Iron and steel form the structural backbone of modern life, but they're responsible for somewhere around 8% of global carbon emissions, making them the single biggest source of industrial greenhouse gases.
The path to a 100% clean future is clear enough; ditch the blast furnaces and baked-coal coke reductants, and replace them with electric arc furnaces running on clean energy, and green hydrogen reductants. Boom: green steel with water as the only by-product.
Here's the problem: humanity is now producing somewhere around two billion tons of steel a year globally, and such a vanishingly tiny percentage of that is clean that it was big news in 2021 when a block of green steel actually got delivered to a customer. This is a colossal industry with an enormous amount of assets, facilities and machinery already fully functional, and built to last.
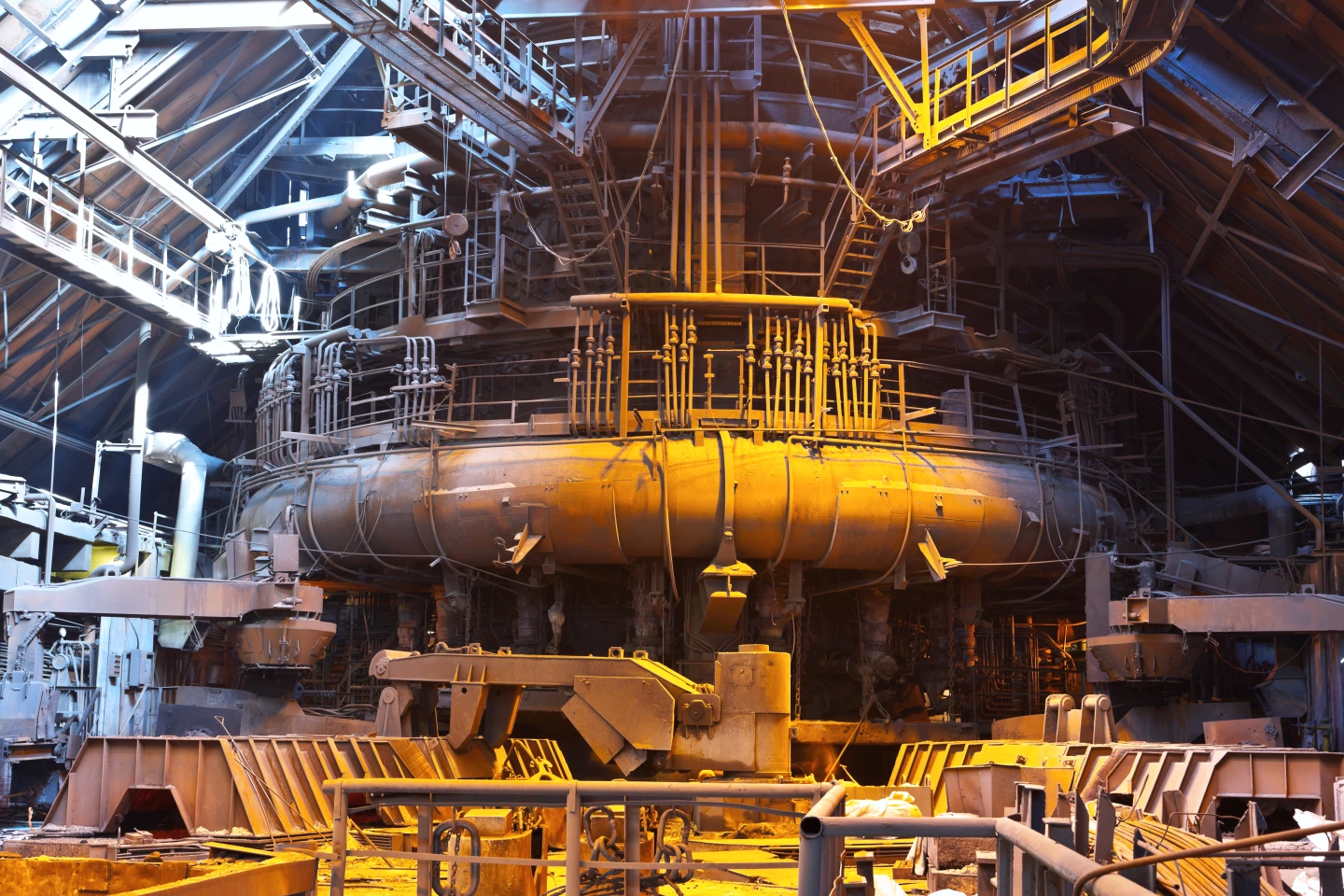
Switching to an electric arc furnace is no trivial exercise; it costs between US$1.1 to 1.7 billion according to the world's second-largest steelmaker, not including costs related to your stranded blast furnace assets. Green hydrogen isn't available yet at the necessary scale, and thus the production cost of green steel is a brutal 60% higher than the dirty stuff.
