Thanks to gyros, accelerometers and sophisticated control mechanisms, remaining upright on a two-wheeled vehicle is no longer quite the balancing act it might once have been, even when at a standstill. Visions of future mobility like Honda's U3-X take such ideas in whole new directions, quite literally, by including multi-directional capabilities, and concepts such as Supple go even further still by ditching wheels altogether in favor of balls. It's this freedom of movement that inspired a group of students from the Charles W Davidson College Of Engineering at San Jose State University to begin work on the ambitious Spherical Drive System (SDS) electric motorcycle.
The SDS concept vehicle is described as a self-balancing electric motorcycle that rides on spheres. Rather than using the kind of mechanical gyros that help keep the Gyrobike or the C-1 from Lit Motors in an upright position, the SDS creation uses data from MEMS gyroscopic sensor technology and an onboard accelerometer to electronically control balance.
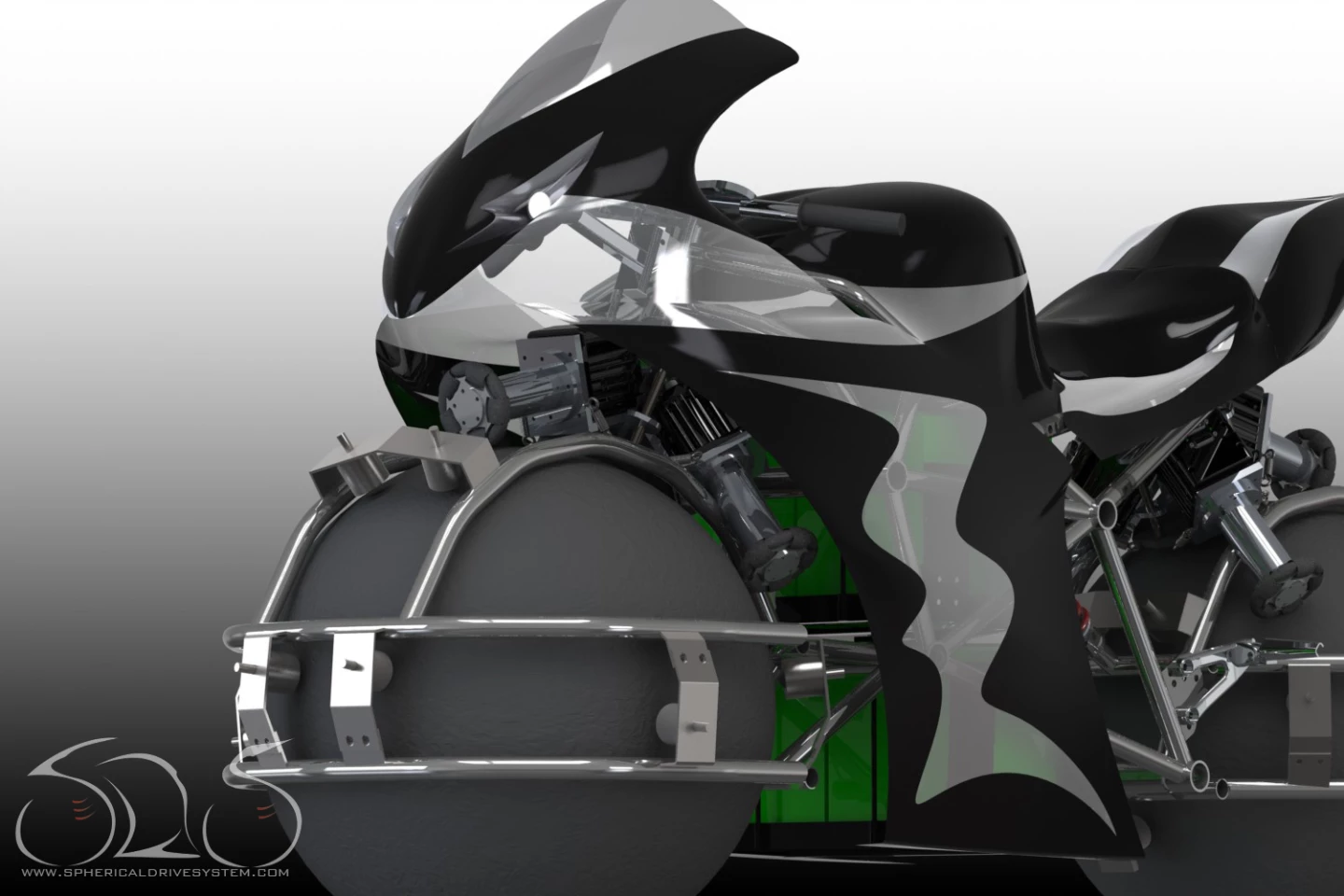
"The motorcycle operates on a friction based drive system that directly drives the surface of the sphere with custom manufactured omniwheels, attached to Animatics motors," explained team leader Max Ratner. "The method for balancing the motorcycle is similar to a Segway in that it uses accelerometers and gyros for detecting the pitch angle and correcting for any displacement from vertical. The user will control the motorcycle just like any modern motorcycle with a throttle, leaning, and handlebars. Additionally, there will be a set of joysticks that will allow for additional maneuvers such as forward/reverse/side-to-side motions/spinning the vehicle."
