If someone does a lot of arm curls at the gym, the typical result is that the bones and muscles in their arms will get stronger. Recently, researchers at Houston's Rice University inadvertently created a nanocomposite that behaves in the same way. Although the material doesn't respond to static stress, repeated mechanical stress will cause it to become stiffer.
The discovery was made in the lab of Pulickel Ajayan, Rice professor of mechanical engineering and materials science, and of chemistry. Graduate student Brent Carey had created a composite material by infiltrating a batch of vertically aligned, multiwalled nanotubes with polydimethylsiloxane, which is an inert, rubbery polymer. He was testing the high-cycle fatigue properties of the composite, and was surprised to discover that instead of weakening when subjected to repeated loads, it actually got stronger.
Over the course of a week, the material was subjected to 3.5 million compressions. This caused its stiffness to increase by 12 percent, with indications that there was potential for further stiffening. The reason for this type of reaction is still something of a mystery.
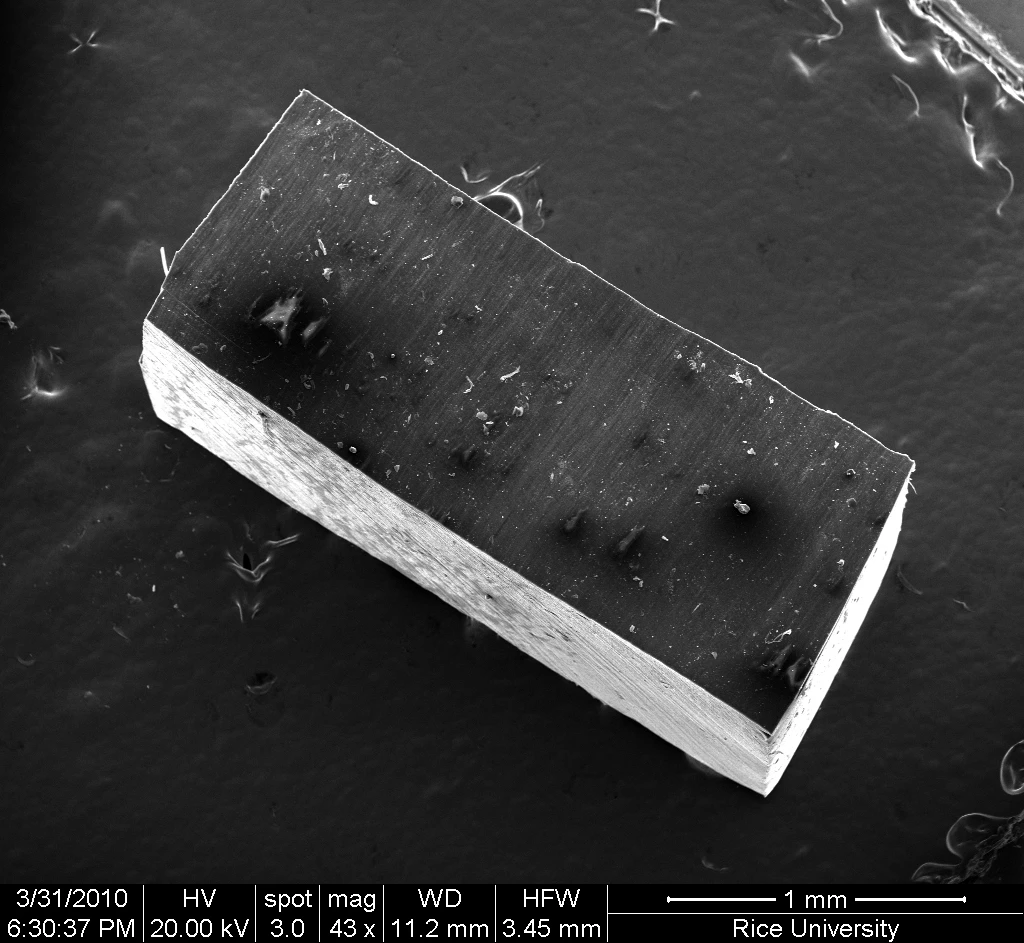
(Image: Ajayan Lab/Rice University)
"We were able to rule out further cross-linking in the polymer as an explanation," said Carey. "The data shows that there's very little chemical interaction, if any, between the polymer and the nanotubes, and it seems that this fluid interface is evolving during stressing."
What is known is that the use of nanomaterials greatly increases the surface area available to that fluid interface, so whatever reaction is taking place is much more pronounced than would be the case with a conventional composite.
Carey is already envisioning potential uses for materials utilizing the process. "We can envision this response being attractive for developing artificial cartilage that can respond to the forces being applied to it but remains pliable in areas that are not being stressed," he stated.