In the simplest terms, nearly every modern car on the planet uses disk brakes: a rotor attached to a hub with a caliper with brake pads fixed to the control arm at each wheel. The driver presses the brake pedal and hydraulic fluid is pushed down the brake lines into the caliper, expanding the pistons and pushing the brake pads against the rotor, slowing down the rotation of the rotor connected to the hub, thus slowing down the wheel.
There are other systems, like drum brakes, air brakes, band brakes, the Flintstones method, et cetera, that have also been around since the dawn of the automotive industry. The concept almost always remains the same: using friction to slow down. And so it doesn't go unsaid, yes, there are compression brake systems as well, but that's entirely different.
Mercedes-Benz has put a new spin on an age-old concept with what it calls "in-drive brakes" for electric vehicles. The system being developed at the company's research and development department in Sindelfingen, Germany, integrates the brakes right into the drivetrain, in an arrangement that works very much like a transmission brake. It resembles clutch plates – but with a unique twist.
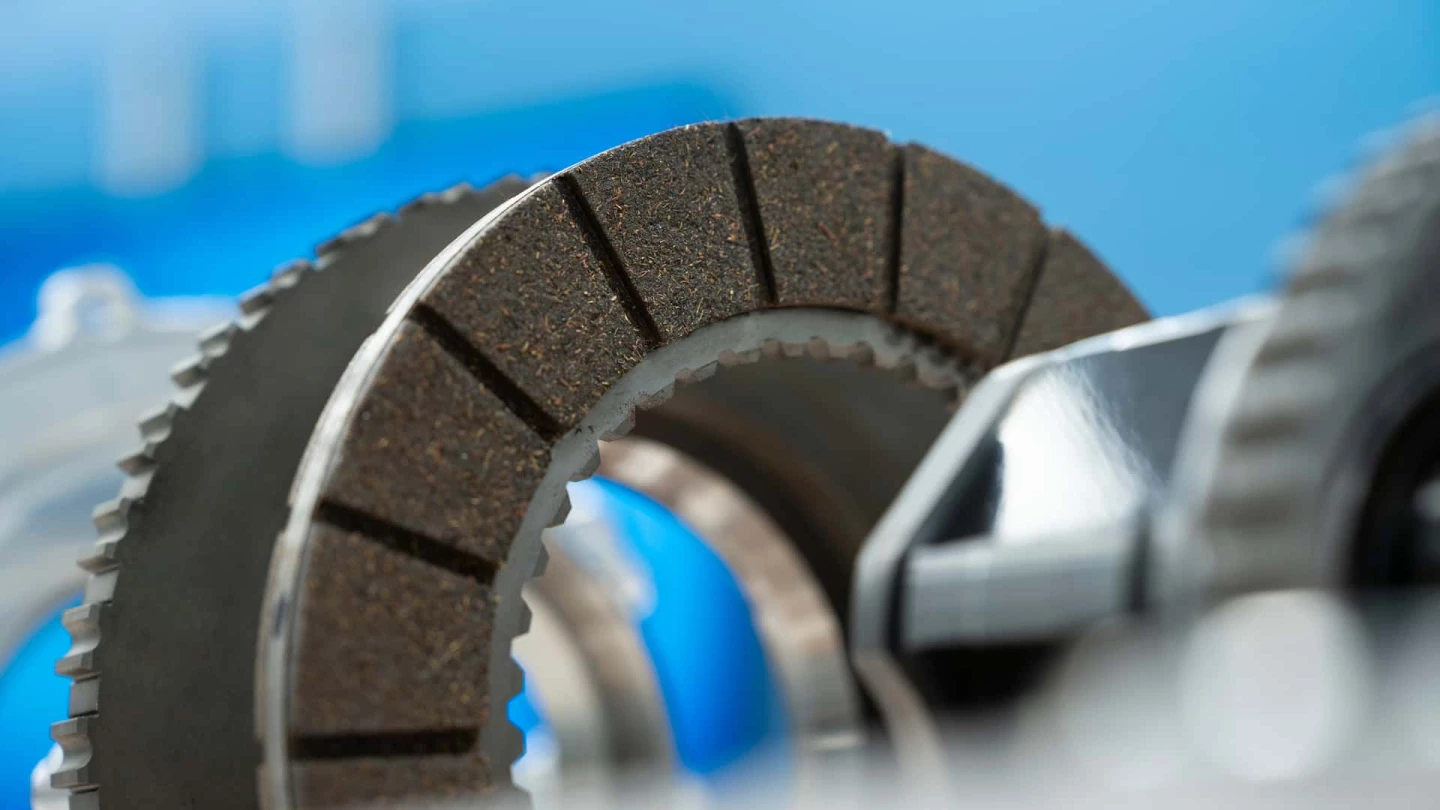
There are no calipers, instead a circular brake pad connected directly to the output shaft of the electric motor is pressed against a stationary water-cooled ring, all of which is in an enclosed system.
According to Mercedes, the in-drive brake system shouldn't require servicing for the life of the vehicle, potentially saving the owner thousands of dollars in brake repairs and replacements. Even the brake dust is collected in a small inner compartment that won't require emptying.
Brake dust is a major contributor to pollution, particularly in urban areas with lots of stop-and-go traffic. And if you've ever driven down a long, steep grade like the Grapevine, just north of Los Angeles, California, you're no stranger to the smell of brake dust – and the discomfort in your nasal passages. EV motors inherently act as a brake when the accelerator is released, as EV motors have the ability to regenerate electricity back into the batteries, slowing the vehicle down in the process. An actual brake system is still needed, however.
