Touring kayaks are typically made of plastic, composites or sometimes wood, but unlike canoes, almost never aluminum. That didn't faze Brennen Kunka, however, who recently built his own all-aluminum kayak from the ground up – and it's awesome!
Understandably, some people might wonder what would possess someone to take on such a project in the first place.
"Before the build I had been kayaking a few times but never owned one," said Kunka, a 28-year-old mechanical designer and maker-of-stuff who lives in Powhatan County, Virginia. "I knew I wanted to build one, and whenever I make something that I could theoretically buy instead, I take the opportunity to make it unique. I've seen plenty of wooden kayaks on the internet already, and I'm probably more experienced working with metal anyway, so I decided on aluminum."
Instead of starting completely from scratch, Brennen worked from commercially available plans for a plywood kayak – he just swapped in laser-cut sheets of 1-mm 5052 aluminum alloy, which he welded and riveted instead of stitched and glued. It wasn't an easy process, though, due largely to aluminum's tendency to expand and thus distort when heated.
"Getting all of the hull sections tacked together was the longest struggle of the project," he told us. "I had a few interior frames to guide the placement, but still needed to reposition clamps for every tack, and usually support the clamps themselves to avoid bending the metal. It was super easy to burn through at this stage, and individual tacks are easy to break."
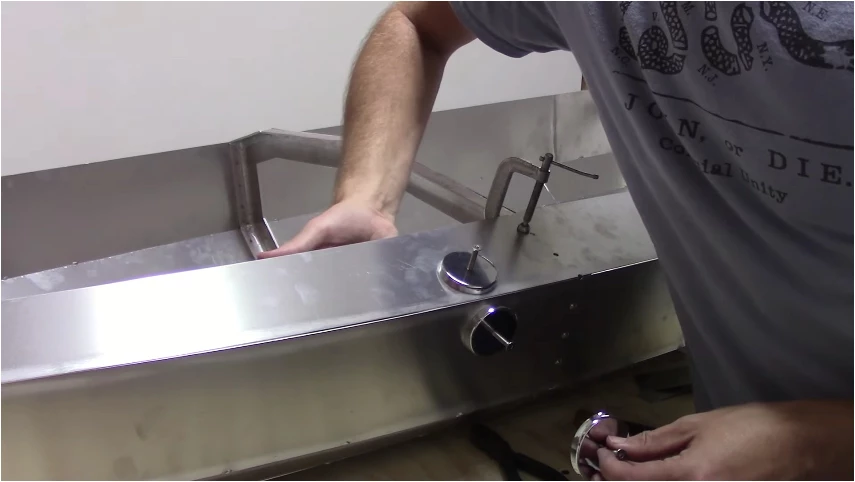
One of his particularly clever clamping arrangements – which was used to keep two adjacent aluminum panels aligned with one another while being welded – involved a steel door hinge and two magnets. The hinge went inside the kayak, pressed up against the undersides of both panels where they met, while the magnets went on the outside, holding the hinge and panels in place. He then just worked his way along the length of the panels, moving the hinge and magnets as he went.
Because the thin aluminum wasn't as stiff as plywood, the openings for the cockpit, front hatch and rear cooler receptacle(!) had to be made sufficiently rigid by adding thicker strips of aluminum around their perimeters. Likewise, two aluminum bars were added lengthwise along the interior, to keep the hull from flexing too much. Those bars doubled as the mounting points for the seat (which was made by cutting up an aluminum chair), while a separate bar spanning the space between them served as the footrest.
