One factor limiting the output of today's power stations is the metals used in the blades, bearings and seals of their steam turbines, which tend to soften and elongate well before their melting point. Solve these problems, and you could conceivably raise temperatures on anything that converts heat to electricity using a steam turbine, with a resulting boost in efficiency and a reduction in waste heat being lost.
Researchers at Sandia Labs, Ames National Laboratory and Iowa State University say they've created a 3D-printable high-performance superalloy that's stronger and lighter than the state-of-the-art high-temperature alloys used today. They've published their findings in the journal Applied Materials Today.
Composed of 42% aluminum, 25% titanium, 13% niobium, 8% zirconium, 8% molybdenum and 4% tantalum, this material is an example of a "multi-principal-element superalloy," or MPES. Most alloys are made chiefly out of one primary element, combined with low concentrations of other elements to boost certain properties, but multi-principal-element alloys have high concentrations of three or more elements.
According to the research team, a wide variety of these alloys are showing great promise on a number of metrics; strength-to-weight, fracture toughness, corrosion and radiation resistance, wear resistance, and others. But the MPES subset this team has explored excels at high strength in high-temperature situations.
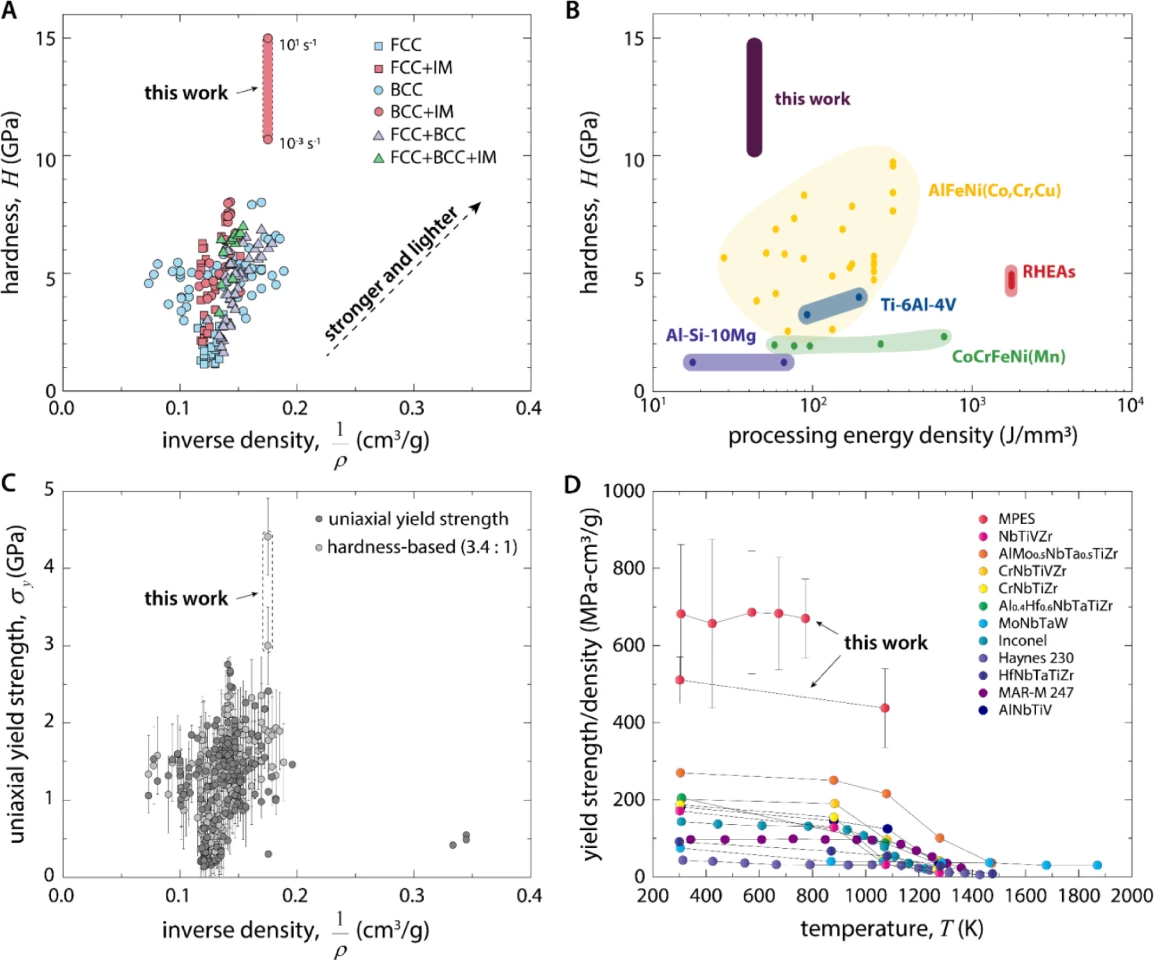
"The specific strength of the MPES based on the ratio of hardness and density is 1.8–2.6 GPa-cm3/g," reads the study, "a value that surpasses all known alloys, including intermetallic compounds and legacy titanium aluminides, refractory MPEAs, and conventional Ni-based superalloys. This specific strength is a 300% improvement over Inconel 718 based on measured peak hardness [28] of 4.5 GPa and density of 8.2 g/cm3, which gives a ratio of 0.55 GPa-cm3/g."
