A Tel Aviv-based company is making a push to revolutionize the architecture of future automobiles. REE has developed a massively modular platform that squeezes the entire motor, transmission, steering, suspension, brakes and more into the wheel bay, enabling a full range of vehicle types.
REE CEO and co-founder Daniel Barel has been through a number of startup phases, most notably bringing the SoftWheel to market internationally. But for the last six or so years, he and the REE team have been in stealth mode working on a completely new approach to the entire automotive segment, that could prove to be his biggest contribution yet.
Electric cars, thought Barel, shouldn't be constrained by the forms and solutions that combustion cars have evolved into over more than a century of development. Old-school mechanical thinking around steering, motors, transmissions and suspension is due for a complete re-think – the kind of re-think that's too revolutionary to come from within the automotive industry itself.
So Barel began assembling a team to pull off an audacious plan: to develop a completely modular, hyper-flexible electric vehicle platform that could be used for anything from a golf kart, a supercar or a delivery van to a 10-ton truck or a high-performance off-road vehicle. And to completely clear out all the space under the hood, handling every mechanical function from steering and suspension to motor, transmission, brakes and cooling in a super-compact, modular unit that lives in each wheel bay.
Barel tells us over the phone from his office in Tel Aviv that the architecture is based on four pillars. First, modularity, to allow a virtually limitless scope for future improvements. Secondly, a tiny footprint, allowing vehicle designers totally flexible access to the maximum possible amount of space above what is truly a skateboard chassis. Third is energy-efficiency, to maximize the range possible from a battery charge, and fourth is lightweighting, including the reduction of unsprung mass.
"There's an economic driver there too," says Barel. "The single biggest expenditure for an OEM auto manufacturer is the platform, developing and validating it. It costs billions, it takes years, and each OEM has between two and six platforms at any given moment, and two or three in development.We went in and said 'what if you might need only one? That might be worth something.'"
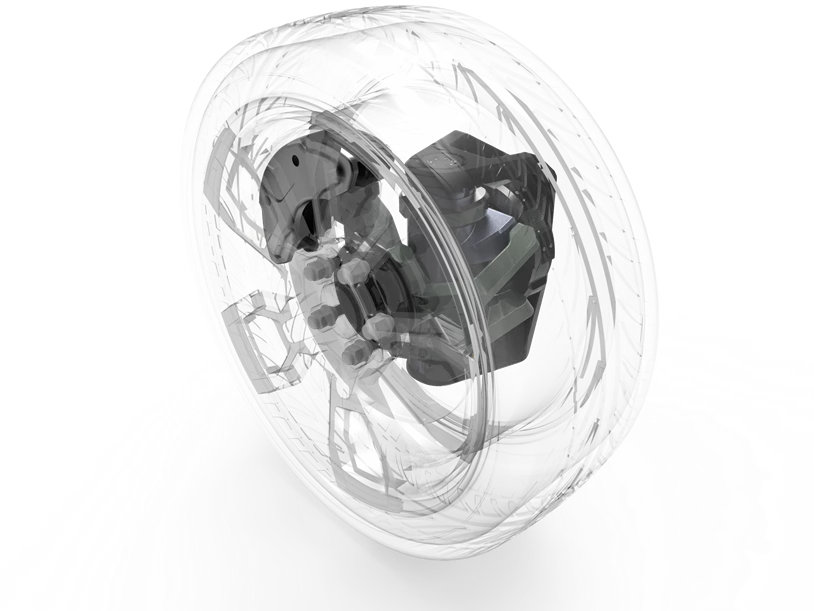
The REE solution is difficult to describe, because it's so modular that it's hard to pin down specifics. Basically, each wheel sits on a lightweight rim, connected via a super-compact suspension and steering system to an equally compact electric motor and transmission.
Nothing takes a direct mechanical or hydraulic input from the driver. Everything is electronically actuated, with a raft of sensors on board each wheel unit to feed information back into the system's brain.
How do the suspension and steering work? "We need to understand that the entire core of this technology is modular," says Barel. "We've built an array of capabilities. So we have many types of suspension: passive, semi-active, active, active through the dampers, rotary dampers. We have four different types of steering, all steer-by-wire. Single wheel steering, adaptive steering, so on and so forth. It can be front wheel drive and front wheel steering, or all wheel drive and all-wheel steering. It depends on the application you need."
Is this anything like a hub motor? Absolutely not, says Barel: "Hub motors have been around for a while, but according to our beliefs, they're not suitable for automotive for three main reasons. One: they're very prone to damage, sitting at the wheel. Two: you have to spin them at the same RPM of the wheels, meaning low RPM and high torques – which is exactly the opposite of what you want to do. And thirdly, they increase the unsprung mass of the vehicle – which you don't want to do. We're dramatically reducing the unsprung mass. The configuration that we've built, most of the components come after the suspension.