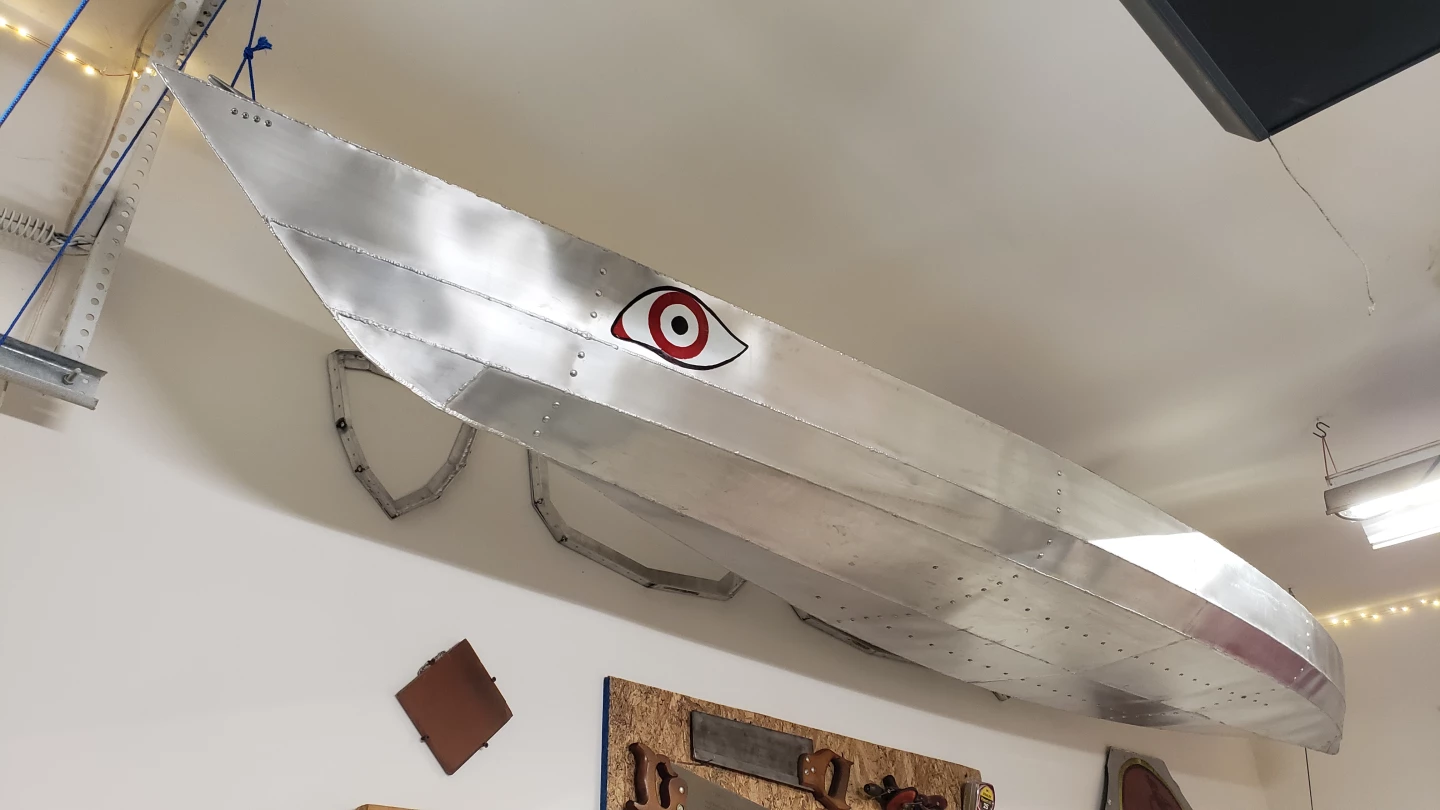
Kunka brushed the entire exterior with an angle grinder – to give it the "brushed aluminum" look – and painted the interior with Flex Seal liquid rubber to prevent leaks. The finished product, which took about eight months to build, is 12 feet long (3.7 m), 28 inches wide (711 mm), and tips the scales at only about 39 lb (18 kg) … cooler not included. But how is it on the water?
"It is very stable and handles well," said Brennen. "Everybody assumes it gets really hot in the sun, but it's fine. And the glare off of it is nothing compared to the glare off the water. One noticeable quirk is the noise. On the first paddle I heard lots of water sloshing around and thought I was sinking. Turns out that's just the noise it makes when it's moving, and the metal hull amplifies it. And when you hit a rock, everyone on the water knows it."
