British engineer Ian Foley has had considerable input into Formula One racing, designing active suspension systems for Lotus and a KERS system for the Williams team. But in recent years he's turned his hand to electric drivetrain technology, and he's taken his company Equipmake in a new direction as he looks to build something a little more relevant to the average Joe.
It comes in the form of an electric motor that has its magnets arranged like spokes around the central hub, and Foley claims it offers superior torque, power density and cooling capabilities in a package that's smaller and cheaper to manufacture than a standard motor. With electric drivetrains set to own the coming decades in both consumer and public transport, that kind of claim is a big deal.
"Most of the radial flux permanent magnet motors that are out there in automotive have the magnets arranged in a very shallow V-shape in laminations around the hub," Foley tells us over the phone from his office in Norfolk, UK. "This was a design that Toyota ran with 20 years ago with the Prius. Effectively, everybody's gone with similar versions of that design."
The problem is cooling. With the magnets in this standard arrangement, it's hard to get coolant close enough to them to keep them in their operating zone under constant high-power operation.
Hence, electric motors have two power figures: how much they can put out flat out (peak power) and how much they can sustain without eventually overheating and needing to shut down (continuous power). I've experienced this kind of shutdown on the road with certain electric motorcycles; when you ride them hard for an extended period, the engine management system quietly kicks in and limits your power output. It's more than a little annoying, particularly on a performance vehicle.
You can offset this kind of thermal cut-off by using more expensive magnet materials – neodymium itself demagnetizes quickly as the temperature rises, but you can specify your magnets to include additives that bump the thermal shutdown temperature higher, as long as you don't mind the additional cost of these fancy high-temp magnets.
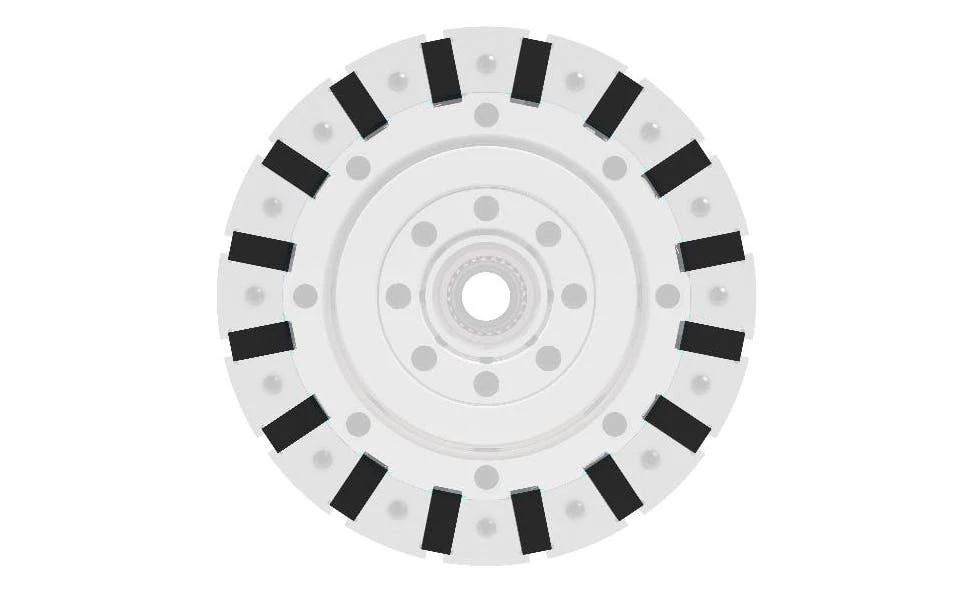
"The spoke motor has magnets arranged at 90 degrees to the hub, like the spokes of a wheel," says Foley. "And there's laminations in between each of those spokes. This arrangement gets better use of the magnetic material; it means that for a certain torque we can use 25 percent less magnet material, or use the same amount and get 25 percent more torque.
"It also means, because the magnet sits right on top of the hub, we can get water inside the hub and cool the magnet directly. So the spoke architecture gives us more torque to start with, but more importantly it lets us get water right underneath the magnet and get it much better cooled.
"We don't need expensive high-temp magnets. We can use the cheapest, cooking-grade neodymium magnet because we can keep it cool enough and still maintain the performance."
