It's one thing to 3D-print something as advanced as a jet engine, but it's another to fuel it up and push the start button. That's the step that GE Aviation took when it recently fired up a simple jet engine made entirely of 3D-printed parts in a test stand normally reserved for commercial jet power plants.
The 1-foot long by 8-inch tall (30 by 20 cm) engine was built at GE Aviation’s Additive Development Center outside Cincinnati as a side project. The result of several years' work, the purpose was to test the printing technology. It's not the first 3D-printed jet engine, but it has been fired and revved up to 33,000 RPM.
GE says that the simplified design was necessary because building anything like a conventional commercial engine is beyond the present technology’s state of the art. The team therefore chose a design created for remote control model planes, which was modified for Direct Laser Metal Melting (DLMM) printing
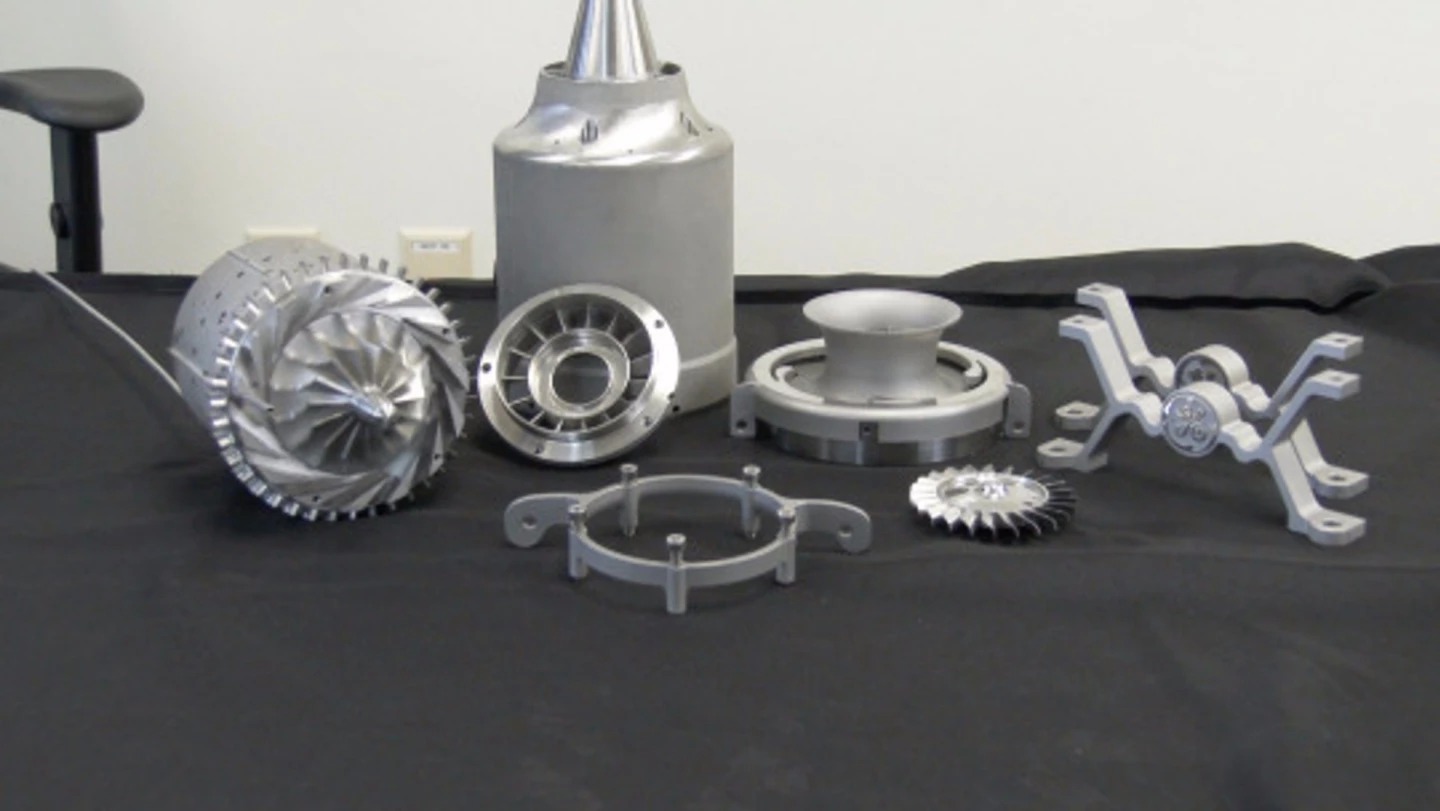
DLMM works by laying down a fine metallic powder in a flat layer, then a laser fuses a section of the CAD plan within it. Another layer of dust is laid down and the process is repeated. When the printing is completed, the excess powder is blown and brushed away, and the part is given a finish. The technique was used in fabricating GE’S first 3D-printed part to be certified by the American FAA for installation in the GE90 jet engine.
"There are really a lot of benefits to building things through additive," says Matt Benvie, spokesman for GE Aviation. "You get speed because there’s less need for tooling and you go right from a model or idea to making a part. You can also get geometries that just can’t be made any other way."
The model engine is on display at the Additive Development Center.
The video below discusses the 3D-printed model engine.
Source: GE Reports