So blast-furnace/basic oxygen furnace (BF-BOF) steel is going to be around for decades to come, and that's why this new retrofit system from the University of Birmingham may be one of the most important green-tech advances of the year, despite not being fully green.
In a nutshell, it replaces about 90% of the coke used in the blast furnace with direct carbon monoxide injection. The carbon monoxide comes from a system that captures and recycles the furnace's own exhaust "top gas," separating out carbon monoxide, carbon dioxide, hydrogen and nitrogen gases at high temperatures. These gases are then sent through a twin-reactor redox system that keeps the carbon inside a closed loop.
The carbon dioxide is cycled through a thermochemical oxidation process in one reactor chamber, using a double perovskite material (Ba2Ca0.66Nb0.34FeO6, or BCNF1 for brevity), which converts it into carbon monoxide at around 800 °C (1,472 °F) at a rate around 10.1% each pass, grabbing oxygen atoms out of carbon dioxide molecules and using them to fill up the cubic crystal structure of the BCNF1.
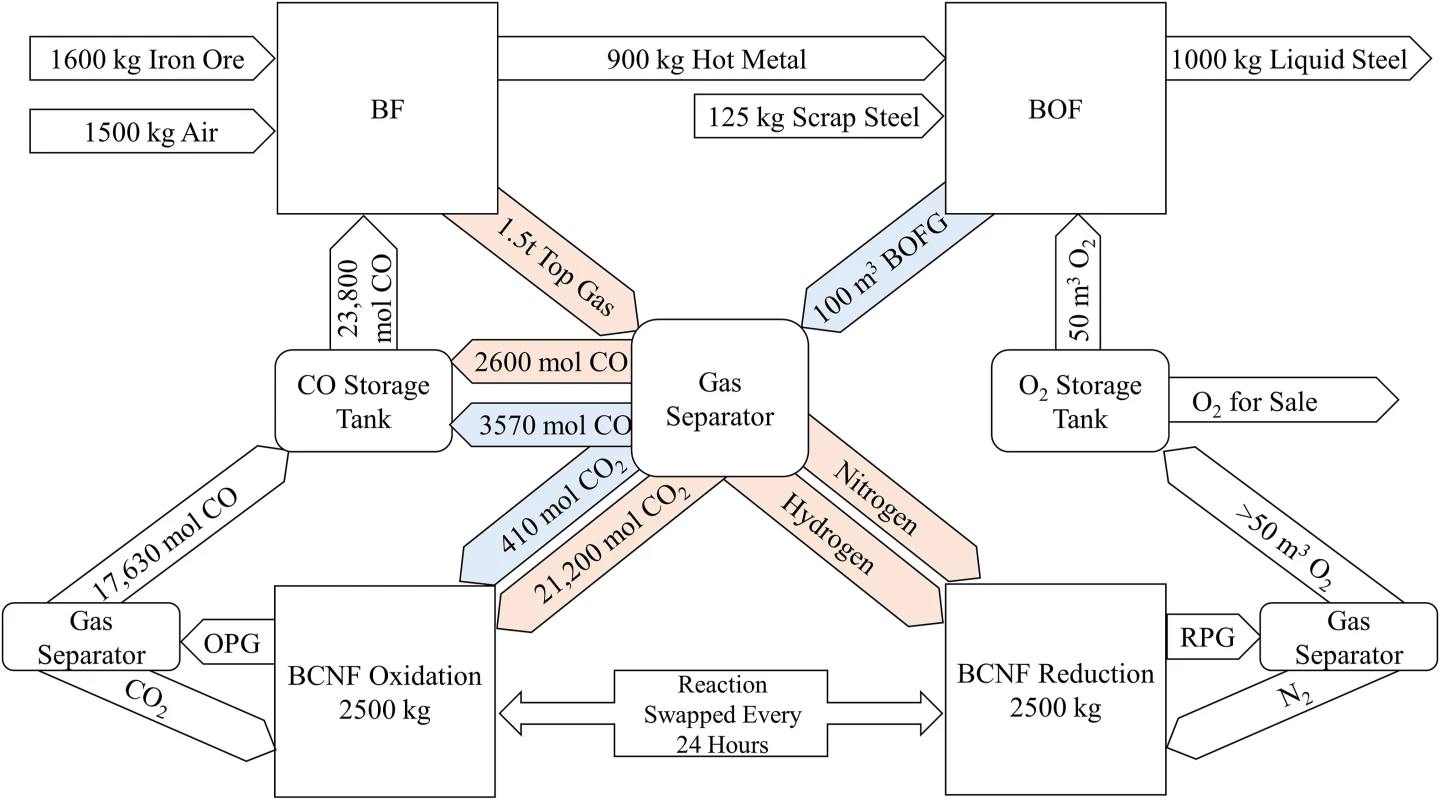
Meanwhile, the nitrogen and the small amount of hydrogen from the top gas go into a second BCNF1 reactor for a thermochemical reduction process at 700 °C (1,292 °F), which releases pure oxygen from the BCNF1 structure. That oxygen feeds the basic oxygen furnace that converts hot metal from the blast furnace into liquid steel, with extra oxygen left over that could be sold. The exhaust gas from the basic oxygen furnace goes straight back into the gas separator.
