Having received permission from Austrian authorities to begin outdoor flight testing on its remarkable CycloRotor-propelled technology demonstrator, CycloTech has announced noise testing results for its 360-degree thrust vectoring propulsion barrels.
CycloTech is one of very few companies looking beyond the humble propeller, pitch-controllable rotor or ducted fan to provide thrust for electric VTOL aircraft and drones. Instead, it uses a series of spinning barrels.
These CycloRotor barrels are known as Voith-Schneider propellers, and they spin at a reasonably constant rate when an aircraft is off the ground, rather than needing to constantly speed up and slow down like the propellers on a drone do to keep it balanced in changing wind conditions.
Instead, the walls of the barrels are a series of blades, and these blades can be pitch-controlled throughout the rotation of the barrel, allowing for near-instant changes in the magnitude and direction of thrust through 360 degrees.
Blade pitch control is handled by a central hub that works a bit like the swashplate in a helicopter; when it's moved off-axis, it changes the pitch of all blades as the barrel rotates, such that the thrust remains constant when the hub is staying still.
One advantage of this kind of idea is that it doesn't necessarily require electric motors spinning the barrels, because it doesn't need massive amounts of instant torque to stabilize an aircraft. You could run the thing on combustion engines, and presumably make yourself a much longer-endurance aircraft.
Progress hasn't exactly been at lightning speed here. CycloTech made the first tethered flights (above) with its 83-kg (183-lb) technology demonstrator more than a year and a half ago, and since then, it's been radio silence apart from a super-weird cargo drone concept it put together in conjunction with Japanese delivery company Yamato.
