonia and carbon dioxide combine they act as a catalyst, setting off a selective depolymerization reaction that breaks down the plastic but preserves the cotton. While ammonia is toxic on its own, when paired with carbon dioxide it’s safe for humans and the environment.
After discovering that carbon dioxide could be used as a catalyst to break down nylon, the researchers explored the addition of hartshorn salt and were pleasantly surprised by the results.
“At first, we were excited to see it work so well on the PET bottle alone,” said study co-author Carlo Di Bernado. “Then, when we discovered that it worked on polyester fabric as well, we were just ecstatic. It was indescribable. That it was so simple to perform was nearly too good to be true.”
At this stage, the researchers have only tested their method in the lab but are shopping around for companies to adopt it, touting its scalability as a selling point.
“We’re hoping to commercialize this technology that harbors such great potential,” Yang said. “Keeping this knowledge behind the walls of the university would be a huge waste.”
The study was published in the journal ACS Sustainable Chemistry & Engineering.
Source: University of Copenhagen