Scientists have developed a new "ink" that allows objects to be 3D-printed out of wood. The material could reduce the amount of wood that gets wasted in the manufacturing of various products, plus it could utilize existing wood waste that would otherwise end up being burned or dumped.
First of all, the use of wood in 3D printing media isn't a new idea.
Among other things, we've previously seen wooden-ish objects printed out cellulose derived from wood, along with a 3D-printed guitar made of sawdust mixed with a bio-epoxy resin. Scientists at MIT are even developing a method of growing lab-cultivated wood into predetermined three-dimensional shapes.
Researchers at Houston's Rice University, however, are claiming that they are the first people to 3D-print truly wooden objects out of a material made up solely of wood's natural components.
Along with water, the viscous ink consists of cellulose nanofibers, cellulose nanocrystals, and lignin – the latter is a type of organic polymer that makes up much of the support tissue in plants, including trees. Both cellulose and lignin can be harvested from wood waste generated by the forestry, construction and consumer goods industries.
The wood ink is used to build objects up in successive layers via a 3D printing process known as direct ink writing (DIW). This is similar to the commonly used fused deposition modeling (FDM) technique, in which a molten material is extruded from a nozzle and then allowed to harden as it cools. In DIW, instead of cooling, the material is rendered into solid form via a sintering process.
For the wood ink, the sintering process involves freeze-drying the printed objects at -85 ºC (-121 ºF) for 48 hours, then heating them at 180 ºC (356 ºF) for 20 to 30 minutes. The heating step converts the lignin into a "molecular glue" that binds the cellulose fibers and crystals.
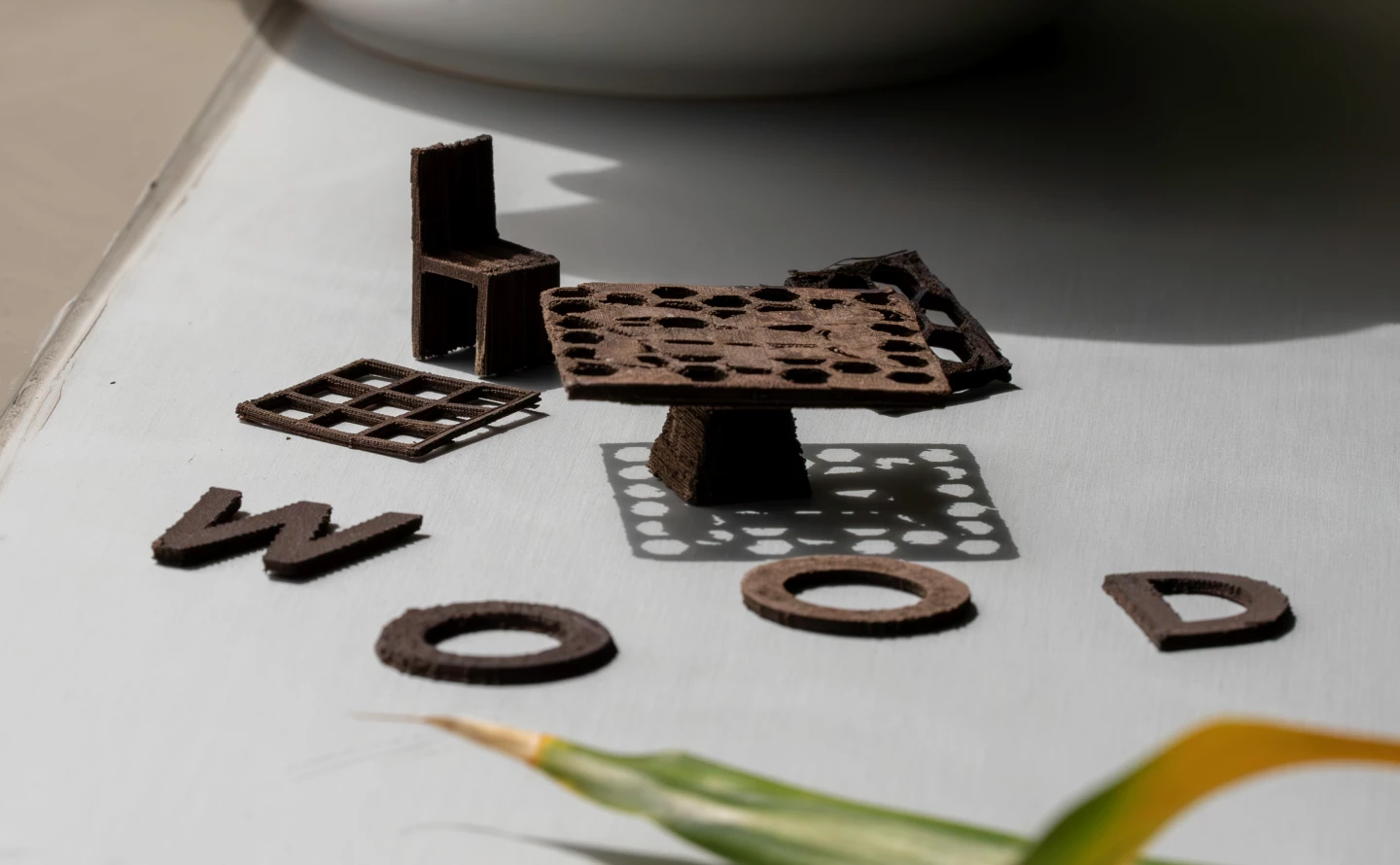
Small objects printed out of the material are reportedly quite similar to natural wood in appearance, structure, texture, thermal stability and even scent. They're also mechanically stronger than natural balsa wood, which was used as a baseline in the study. And as an added bonus, they will biodegrade when discarded.
More importantly though, when an item is printed out of the ink, only the exact amount of ink required to print that item is used. By contrast, when an object is carved or milled from a block of natural wood, all of the removed wood goes to waste.
"The ability to create a wood structure directly from its own natural components sets the stage for a more eco-friendly and innovative future," said the lead scientist, Asst. Prof. Muhammad Rahman. "It heralds a new era of sustainable 3D-printed wood construction."
The scientists do admit that the freeze-drying and heating steps in the process are energy-intensive, so they are exploring alternatives. A paper on their research was recently published in the journal Science Advances.
Source: Rice University