Desktop 3D printers have hit price-points that make them as affordable as color laser printers. But they also share the same problem – replacing the printing medium costs an arm and a leg. A kilogram of plastic filament costs about US$50, meaning the cost of turning your ideas into reality can quickly add up. But now the Filabot, a miniature plastic recycling plant, will provide a wide variety of plastic filaments from scrap.
Invented by American college student Tyler McNaney, the Filabot can make new 3D printing filament in 3.0 or 1.75 mm (1/8 or 1/15 in) diameters using nearly any household plastic, from PET and polypropylene to Nylon-101. A two-liter soda bottle (PET) weighs about 50 grams, which will be converted into about $2.50 of 3D printing filament. The Filabot can also recycle failed, broken, or obsolete 3D printed parts, making prototype development far less costly. McNaney has even developed an extrudable conducting plastic from scrap.
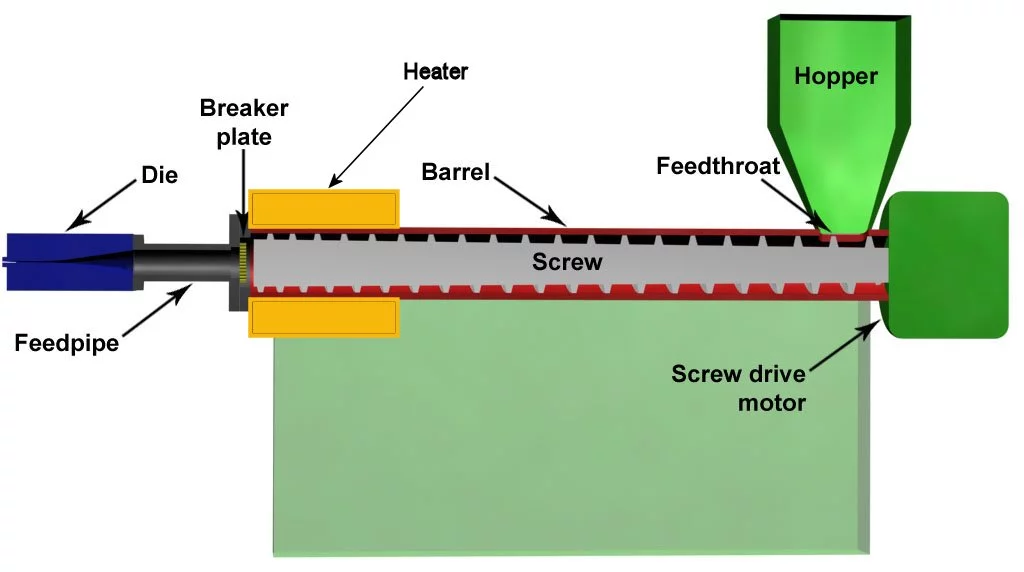
The Filabot comes with a plastic grinder that converts scrap plastics into tiny pieces suitable as feedstock for the filament extruder. The plastic feedstock is gravity-fed onto a feed screw, which moves the plastic toward the extrusion die. On the way, the plastic is heated – not to melt it, but to allow extrusion at a reasonable pressure for a tabletop unit. On being formed, the new filament is air-cooled slightly, then wound onto an empty spool ready for reuse. No additional treatment or finishing is needed.
Following a successful Kickstarter campaign (the project raised US$32,330, well over the target of US$10,000), McNaney is nearly done producing the first 67 production units for his Kickstarter investors. Shortly thereafter he will begin general production of Filabot grinders and extruders. No pricing information is yet available, but the cheapest Kickstarter pledge to secure a ready-to-use Filabot was $490, so we wouldn’t expect it to sell for less than that.
An introductory Filabot video can be seen below.
Source: Filabot