"Everything in our system is connected through a very unique – and patented, of course – gearbox, or drivetrain, that can allow for vertical movements while maintaining peak performance. If you think about a car today, you might think about a half-shaft, which is usually how you transfer torque. Those usually lose about 8 percent of their torque capability where they reach the top and bottom of the suspension stroke and create the largest angles. Our technology does not suffer from those scenarios, it remains just as efficient throughout the suspension travel."
Why use transmissions instead of the direct drive many electric vehicles are using today? The answer is efficiency. Low-torque, high-RPM electric motors, says Barel, give better efficiency, and running them through a super-compact transmission allows high-torque, low-RPM output through the wheels.
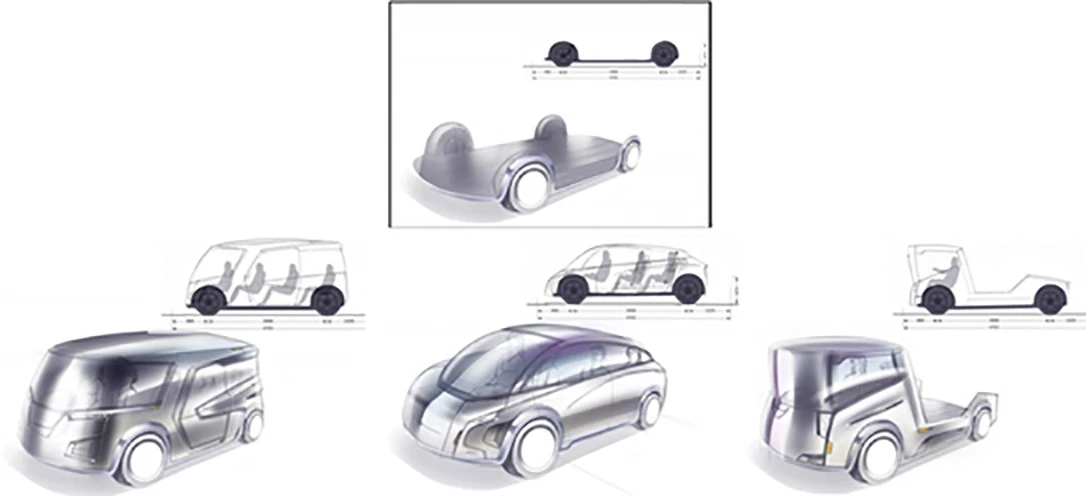
What each wheel module will look like is entirely dependent on the application. REE says that with one configuration, you could have yourself a hard-charging electric sportscar capable of doing 0-60 mph (0-98 km/h) in three seconds flat. With another, you could have a super-tough 4x4 off-roader with 240 mm (9.5 in) of travel in a fully active suspension system. The system doesn't care, it merely needs to know what modules it's got at its disposal.
Nor does it care if there's a human driver involved or a steering wheel installed. All that goes into each wheel unit is a power cable, which can accept electrons from a battery, a fuel cell, or whatever other source you care to name, and a data cable. If it's a human driver requesting extra power and a 32 degree turn to the left, fine. If it's an autonomous system, no problem.
Servicing these vehicles will be a doddle. Lift them up, take the wheels off, pull out the entire wheel module and repair or replace whichever bits are necessary.
Barel says the REE team developed the concept for nearly five years before taking it to show tier-one and tier-two automotive manufacturers. "Seriously, we were really just hoping they'd take our call and not laugh too hard. We thought it could work, but nobody from the real auto industry had ever looked at it, outside the team.
"To our amazement, they didn't just take the call. Not only did they like it, but they actually asked to invest in us and be our partners in R&D and production for the future – in a very aggressive, untypical way for us. At that point, we understood that we'd hit the spot. That we've got something nobody else has, that can power the future of EVs."
At this point, with a range of prototypes already built to validate and demonstrate the technology, the company is actively collaborating with Mitsubishi, Musashi, Linamar, Tenneco and NXP, as well as other "leading OEMs." Barel says he expects the first REE-architecture vehicles to begin hitting the market around 2023.
"I think autonomous delivery will be the first, because of the low speed vehicle regulations that are out there allowing for a faster adoption rate," he tells us.. "Then I believe we're going to see commercial vehicles – because we save about 50-70 percent of volume, you can put 50-70 percent more goods on top of the same footprint compared to a combustion powered van. That's a strong incentive for business."
Barel firmly believes this kind of disruptive design could only have come from outside the industry. "Our relative ignorance of the automotive world – we didn't come from 30, 40, 50 years of hardcore automotive – that was our biggest strength. We're not confined in the old concepts and paradoxes of how things should look, and how things should work.
