Among the almost limitless use cases for commercial-scale graphene is filtration. MIT engineers say they've now developed a scalable production process for precisely tailored graphene filtration membranes, which could see action in desalination, biological separation and other applications.
Graphene is an ultra-light, ultra-strong, super conductive, transparent carbon allotrope that resembles a chicken wire lattice at the atomic level, one that makes it impervious to even the tiniest of atoms – helium. Thus, with the right-sized holes poked in it, it can be tailored to filter out specific molecules very effectively.
The problem has always been manufacturing the damn stuff, particularly at any kind of scale, because graphene needs to be grown under very particular conditions. And that's what an MIT team believes it's cracked, using a roll-to-roll approach that's already producing up to 10 m (33 ft) of continuous graphene at a time, at a rate of 5 cm (2 in) per minute.
The process uses chemical vapour deposition, spooling a length of copper foil between two rolls and passing it slowly through two tubes. The first tube heats the foil to an ideal temperature, and in the second, a specific ratio of methane and hydrogen gas is pumped in. When this gas mixture hits the heated foil, graphene begins to form.
"Graphene starts forming in little islands, and then those islands grow together to form a continuous sheet," says John Hart, associate professor of mechanical engineering and director of the Laboratory for Manufacturing and Productivity at MIT. "By the time it's out of the oven, the graphene should be fully covering the foil in one layer, kind of like a continuous bed of pizza."
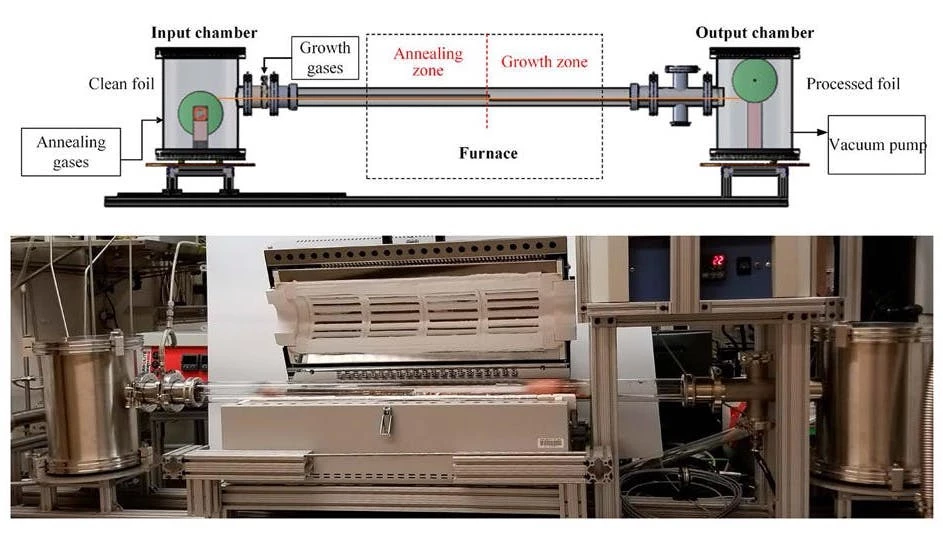
Once it's rolled up onto the second spool, the graphene-coated foil is cast with a polymer mesh, and the copper foil is etched away to free the graphene.
"If you don't support graphene adequately, it will just curl up on itself," says lead author Piran Kidambi, a former MIT postdoc who is now an assistant professor at Vanderbilt University. "So you etch copper out from underneath and have graphene directly supported by a porous polymer – which is basically a membrane."
The team tested the graphene membranes by passing water, salts and other molecules through them, and found the material's performance "comparable to graphene membranes made using conventional, small-batch approaches."
While the polymer casting procedure is currently done by hand, the team believes it could eventually be incorporated into the roll to roll system, making the procedure even faster and more automated.
The video below shows the system, which is detailed in a paper appearing online in the journal Applied Materials and Interfaces.
Source: MIT