The electric bike's three-motor drive system that gives the vehicle its potential to move in any direction is modeled after a system known as an inverted pendulum, and features omniwheels made from zinc-coated 4130 steel and Animatics Smart motors powered by Lithium Iron Magnesium Phosphate batteries with a built-in battery management system. The rather shiny frame is fashioned from 304 stainless tubing, and there's suspension front and rear in the shape of Fox racing shocks.
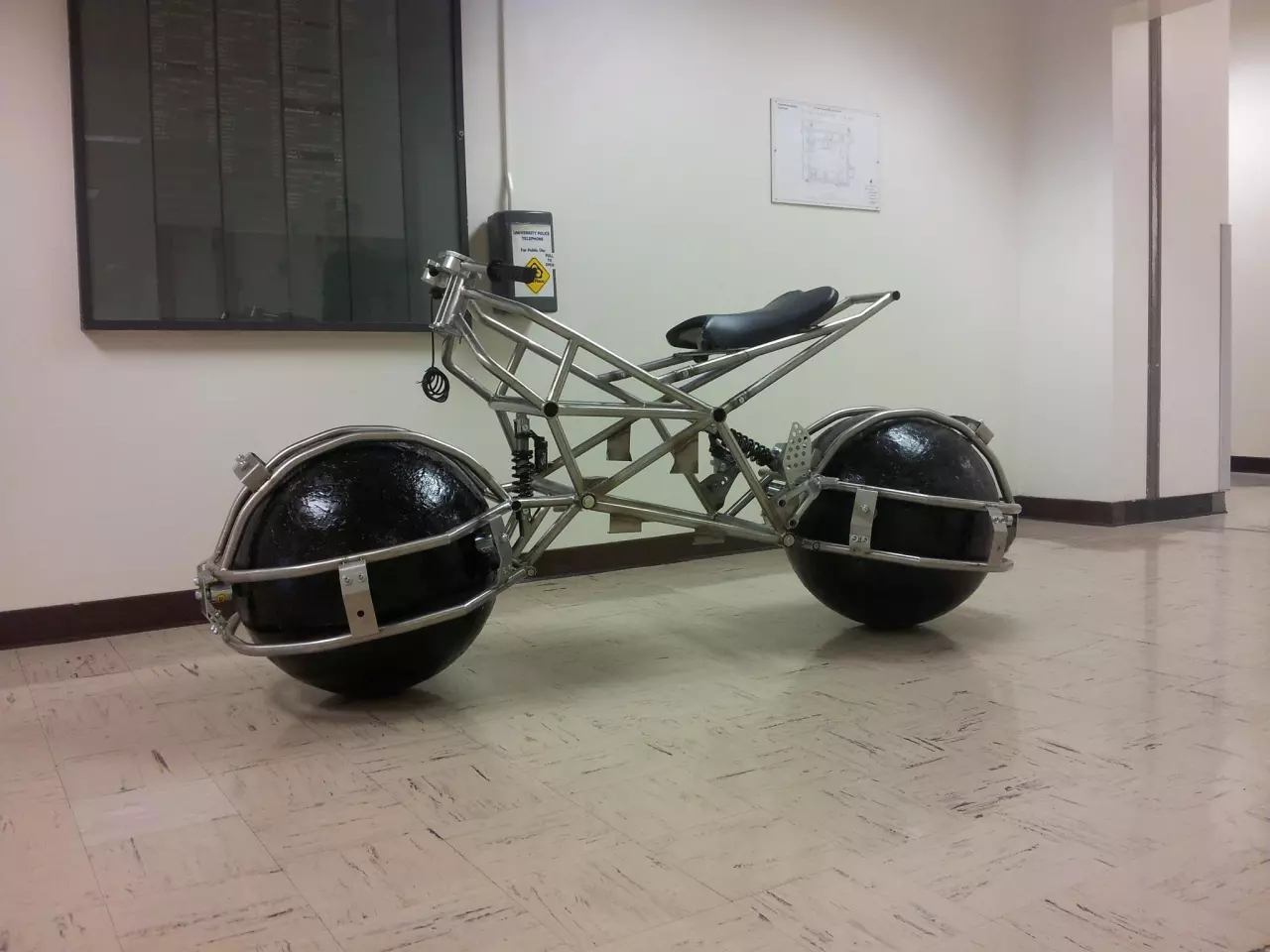
The vehicle's computer-controlled operation (much of which is undertaken using an ARM architecture microcontroller) should help keep bike and rider safe, but if the vehicle were to leave the ground for any reason, the spheres will remain contained within the swingarms. Ratner told us that the "spheres are essentially carbon fiber and fiberglass shells, coated with a durable industrial rubber for traction."
The SDS motorcycle is still very much a work in progress and, now that original team members have graduated, only Ratner, Henry Li and Andrew Parmar remain on the project full time. The initial aim is to get the vehicle stable and in control at speeds up to about 10 mph (16 km/h) but the designers say that, in theory at least, it could zoom up to 60 mph (96.5 km/h).