Every 24 hours or so, the BCNF1 structures in the reduction and oxidation chambers will start to drop their reaction rates, having released or stored too many oxygen atoms, respectively. The steel plant operator then simply switches the gas flows going in and out of these two reactors, using the perovskite in an endless thermochemical redox cycle to keep these reactions moving efficiently.
This system recycles both the carbon and the heat very effectively. But by removing most of the coke, and repurposing exhaust gases that are normally burned, it takes away a lot of the energy typically used to run a steel plant. This system requires somewhere around 306 kWh of extra electrical energy to be brought in per tonne of liquid steel produced.
"If the electricity needed to power the electric heaters and gas separators is procured from renewable sources, this would not add to the emissions of the TC-BF-BOF," reads the Birmingham team's study, just published in the Journal of Cleaner Production. "The cost of this electricity, plus the electricity needed to power the gas separators, is more than accounted for in the savings from replacing the coke in the system."
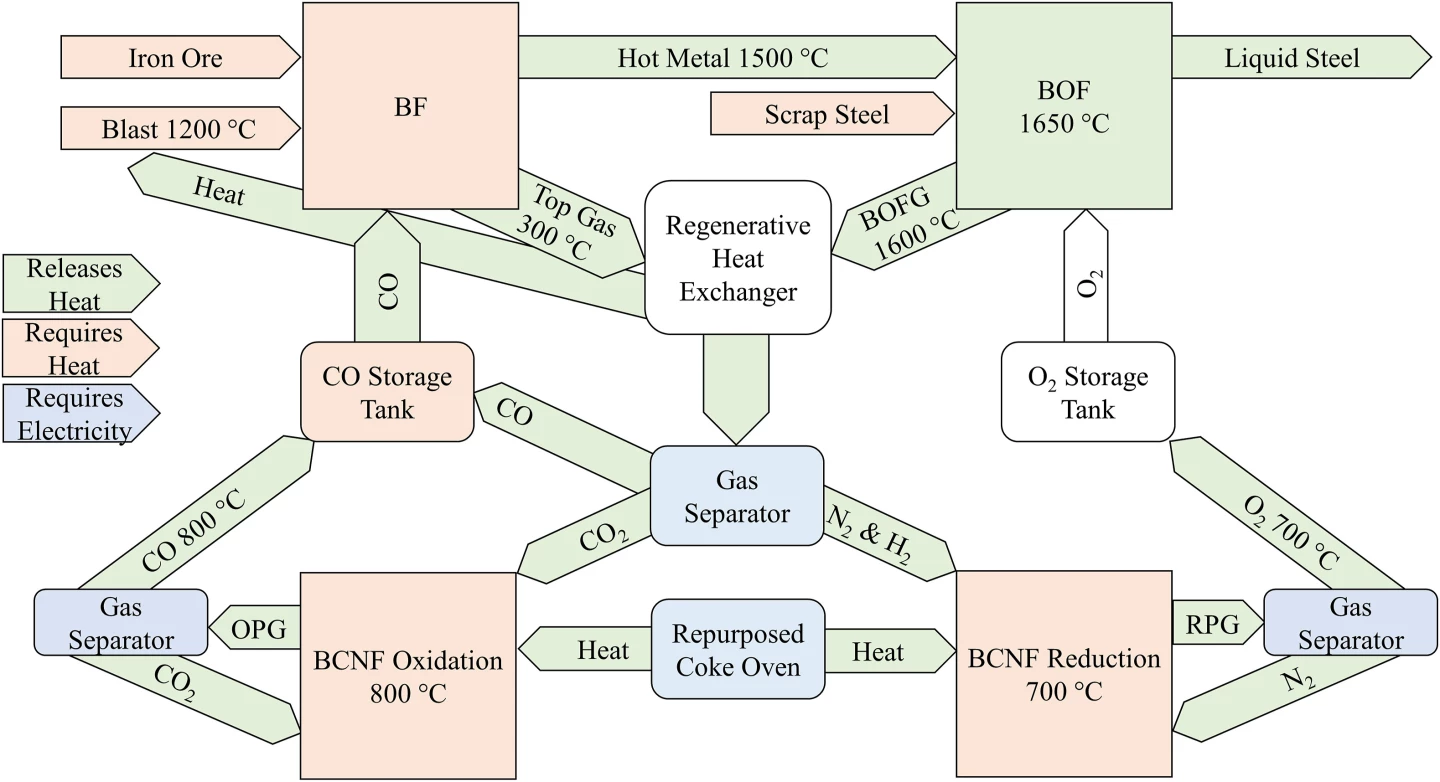
Indeed, the Birmingham team says that retrofitting this thermochemical redox system to existing BF-BOF steel plants should make it notably cheaper to produce steel. Taking the British Steel (BS) facility at Scunthorpe as an example, the team estimates BS would need 10 of these switchable redox reactors, each around 15 m (49 ft) tall and 9.5 m (31 ft) in diameter, at a cost around UK£359 million (US$445 million) all up.