"If you think about an average gearbox, it's quite big. It might weigh 100 kg, maybe 200. It's about a meter in length, maybe a meter and a half, depending on the gear ratios and whatnot. And yeah, you can make incremental changes and improvements to that design. Make it a bit smaller or a bit lighter.
"But you can never get to a 6 kg, 16 cm width of a gearbox by doing that. That's our gearbox, which outperforms all gearboxes today. Of course, that's fully validated by the industry. This is just an example. We're looking at the technology from a completely, completely new and fresh approach."
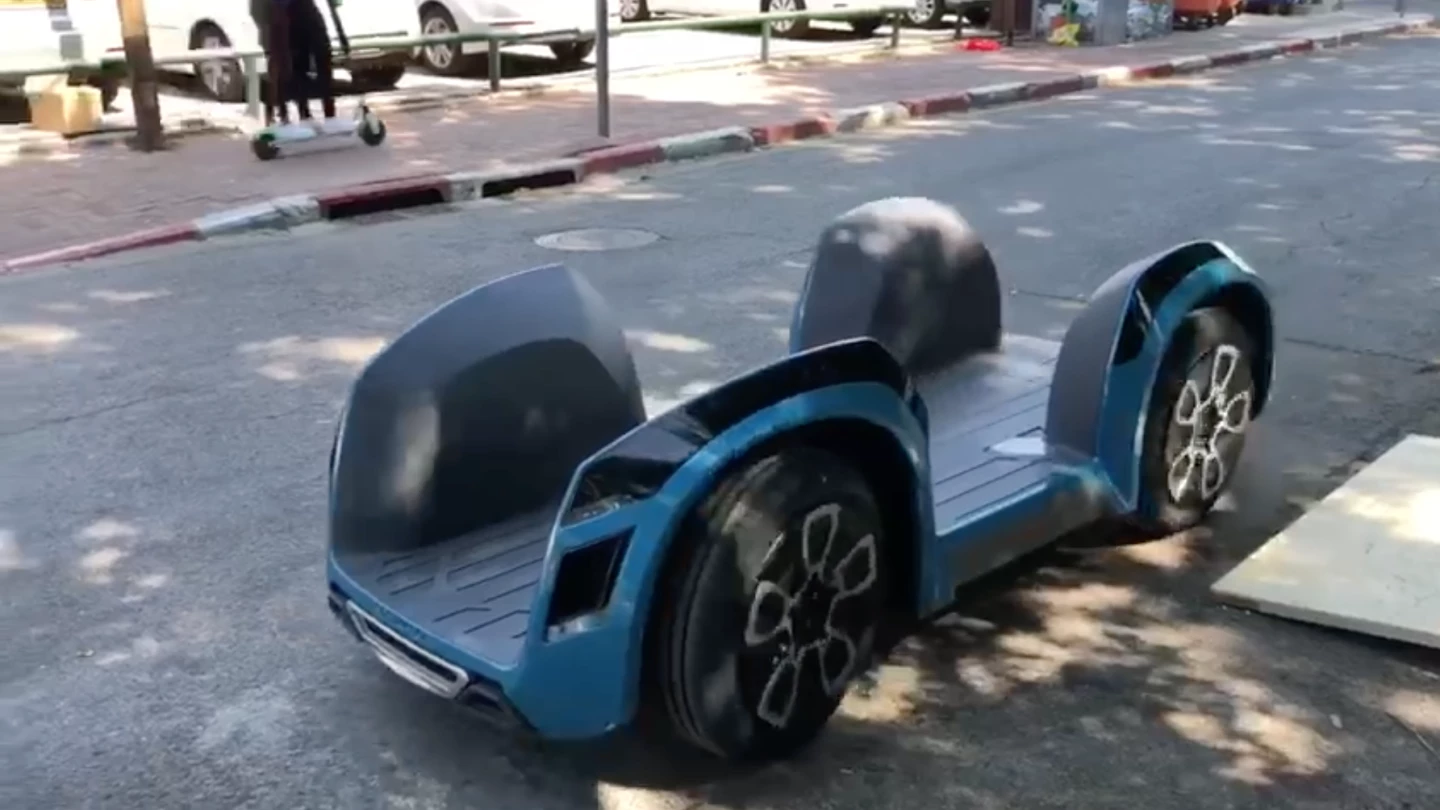
We look forward to learning more about REE's potentially disruptive auto architecture as it develops and moves toward the market. At this stage we've only seen a very short video of one of the prototypes, pictured above, and can confirm that it certainly seems to use high-RPM motors, given the high-pitched sound it makes as it moves. We have requested more information, diagrams and photos from REE and hope to bring them to you soon.
Source: REE