Although glass is recyclable, the recycling process is generally limited to large pieces that can be easily sorted by color. Because it's not worth the effort to sort smaller fragments, they tend to simply be discarded. A new process, however, can convert them into a useful substance.
The proprietary technique was developed by PhD candidate Rhys Pirie and Prof. Damien Batstone, both of Australia's University of Queensland. It incorporates what is described as "a chemical that most people would know as drain cleaner," which is used to dissolve miscellaneous glass fragments into liquid silicate.
That liquid can subsequently be used in a wide variety of products, such as tires, detergents, toothpaste, concrete sealant and even crop fertilizer. It's also utilized to make silica gel, which is the desiccant contained in little packets with electronic devices. It cannot, however, be made into new glass on a commercial scale.
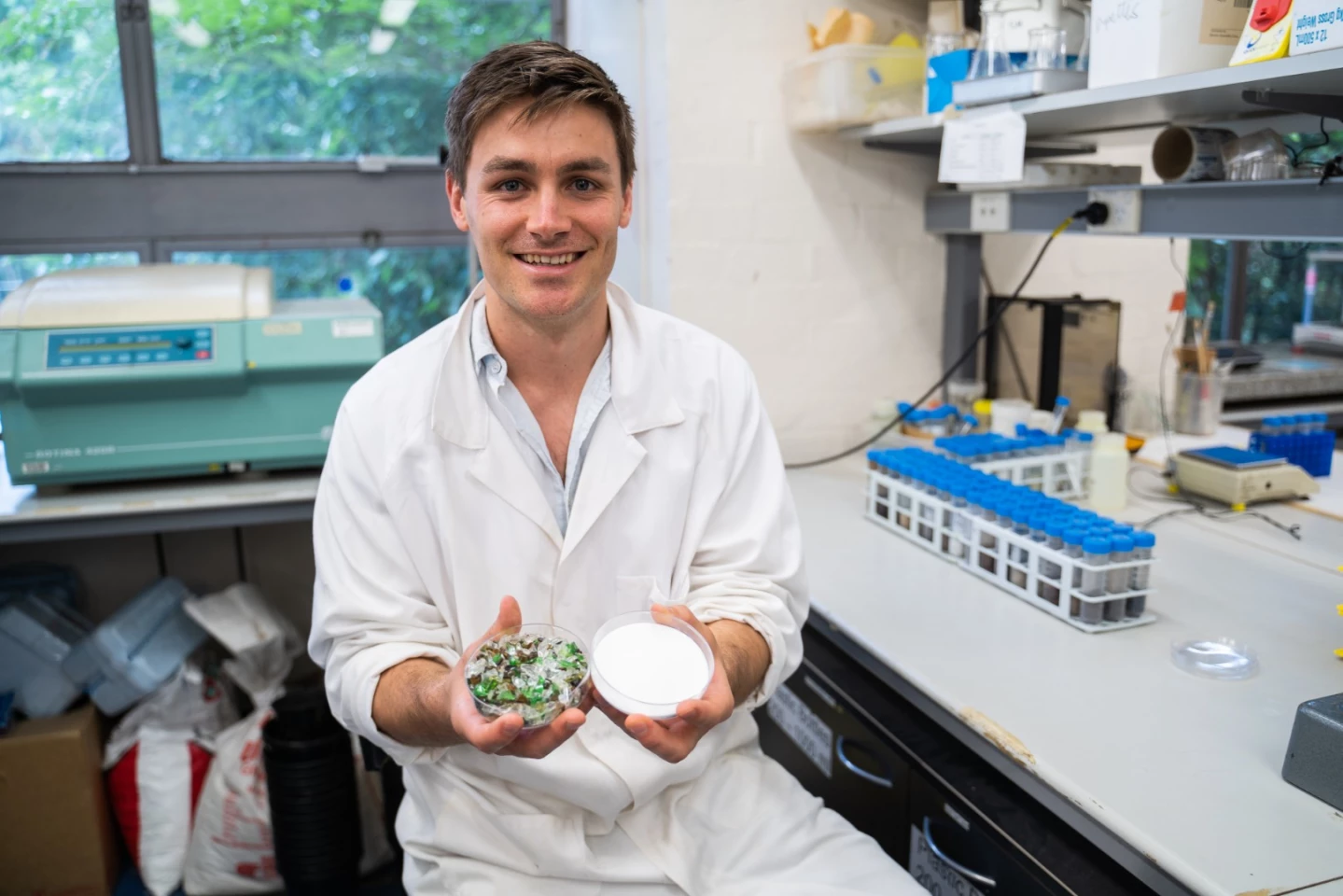
Because glass consists of around 70 to 75 percent silica – which is what gets converted to liquid silicate – the process results in little waste. According to Pirie (pictured above), approximately 1.3 kg (2.9 lb) of waste glass is required to make 1 kg of silica gel.
The technique also requires relatively little energy, unlike traditional methods of producing liquid silicate. Partially because of this, the researchers estimate that their process is over 50 percent cheaper than existing production systems.
"At the moment these kinds of silicates […] are generated through a glass production route where you make glass effectively and you then turn it into a silicate product that is a soluble gel-type product," says Batstone. "Instead of doing that, we're going to take glass that has already been made and is actually waste, and take it through a much simpler process to turn it into this commercial silicate product."
The university's commercialization company, UniQuest, is now seeking partner companies that are interested in taking the technology to market.
Source: University of Queensland