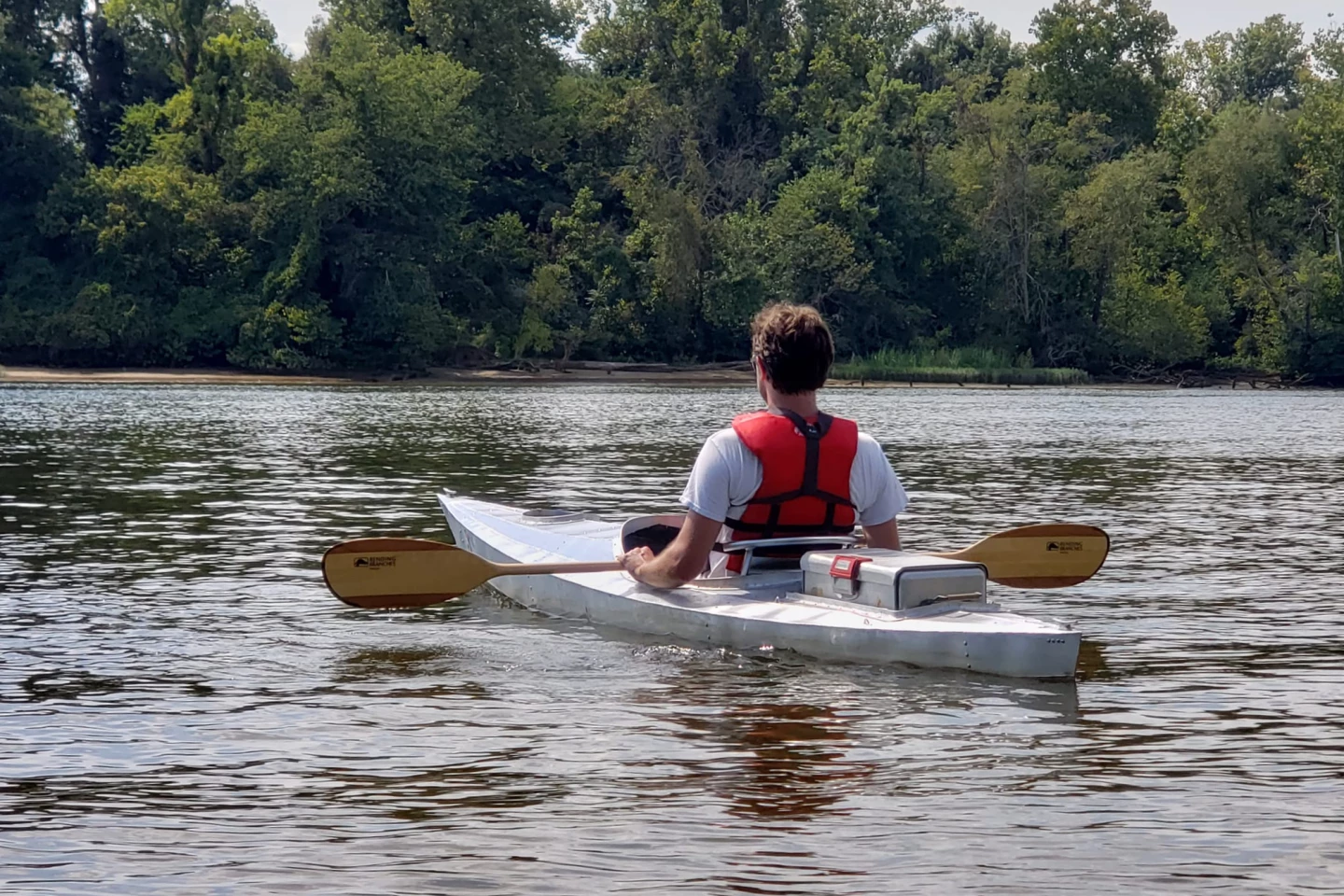
Noisiness aside, you may still be wondering why there are essentially no commercially available aluminum kayaks, whereas aluminum canoes are quite common. Well, during World War II, a great deal of aluminum was produced for the construction of aircraft. After the war ended, the extensive aluminum production infrastructure was still in place, so the metal became a popular choice for canoes – which at the time were much more popular than kayaks. This was the case up into the 1970s.
Although some companies do still make aluminum canoes, most manufacturers now go with materials that are more versatile and easier to work with. According to Brian Day, who is a sales representative with Current Designs Kayaks, there isn't much reason for kayak companies to choose aluminum now.
"Aluminum canoes were durable and affordable, but they were heavy,” he told us. "They were hot on hot days and cold on cold days. They were also limited in design by the need to join the various parts of the canoe together with rivets […] An aluminum kayak would share the same materials challenges faced by aluminum canoes – mainly in joining together the various parts of the hull and deck. This would require either welding or riveting, both of which would be time-consuming and expensive. Tooling to mass produce aluminum shapes is also extremely expensive, this is a real challenge in producing a commercially viable design."