There is still quite a bit to do before then, however. Ratner confirmed that "the vehicle is about 85 percent assembled in terms of hardware and about 20 percent done in terms of software and electrical. We have about 90 percent of our parts."
Work on the control system is currently being undertaken by three new recruits from San Jose State University (Lynn Comiskey, Evan Ly and Jessica Chen) as part of their own class project.
"The challenges posed by the control system include an attempt to balance an inherently unstable system, interfacing with multiple drive motors, and combining potentially noisy sensor readings such as those from an accelerometer into something usable and reliable," Ratner told us. "The control system has been proved out on our test rigs but there is quite a bit of stuff to change in the code to make it applicable to the final bike. This testing will likely happen around the end of 2012."
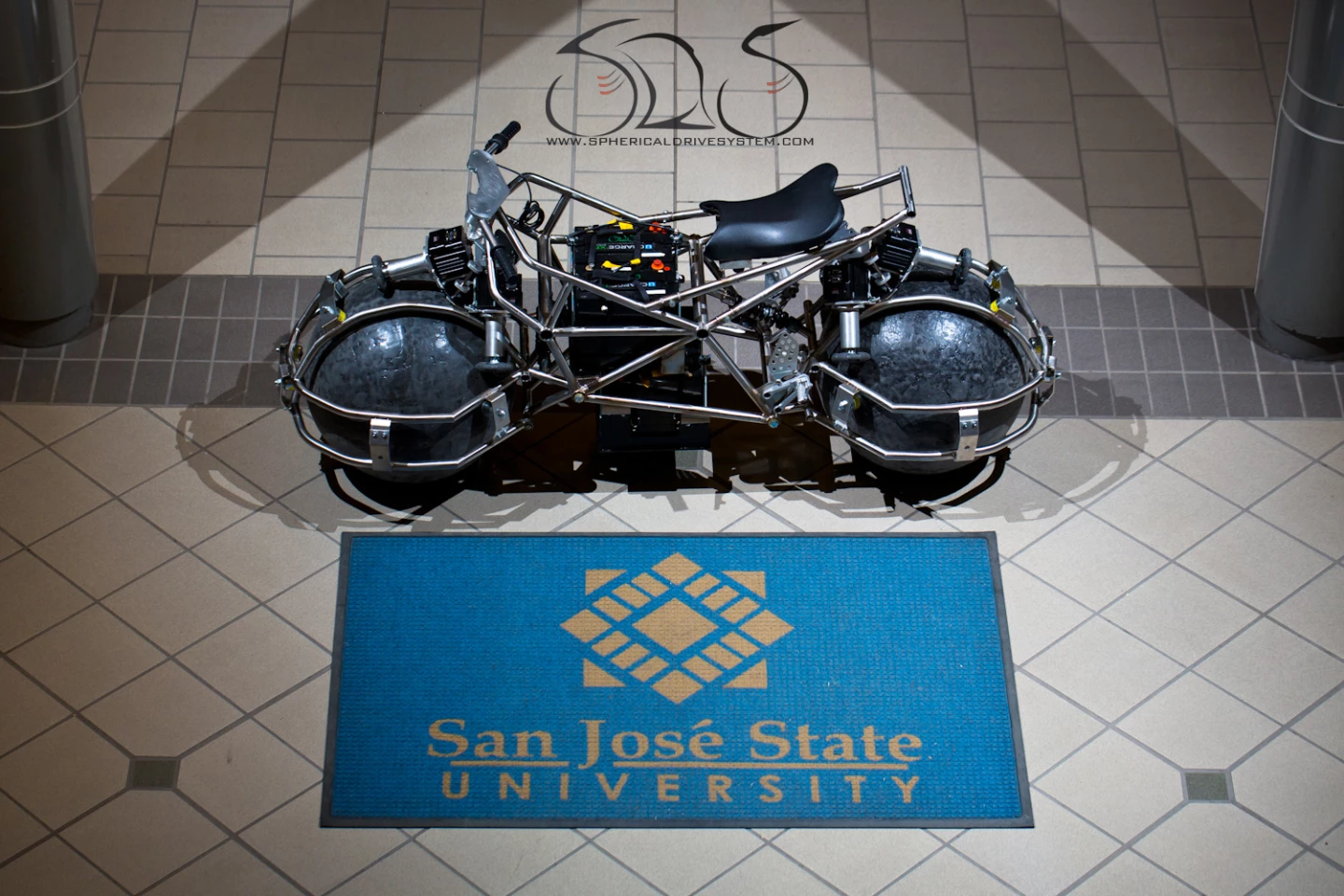
Backing from companies and organizations like Animatics, Wolfe Engineering, Atmel and IEEE has helped toward meeting project costs, and the team is presently on the lookout for sponsors to help mold and manufacture the fairings that will hide much of the exposed workings and help enhance the vehicle's already striking appearance.
Source: SDS (and you can follow project progress via the SDS Facebook page) via The Kneeslider