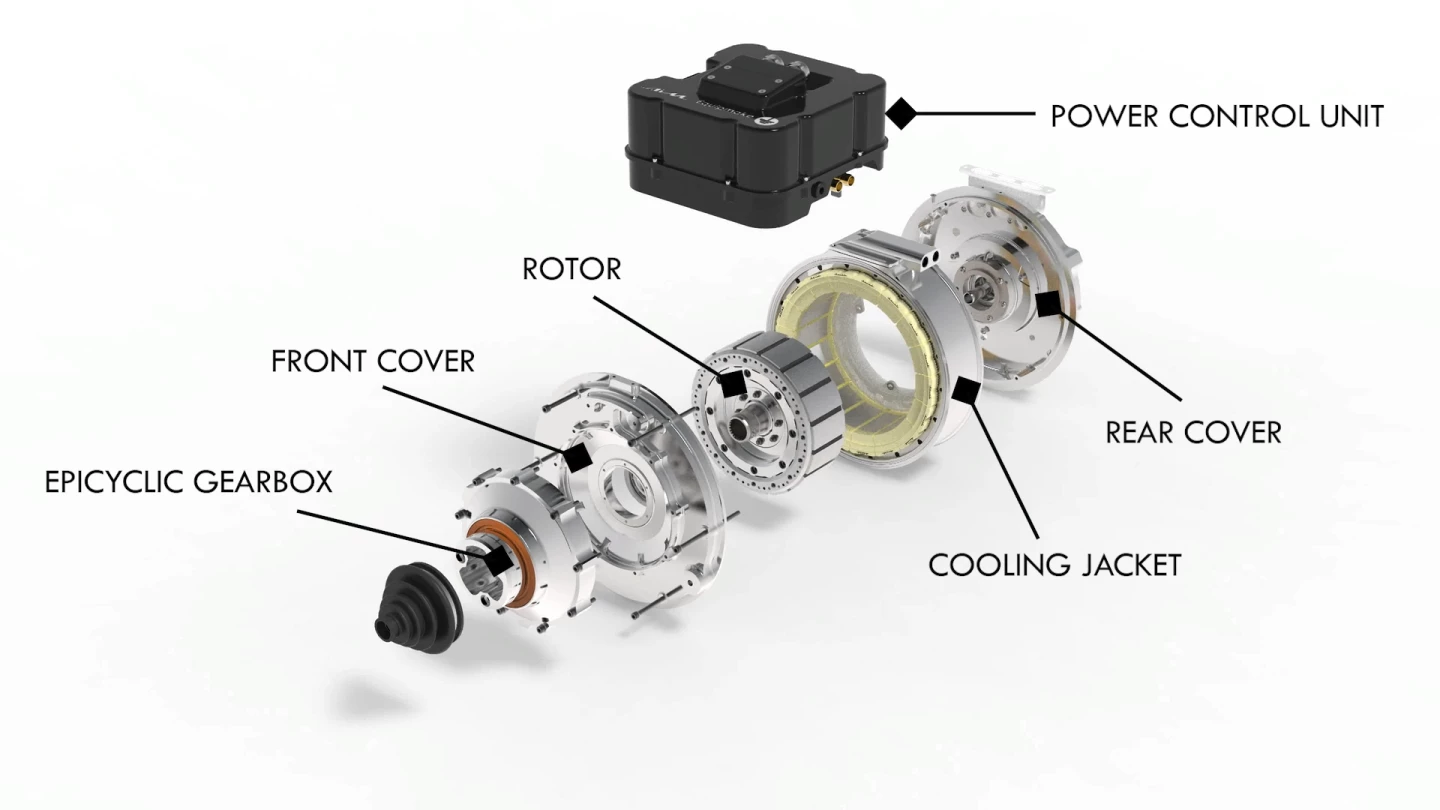
For comparison's sake, let's take a look at the record-breaking Siemens electric aviation motor we covered back in 2015. These things were astoundingly light and powerful for the day, pumping out a massive 5 kilowatts per kilogram of weight. Equipmake claims its spoke motors can make as much as 9 kW/kg, in a package that's cheap and easy to manufacture.
Spoke motors aren't new – there have been many designs over the years. It's just that nobody's figured out how to build one cost-effectively, says Foley: "Fundamentally the spoke motor architecture is very well known. A number of large companies like GE have written papers on the benefits of the spoke motor. The reason the standard motor is widely adopted is because there's a well known route to low cost manufacture.
"There are some design challenges to implementing the spoke cost effectively. The existing designs worked, but they really weren't suitable for mass production, they were very expensive. We use a cheap aluminium hub, which is forged, so a very low cost method of manufacture. And the way we interlock the laminations, they hold the magnets in, and that's a whole design including the cooling system which we've patented.
"All of the processes and materials we use are standard processes. So the fact that it's smaller and lighter means that it'll be cheaper. There's nothing in the design or manufacture that involves an expensive process that isn't being used for motor manufacture at the moment.
"And we know from other work that we've done on other motors that a conventional motor of very similar performance in terms of peak and continuous power, we're about 50 percent of the volume and 80 percent of the mass. So, the fact that it's smaller and lighter means it'll be cheaper. I can't put a figure on how much cheaper it'll be in mass manufacture, but there's no expensive processes, and it's got less materially, so it's going to be cheaper."