Though the in-drive brake is still undergoing testing, Mercedes reckons that brake fade will be a non-issue as the system is water-cooled. Given the in-drive brake system relocates all the necessary "slow down" bits away from the wheels, unsprung weight (weight that isn't carried by the chassis, and instead spins or moves with the wheels, creating gyroscopic forces) is significantly reduced, making the vehicle both handle better and improve the ride. Wheels could also be made more aerodynamically efficient without the constraints of rotors and calipers.
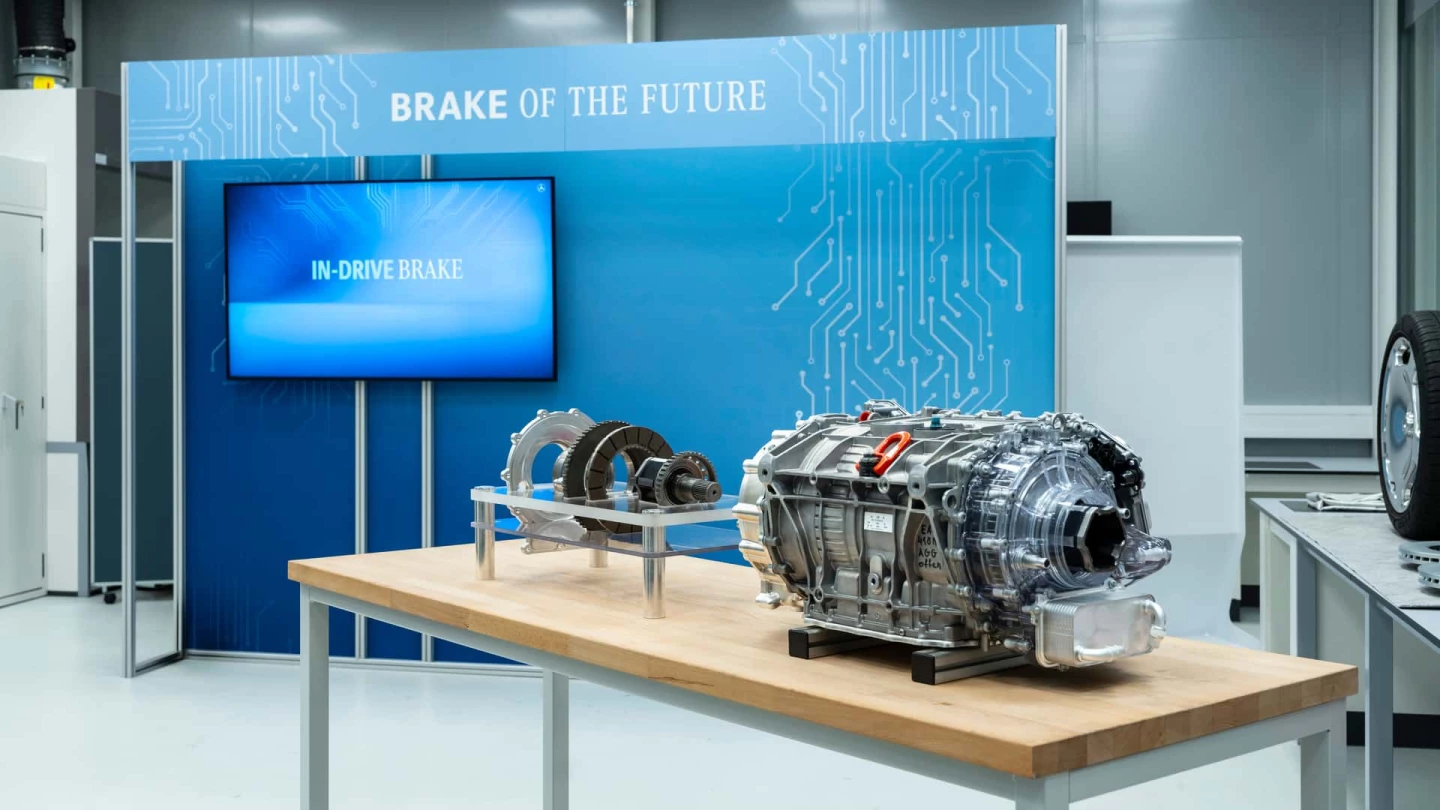
The biggest upside to in-drive brakes? No more looking at rusty rotors on your otherwise beautifully pristine US$180,000 Mercedes-Maybach EQS 680 SUV. Tongue-in-cheek, of course. A brake system that doesn't require repairs will save owners downtime and money. Consolidating components also saves the manufacturers money and necessary materials, making a smaller impact on the planet.
And with Euro 7 emissions standards starting in 2026, the dust-sealing design will be ahead of the curve.
While Mercedes focuses on reimagining traditional brake systems for its electric cars, other companies are rethinking the entire architecture of electric vehicles. REE has taken an interesting approach by relocating everything "under the hood" into the wheel wells. Motors, drivetrain, steering, suspension, and brakes are all located in the wheel wells, creating a modular platform – one that very much resembles a skateboard – on which anything can be built on top of, from delivery trucks to sports cars to camper vans.
Whether Mercedes' in-drive brakes become a new standard or ends up as a premium upgrade for affluent EV buyers, only time will tell.
Source: Inside EVs