Recycling massive wind turbine blades can be difficult because they're built from sturdy materials to weather the elements for decades. Researchers at Washington State University have devised a way to leverage those properties, and use discarded blades to create strong and durable plastics – without resorting to the use of harsh chemicals.
The challenge lies in breaking down the cured lightweight material many older blades from the 1990s are made from: glass fiber-reinforced polymer (GFRP). But in their work, published in the journal Resource, Conservation, and Recycling this month, the team found another way. , explained:
"For this work, we didn’t need to fully break down all the bonds and push the reaction to completion," explained Baoming Zhao, who co-authored the paper. "As long as we can break the cross-linked network into smaller pieces, and they are melt processable, we can compound that with nylon and get a new composite."
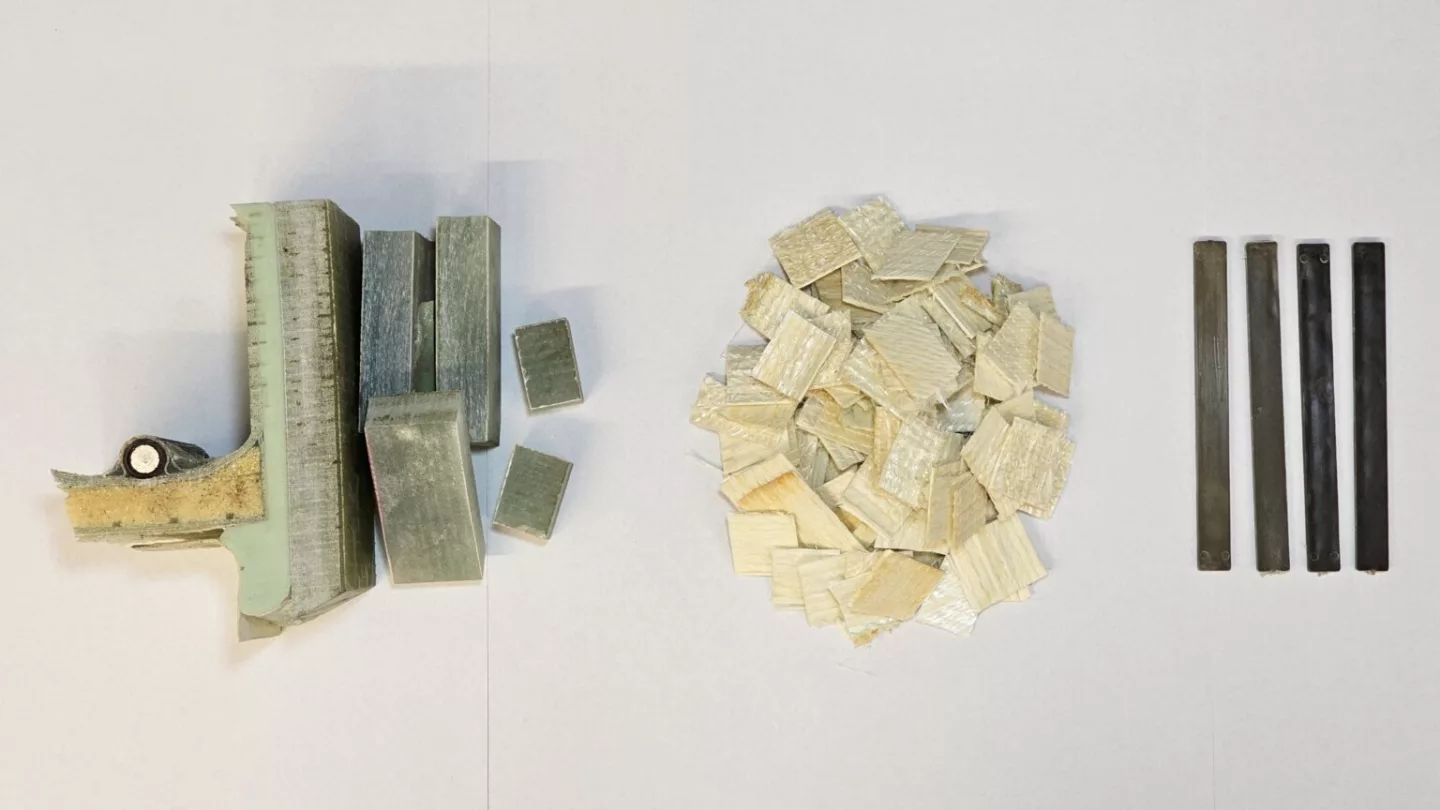
The team's method starts with cutting discarded turbine blades into two-inch blocks, and then shredding those into chips. These chips are soaked in a mild solution of zinc acetate (a low-toxicity organic salt) in pressurized, superheated water for two hours.
The process allows for recovering intact glass fibers and resins, which can then be combined with melted thermoplastics (a material commonly used in milk bottles) and nylon plastic to produce higher grade composite materials. The composite recycled nylon plastic came out more than three times as strong, and eight times as stiff.