Equipmake's initial focus will be on the automotive sector because all those years Foley spent working with F1 teams have built him a significant network among people who build fast cars.
Understandably then, two of the company's current projects are electric supercars. One's still under wraps, but the other is currently known as the Ariel Hipercar: an ultra-lightweight, 1,180-horsepower (880-kW) monster that's set to go into production in 2020. The Hipercar will use one of Equipmake's APM200 motors for each of its four wheels. It'll have a fairly small, high-density battery, sustained by a 120,000-rpm gas-driven turbine range extender for longer trips.
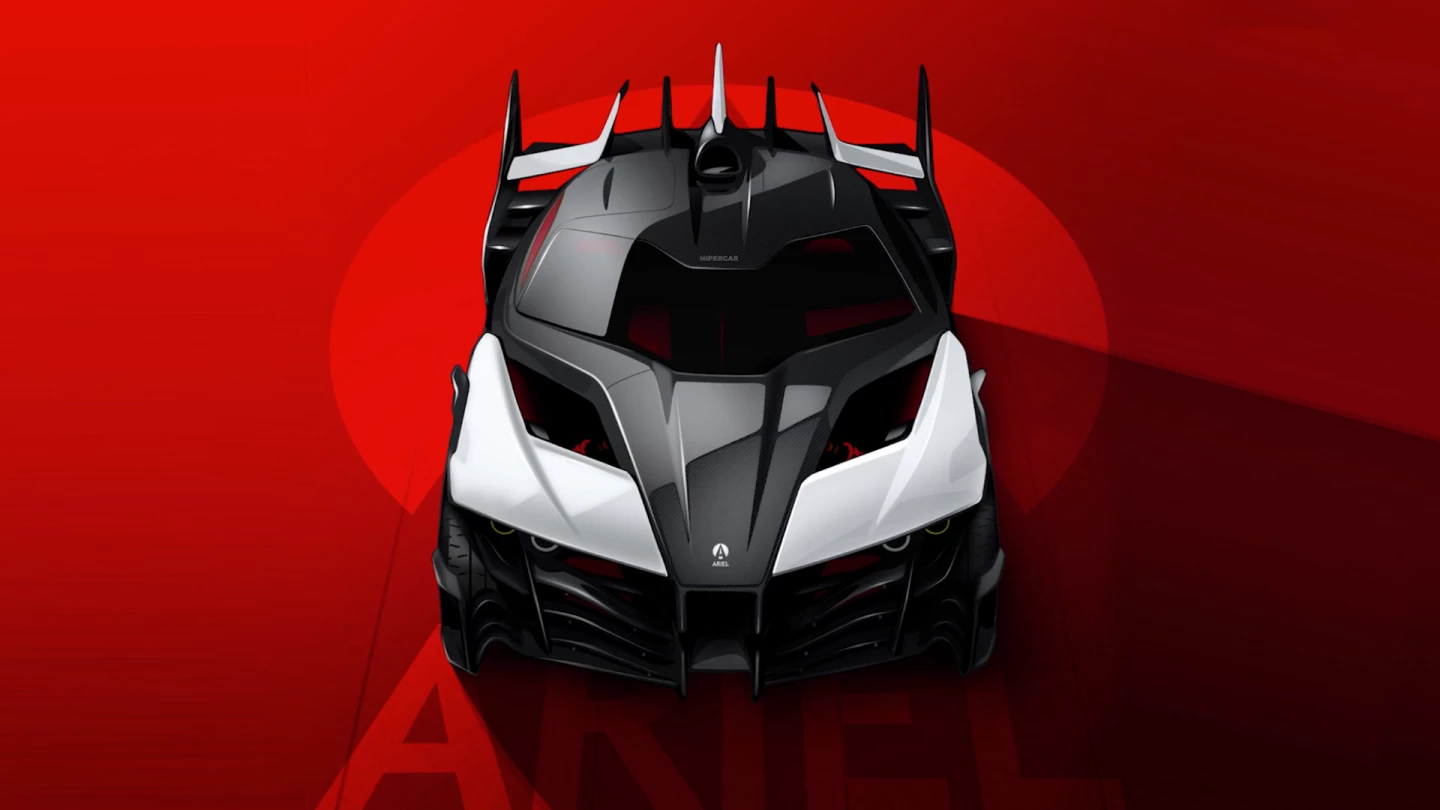
Another project plans to use Equipmake's lightweight, affordable electric powertrains to build a cost-effective electric bus platform. Foley estimates these buses will be cheaper than diesel vehicles over a five to 10-year period, depending on the market. Working prototypes are expected within months, with testing and development time scheduled for a 2020 production run.
At the same time, Equipmake is responding to a number of enquiries from the aviation and marine industries, where arguably even more can be made of the spoke motor's sustained power capabilities.
Check out a video explanation below.
Source: Equipmake