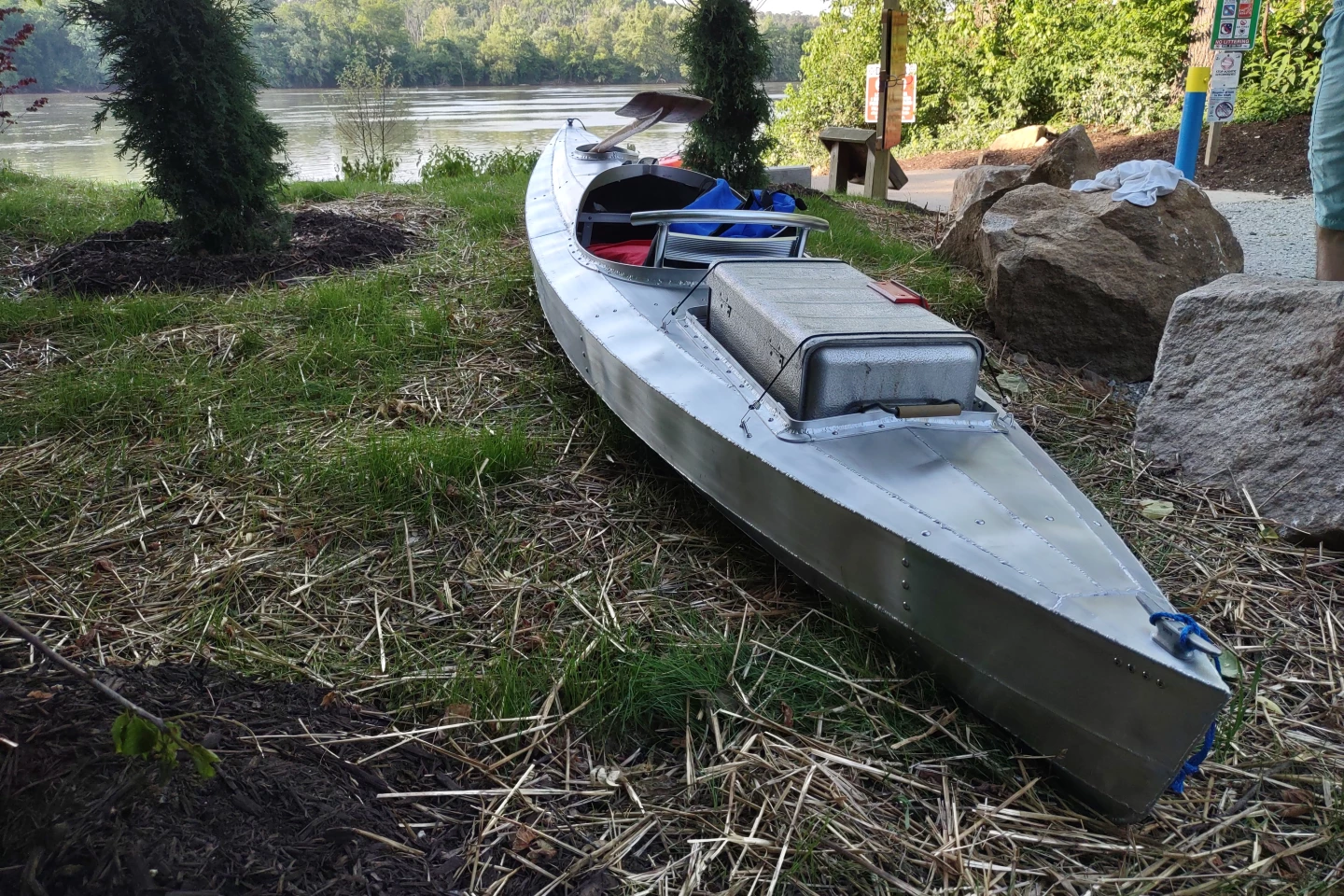
Kunka agrees that aluminum probably doesn't make sense for large-scale production, but notes that it still does offer some advantages.
"Unless you count the cool factor, there's not much about my aluminum kayak that's 'better' than many plastic ones," he said. "It's lighter than a rotomolded one but probably not carbon fiber. Of course, aluminum is fully recyclable, can be repaired to its original strength with welding, and is produced with electricity that can be sourced from renewables."
You can see a detailed account of the building of his kayak, starting with the video below. Subsequent videos document the later stages of the build, and show how the boat performs on the river.
And finally, should you really want an aluminum kayak of your own – but don't want to spend eight months building it – Osagian Canoes does make an interesting little … something called the 12 Solo.1. It has been described as a kayak, although its overall form is more like that of a canoe.