But the company would save UK£187 million (US$232 million) a year on its coke budget – a figure that'd impress late 1990s Robert Downey Jr – and generate about UK£13 million (US$16 million) a year in excess sales of pure oxygen. The report estimates that after just five years, BS would be somewhere around UK£640 million (US$740 million) better off on the balance sheet. The BCNF1 material would need replacing every five to 10 years at a cost around UK£200 million (US$248 million).
If these figures hold up, it'd be just about a no-brainer for any steelmaker with a BF-BOF facility, on economic grounds alone.
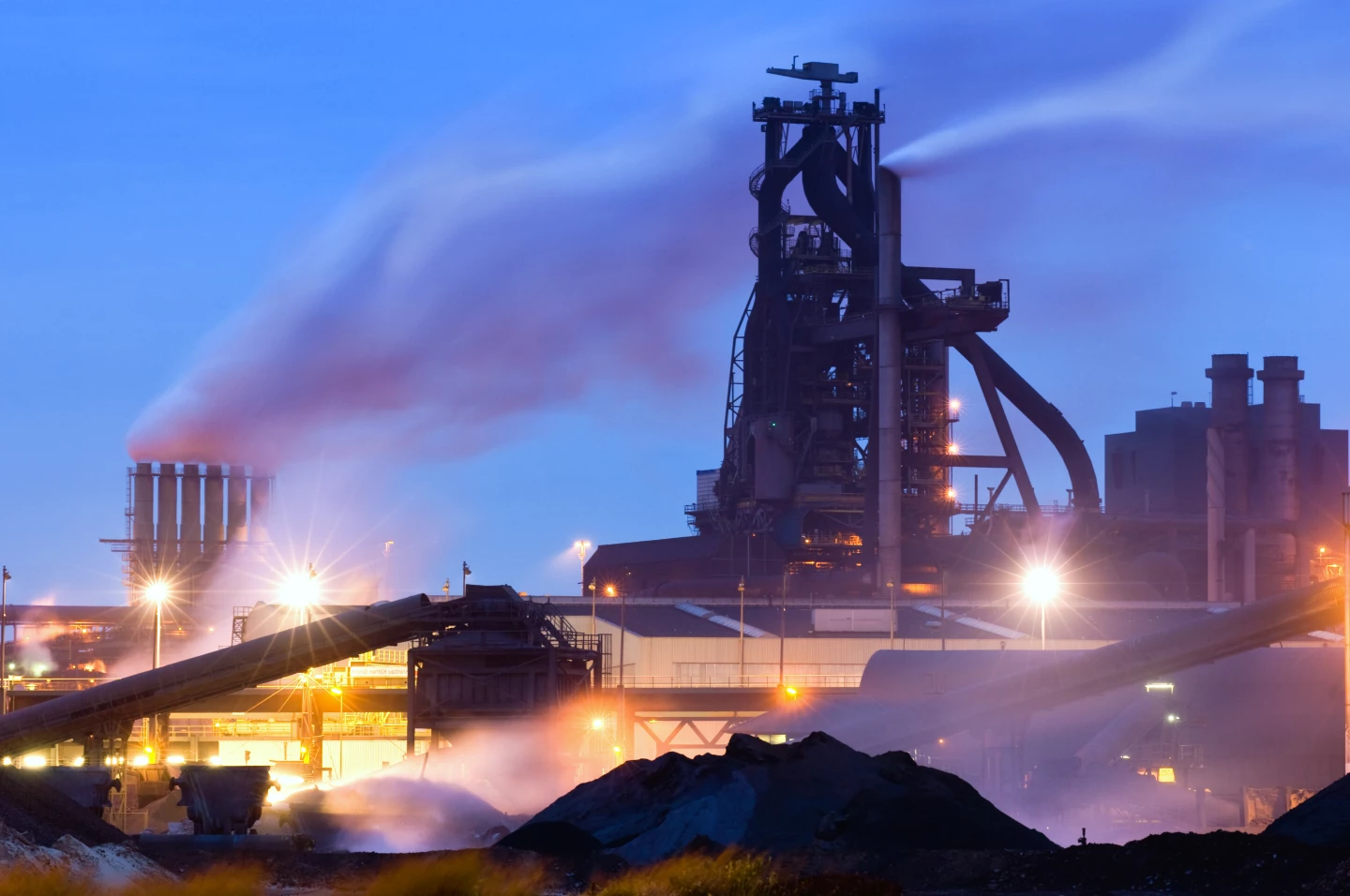
But the broader point is the planet. And emissions would be absolutely slashed, by at least 90%, say the researchers. There's only one other BF-BOF steelmaking facility in the UK, Tata's facility at Port Talbot. That and the BF facility are currently combining to belch out about 11.4 million tonnes of carbon dioxide a year, or about 3.1% of the UK's entire emissions total. This system promises to bring that down to around 680,000 tonnes combined, a massive 94% reduction.
That means the UK could conceivably cut its entire national emissions total by a whopping 2.9% with an upfront investment of about UK£720 million (US$893 million) and perovskite replacement costs around UK£400 million (US$496 million) every five to 10 years – investments which would pay substantial dividends within a few years.
And that's just the UK; somewhere around 70% of the world's steel is currently produced using BF-BOF plants. The potential scope of the decarbonization opportunity here is absolutely enormous.