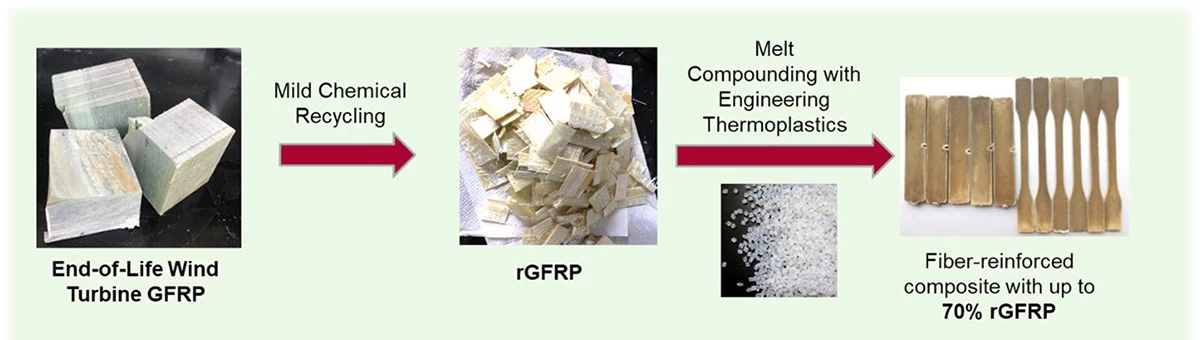
The researchers' method has a couple more benefits. For one, the zinc acetate catalyst can simply be filtered and recovered for reuse. Secondly, this process can be applied to other common plastics like polypropylene, which is used in products like food containers, stationery, and toys.
That could make used turbine blades valuable to plastic recycling plants, while utilizing a relatively environmentally friendly process. The researchers' next step is to reduce the pressurization requirements in their method and make it even easier to apply at scale, and explore the development of recyclable materials that can be used to make new turbine blades.
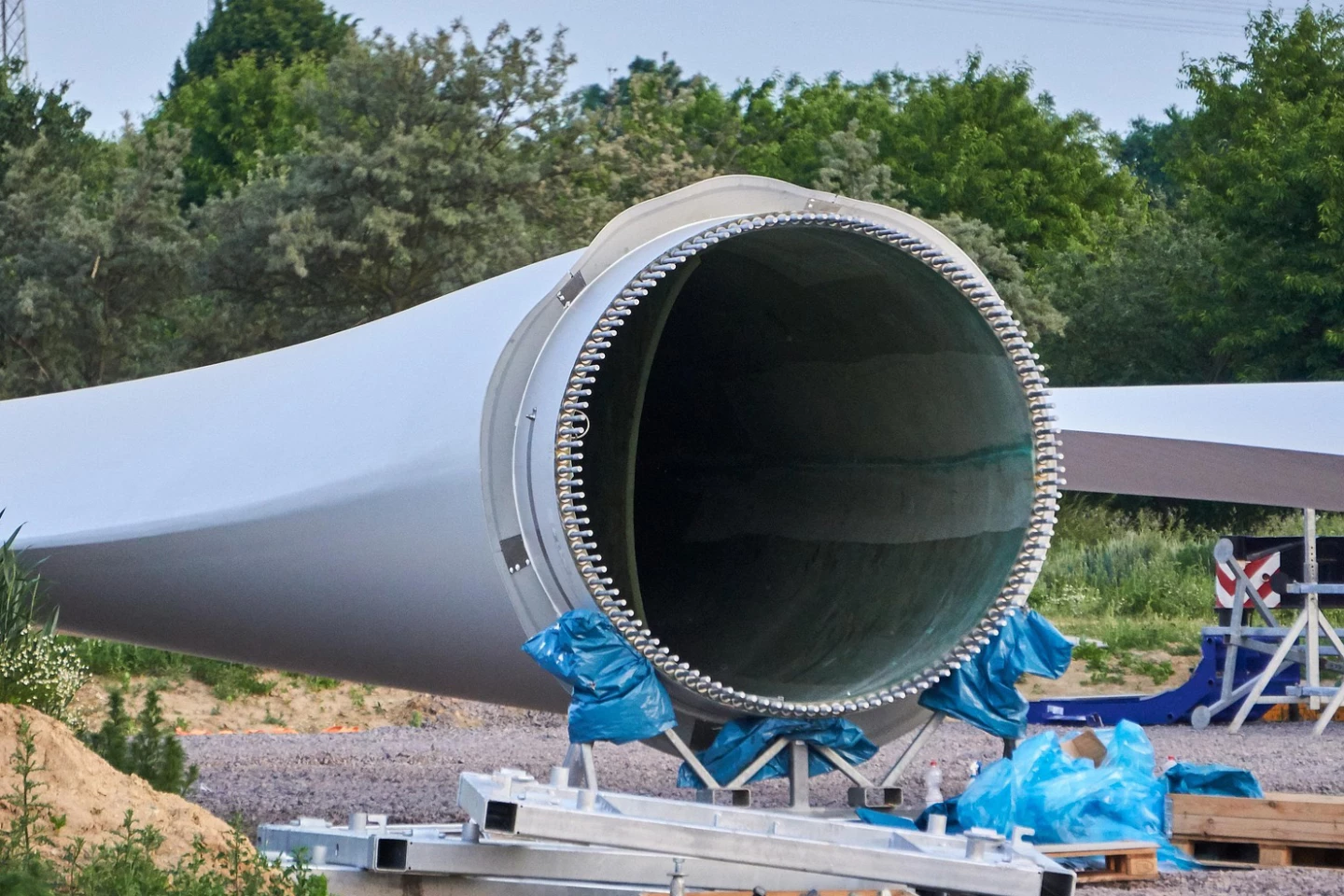
If you're interested in this sort of story, you might want to check out other clever ideas for recycling wind turbine blades we've covered recently, including turning them into surfboards, roads, and floating docks for saunas on the water. There are also recyclable blades currently doing the rounds (pun intended) from Siemens Gamesa and GE, and a bio-based resin could feature in future blades to help them break down faster once they're discarded.
Source: Washington State University