If there's one major thing that's holding back an electric revolution in the aviation world, it's energy storage. But there are a ton of very clever people banging away at the problem of how to increase the energy density of batteries, and another growing faction working to make long-range, fast-fueling hydrogen-fuel-cell powertrains the standard for future flight.
Either way, it's going to happen in the coming decades, and one new company out of Minneapolis is turning its attention to the other critical element of the propulsion system. H3X Technologies is bursting out of the gate with an integrated electric motor design it says can deliver the same sustained power as some of the best motors on the market at a third or less of the total weight.
Weight, of course, is a big deal in aviation – and that goes double for electric aircraft. Every pound carried skyward represents a pound less payload you can carry, a reduction in the range you'll get from your battery or hydrogen tank, and ultimately a loss of money for the owner.
With small to medium electric planes beginning to go into commercial service, and the long-promised rise of the eVTOL air taxi segment forever just around the corner, H3X sees big opportunities ahead for a monster weight-saver like its HPDM-250 motor.
The first version will weigh 15 kg (33 lb) and make 200 kW of continuous power, peaking at up to 250 kW. That's 13.3 continuous kilowatts per kilogram, an extraordinary power density. For comparison, the Magnax axial flux motor we covered in 2018 boasts 15 kW/kg – but that's peak power; its continuous power density is more like 7.5 kW/kg.
And that in itself is absolutely exceptional. The motor used on the world's first commercial electric aircraft flight last year by Harbour Air was a Magnix Magni500 – yes, there are competing electric motor companies called Magnix and Magnax – and that thing's power density is more like 4.2 kW/kg.
What's more, neither of the above motors have an inverter built in, so there's some extra weight you've got to carry – 12 kg (33 lb) in the case of the Magnix drive system. The H3X design has its inverter integrated into its hexagonal prism body.
The motor's highest efficiency is at 20,000 rpm, which is way faster than you'd spin a propeller, so H3X can also fit it with an integrated planetary gearbox with a 4:1 reduction ratio, incurring a weight cost of just three additional kilos (6.6 lb). H3X founder and CEO Jason Sylvestre tells us the team could've designed the motor to spin slower and eliminated the gearbox, but the overall efficiency and power density would've suffered.
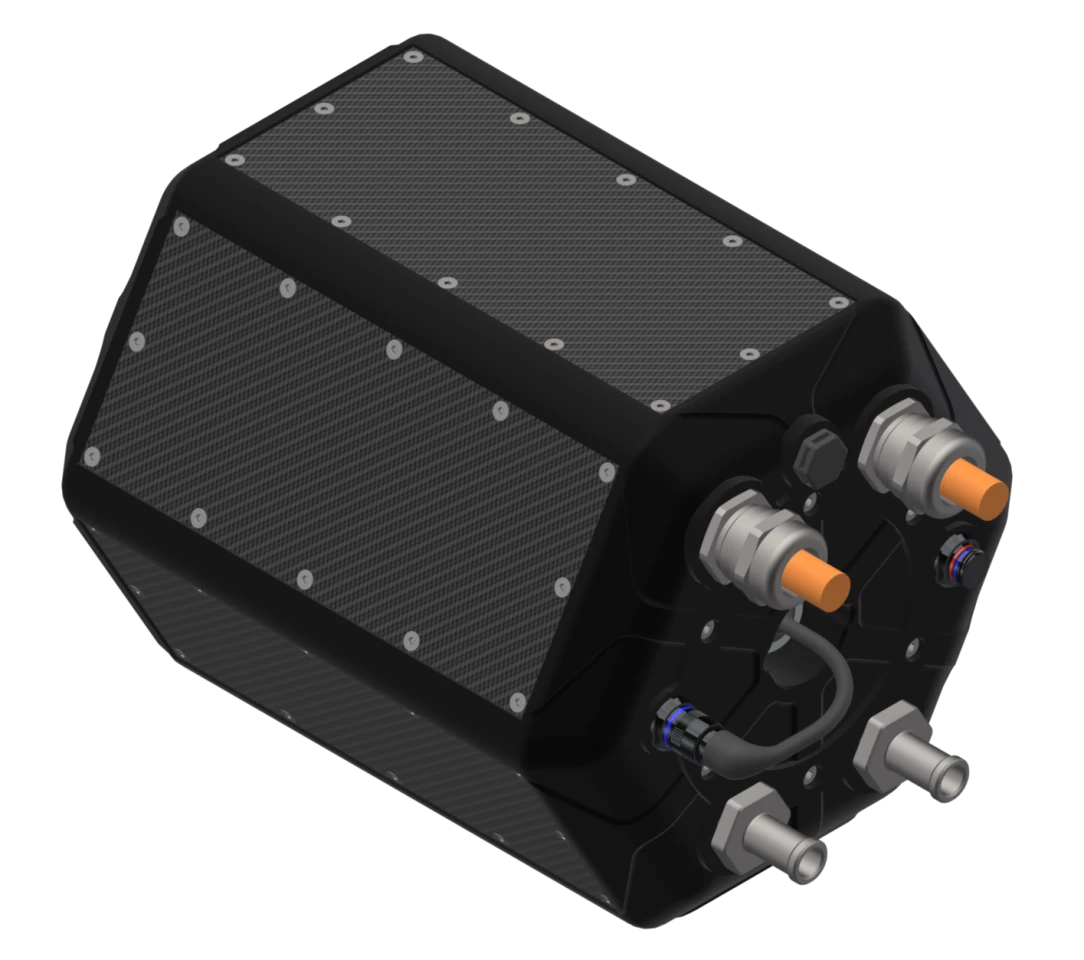
The H3X HPDM-250's peak combined efficiency between the motor, gearbox and inverter in this configuration – the one most likely to be used aboard an electric aircraft – is 92.9 percent. That's pretty much bang on the energy efficiency of the Magni500, just with vastly higher power output per unit of weight. Its continuous power density with the gearbox on board is 11.1 kW/kg, still well clear of the competition.