It's also designed specifically to be 3D-printable in powdered form, enabling it to be laid out in "unusual nanoscale microstructures" that the research team found were "insensitive to exposure at 800 °C [1,472 °F] for one hour" – considerably hotter than the 570-odd °C (1,058 °F) at which a typical coal-based power plant runs.
Indeed, the 3D printing process accepted "compositionally segregated, high-impurity" powdered feedstock – the printer itself mixed the alloy as it melted the component metals.
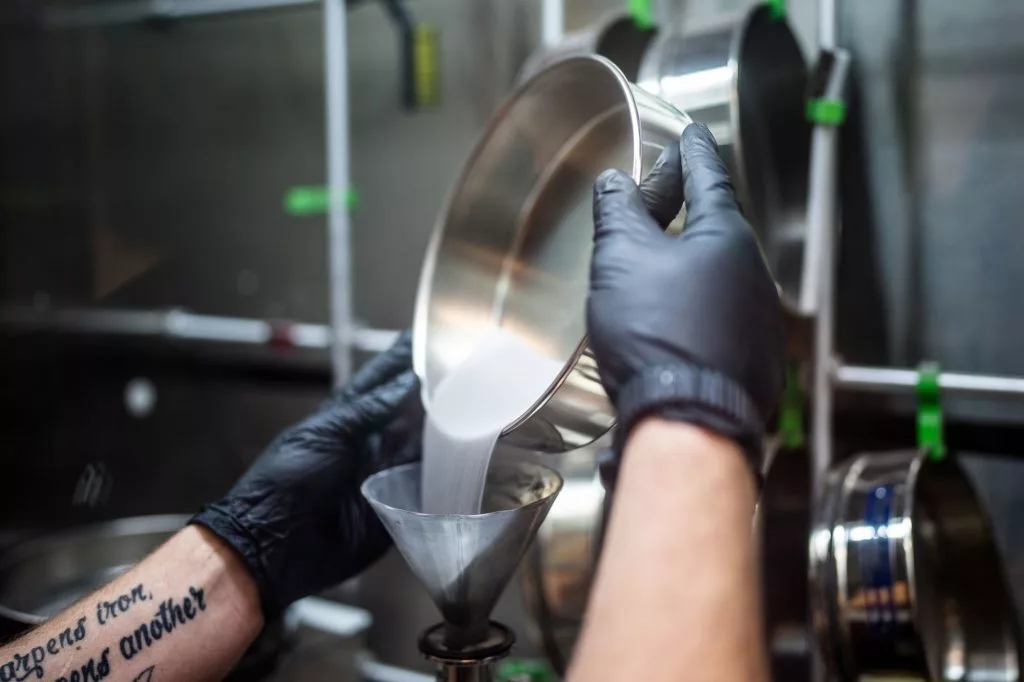
The researchers say this work points to a larger class of MPES materials ready to be explored, with immediately interesting potential in aerospace as well as energy. They warn that further work on the 3D printing process is needed before they'll reliably be able to produce large parts in these alloys without microscopic cracks, and that the feedstock includes some fairly expensive metals that'll make this particular MPES tough to scale up for broader use in applications where cost is a high priority.
“With all those caveats, if this is scalable and we can make a bulk part out of this, it’s a game changer,” says Sandia scientist Andrew Kustas in a press release. “We’re showing that this material can access previously unobtainable combinations of high strength, low weight and high-temperature resiliency. We think part of the reason we achieved this is because of the additive manufacturing approach.”
The study is open access in the journal Applied Materials Today.
Source: Sandia Labs