But there are two bits of recent news worth mentioning. Firstly, in March, CycloTech announced it had received permission from Austro Control, the Austrian aviation safety authority, to start flying the demonstrator outside.
“The Operational Authorization for the outdoor flight test campaign is a major milestone and will be key to demonstrate the CycloRotor technology to the aviation world.” said Deva Harsha Yarramshetti, Flight Test Engineer at CycloTech, in a press release.
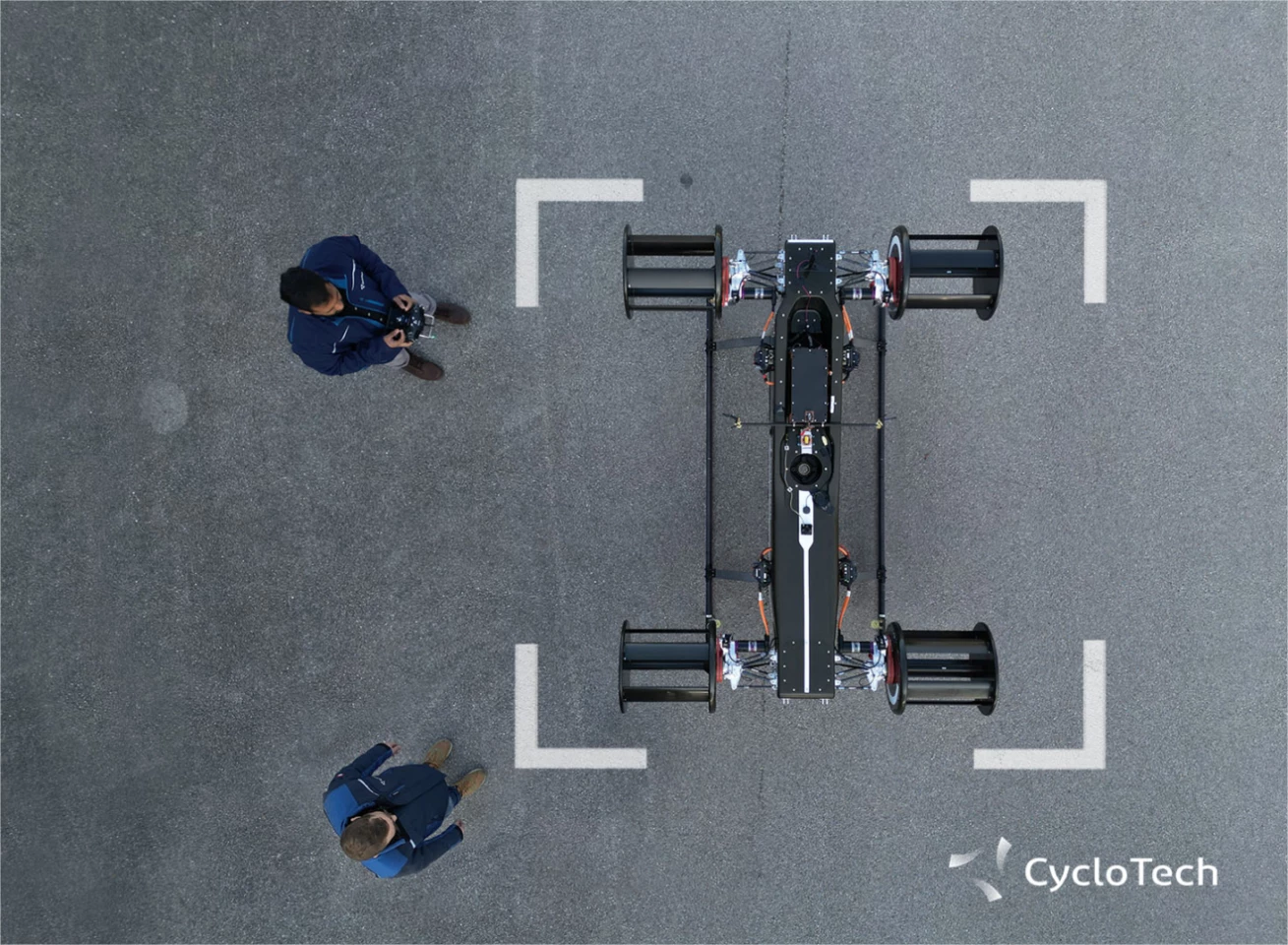
And now, the company says it's completed an extensive outdoor noise testing campaign for the propulsion system at the Wels General Aviation Airport in Austria.
Noise is crucial to eVTOL aircraft designs. If they're going to democratize vertical flight and become the ubiquitous air taxis of the world, they need to be vastly quieter and cheaper than helicopters. So CycloTech stuck a propulsion barrel on a test stand and took a bunch of readings, reporting that "the CycloRotor generates a sound pressure level of 59 dBA at a distance of 100 meters (328 ft), which is equivalent to the level of a typical conversation between two people."
It's hard to put this result in context, though. For starters, the barrel was mounted on a vertical axis, so the thrust couldn't be vectored downward like it'd typically be in any eVTOL aircraft. Secondly, it's not clear which direction it was vectored toward relative to the microphone array.
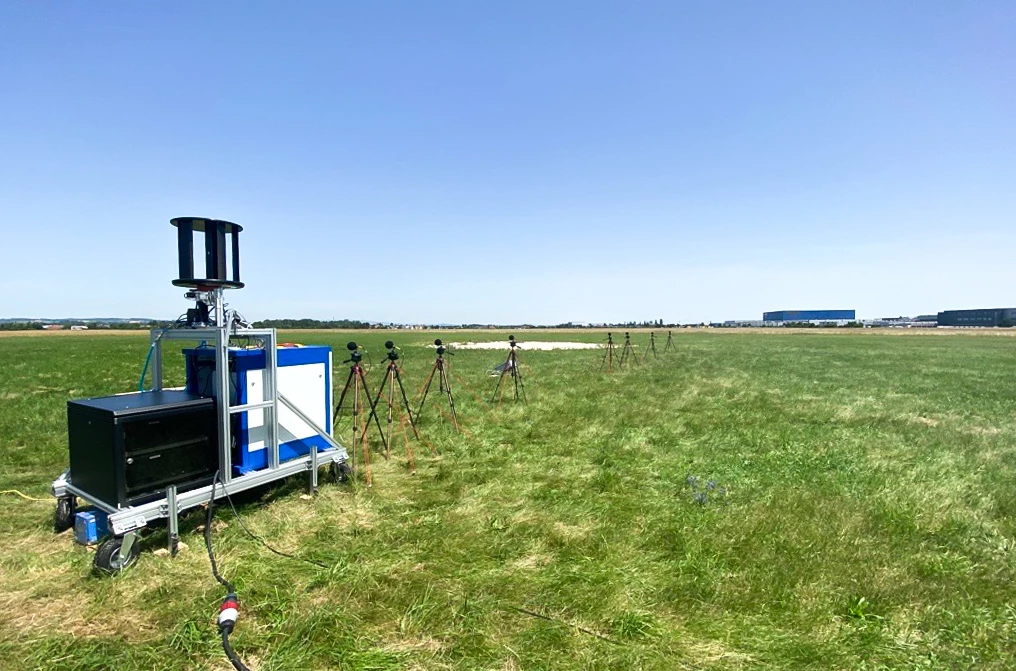
Thirdly, well, there was only one of them, where a full-sized eVTOL aircraft will probably run six or eight for the sake of redundancy. And it was also a fairly small one – presumably, the CR-42 CycloRotor, whose maximum thrust of 253 N (~57 lbf) is nowhere near what each of a Joby S4's big tilting propellers put out.