How has this Minneapolis startup team achieved such a remarkable leap in power density? Sylvestre tells us it's a combination of factors all adding up.
"The HPDM-250 has been designed to push the limits of performance while minimizing system mass," he says. "It is the product of patent pending innovation in multiple areas and features the highest level of integration on the market. This includes electromagnetics optimization, additive manufacturing, advanced materials, and high-frequency SiC power electronics.
"Two innovations are worth highlighting – We use a single, synergistic cooling jacket to simultaneously cool both the power electronics and motor. This integration reduces system mass and volume. Additive manufactured copper stator coils are used to increase copper fill factor and improve continuous current density capability. This is a new technology that has the potential to revolutionize the motor manufacturing industry as it offers faster development, better performance, and greater design flexibility."
Those 3D-printed copper stator coils not only allow H3X to fit more copper into a smaller space, they help a lot with cooling, allowing the HPDM-250 to run closer to its peak power without generating unmanageable amounts of heat. And Sylvestre says additive manufacturing means that this motor will be quick to prototype, iterate, scale to different sizes and power levels, and adjust to customer requirements.
Sylvestre tells us that even though the components are tightly packed in the motor design, its six-cover shell makes for easy access on the rare occasion you'll need to open it up.
Replacing a roughly 50-kg (110-lb) motor with an 18-kg (40-lb) one will deliver a tasty little weight dividend on a single-prop plane, but the benefits will scale up the more motors your design uses. Sylvestre sees this design as offering major payload, cost and range advantages to eVTOL air taxis that typically use upwards of six props. But H3X has its sights set on bigger targets.
"In the next five years, we're going to see those eVTOLs and small electric aircraft," says Sylvestre. "But by around 2030, we'll start to see electrification of large commercial aircraft. That's really what you want to go after. Aircraft around the size of a Boeing 737, those account for around 50 percent of all the greenhouse gas emissions in the aircraft sector. An aircraft that uses distributed propulsion with multiple 250-kW motors, maybe 16 or so, along each wing. You can imagine the weight of those will add up, and that's where a motor like ours could make a huge difference."
As always, extraordinary claims require extraordinary evidence, so we look forward to hearing how the prototype performs.
"We're in the process of prototyping it right now," says Sylvestre. "We should be testing it by Q2 of next year. In terms of the business, we're looking to get letters of intent from potential customers, and partner with early investors to expand H3X. We've been operating very much in stealth mode."
One to keep an eye on.
Source: H3X