But – and there's always a but – this is currently nothing more than a research paper, the first-principles calculations around the idea. The team is yet to prototype such a facility, and there are some unknowns it wants to look into before moving forward.
Firstly, coke is used as a structural support in blast furnaces, and the team says research is needed into how badly heat and mass flows would be affected if it was taken away. Secondly, the team says more research should focus on reducing the energy requirements of nitrogen/carbon monoxide separation. And thirdly, experiments will need to be done over a period of years before the replacement rate of the perovskite materials can be understood.
Still, given the colossal emissions-busting potential here, and the impressive financial projections for steelmakers, you'd have to say the team shouldn't find it hard to get funding to push this idea forward. It's rare to find decarbonization tech that appears like it'll work just as well for business owners as it will for the planet.
“Current proposals for decarbonising the steel sector rely on phasing out existing plants and introducing electric arc furnaces powered by renewable electricity," says study co-author Professor Yulong Ding in a press release. "However, an electric arc furnace plant can cost over £1 billion to build, which makes this switch economically unfeasible in the time remaining to meet the Paris Climate Agreement. The system we are proposing can be retrofitted to existing plants, which reduces the risk of stranded assets, and both the reduction in CO2, and the cost savings, are seen immediately.”
Check out a short video explanation below.
The research is open access at the Journal of Cleaner Production.
Source: University of Birmingham