We bring up the S4 because back in May last year, Joby became the first eVTOL company to release genuine noise figures for a full-size air taxi prototype. Working with a team from NASA, Joby measured the S4 from the same 100-m distance as CycloTech, and found over more than 20 takeoff and landing cycles, the noise level from its six large propellers never rose over 65 dBA.
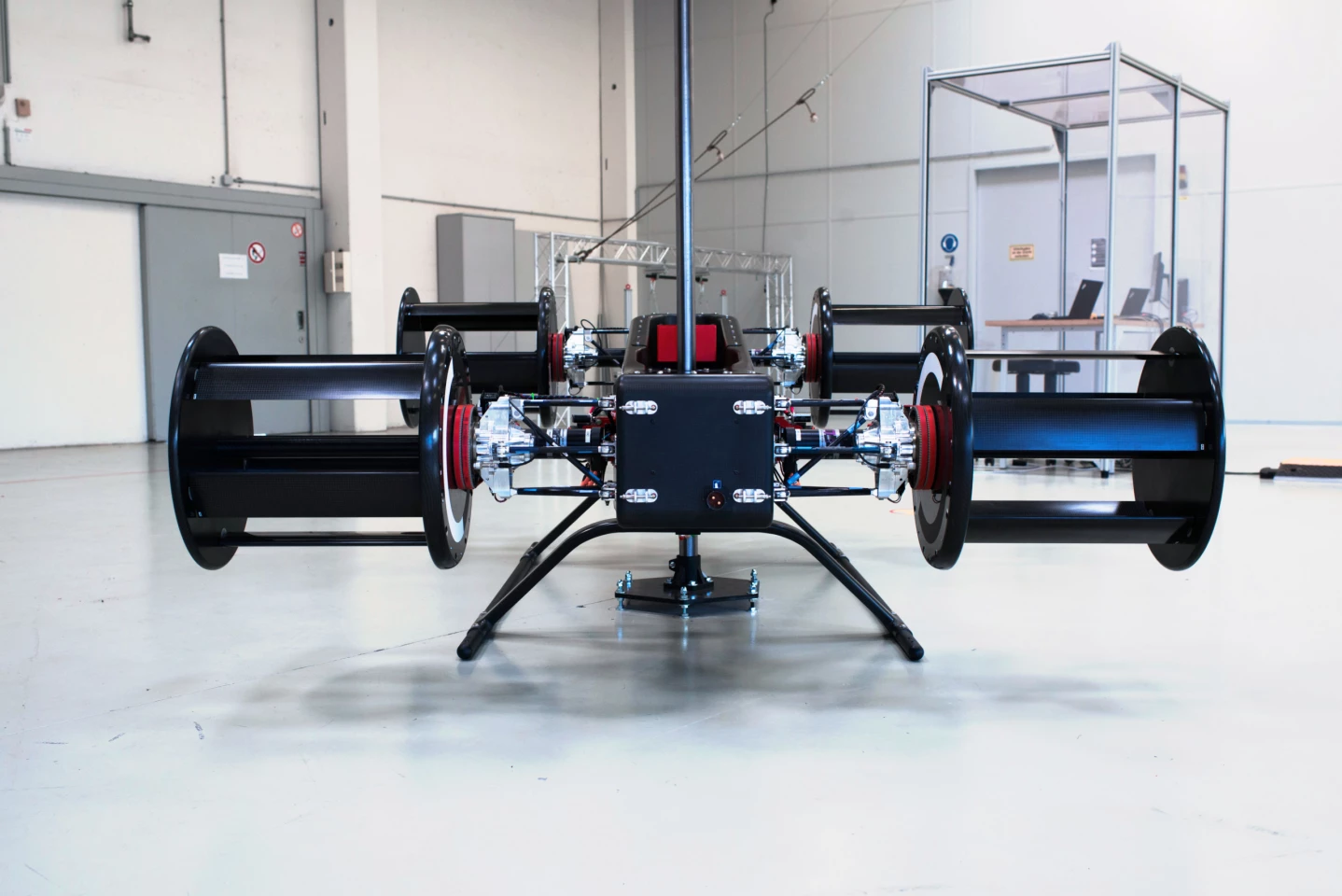
So while the CycloTech system is much earlier in development than the Joby aircraft, it seems reasonable to estimate that the CycloRotor propulsion barrels are likely to prove significantly noisier than regular ol' propellers once scaled up to full air taxi size – assuming that this is where this kind of tech will end up.
Check out the noise testing in the video below, which remarkably contains no audio from the tests. The first flight video above, however, lets you listen in a bit.
Source: CycloTech