Daily finger-prick blood glucose tests are an unpleasant part of life for diabetics, which is why various groups have developed non-invasive glucose-monitoring sensors. Such devices may be becoming more effective and affordable, thanks to a project presently underway at Washington State University.
According to the university, currently-available continuous glucose monitoring systems aren't cost-efficient. They're typically manufactured via processes such as photolithography or screen printing – these have to take place in special "clean rooms," they require workers to take precautions against toxic chemicals which are used, and a lot of material ends up getting wasted.
Led by Asst. Prof. Arda Gozen and Prof. Yuehe Lin, a Washington State team set out to address those problems via 3D-printing technology.
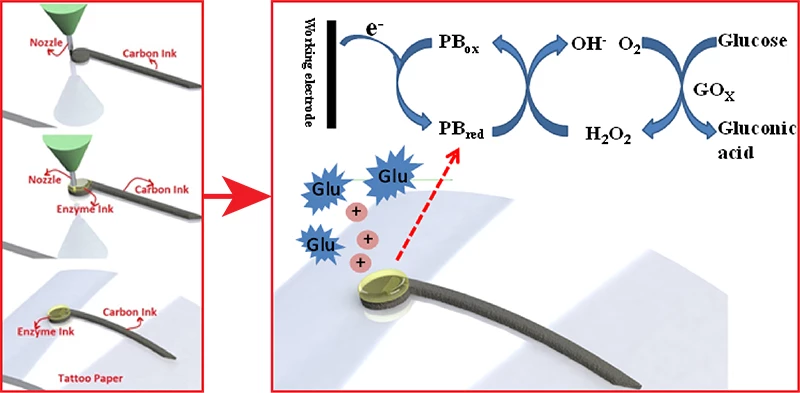
Utilizing a process known as direct-ink-writing, they created flexible glucose-sensing electrodes by finely depositing conductive carbon/enzyme-based polymer "ink" onto a tattoo paper substrate from a nozzle. Due to the fact that the material could be deposited so precisely, the very smooth-surfaced electrodes had fewer defects than their traditionally-made counterparts. As a result, when tested, they proved to be superior at picking up glucose signals.
The 3D-printing approach additionally allows for electrodes to be custom-made for individual patients' unique biology, plus there's almost no waste, as the only material that's used goes directly into the electrodes. What's more, the manufacturing process can be carried out in a regular room, and the ink is non-toxic.
The scientists are now working on incorporating the electrodes into a wearable device. It is hoped that all of the other components of that device could also be 3D-printed, allowing the whole thing to be manufactured in a single step.
A paper on the research was recently published in the journal Analytica Chimica Acta.
Source: Washington State University