It's easy to look back at the history of exploration and aviation and feel like there's no mountains left to climb, that the age of the great pioneers is behind us and we're doomed to a future of LCD tanning and monitor hypnosis. But don't try telling that to Pascal Chretien. On August 12, this electrical/aerospace engineer and helicopter pilot took to the air in the world's first untethered, fully electric manned helicopter flight in a prototype machine that he designed and built almost entirely by himself within a 12 month development period. In his 2 minute, 10 second test flight, Chretien beat aviation giant Sikorsky into the record books - but it was not without significant risk. As the man himself puts it: "in case of crash I stand good chances to end up in kebab form."
With battery technology advancing steadily and electric vehicles popping up across all sorts of transport modes, electric helicopters have been one of the last dominoes to fall. That's because the dynamics of helicopter flight tend to consume a lot of energy - and in a way that doesn't fit in well with the way batteries perform.
Electric airplanes, for example, require a lot of power in the takeoff phase, but can cruise and land on fairly meager amounts of energy. But helicopters require strong power delivery throughout the takeoff, hovering and landing phases - so you have to make sure there's plenty of power in the tank to take you down softly.
So when French company Solution F contacted Pascal Chretien and asked him to build the world's first manned electric helicopter, he knew he had to come up with a pretty unique design - an ultra-light, super simple helicopter that could get a decent flight time out of its available battery power.
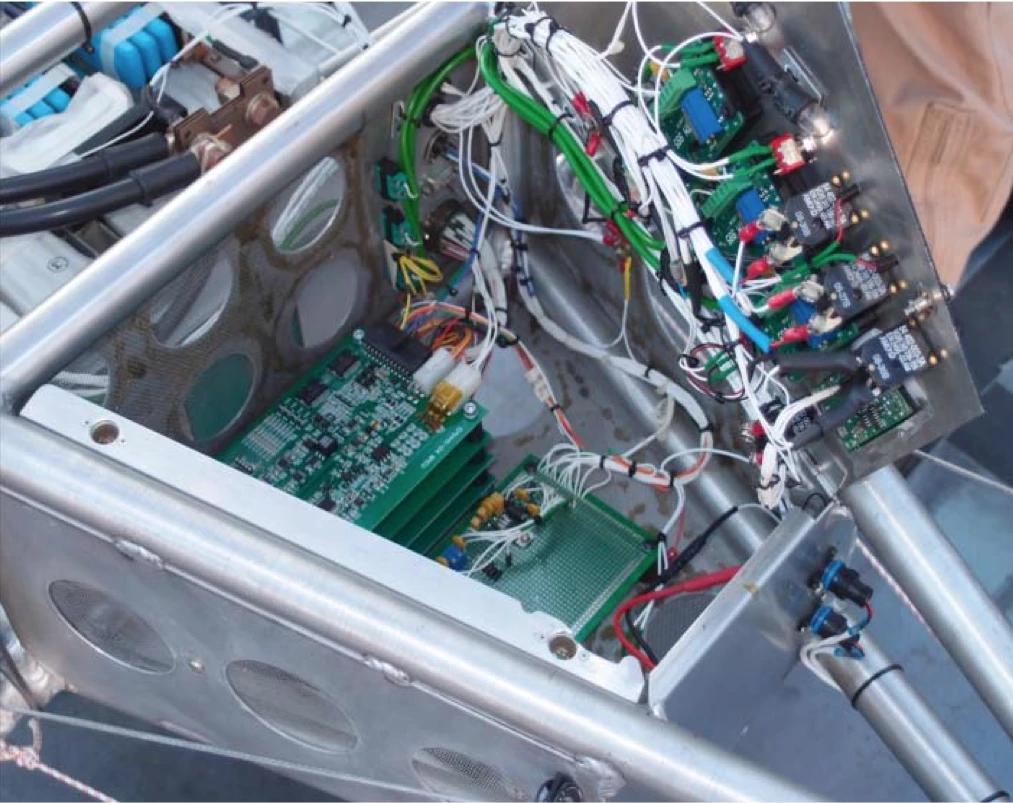
Designing a prototype electric helicopter
For the basics of conventional helicopter flight and definitions of a couple of the terms below, check out our "How to Fly a Helicopter" video - it really is fascinating how these contraptions work in a conventional sense.A conventional system wouldn't work here though - a tail rotor, for example, drains somewhere between 8% and 10% of total hover power. So Chretien modeled and built a coaxial design with two counter-rotating rotors on top - a torque-balanced design that can fly without the need for a tail rotor to stop the aircraft rotating out of control - instead, it just needs a simple, lightweight tail fin.
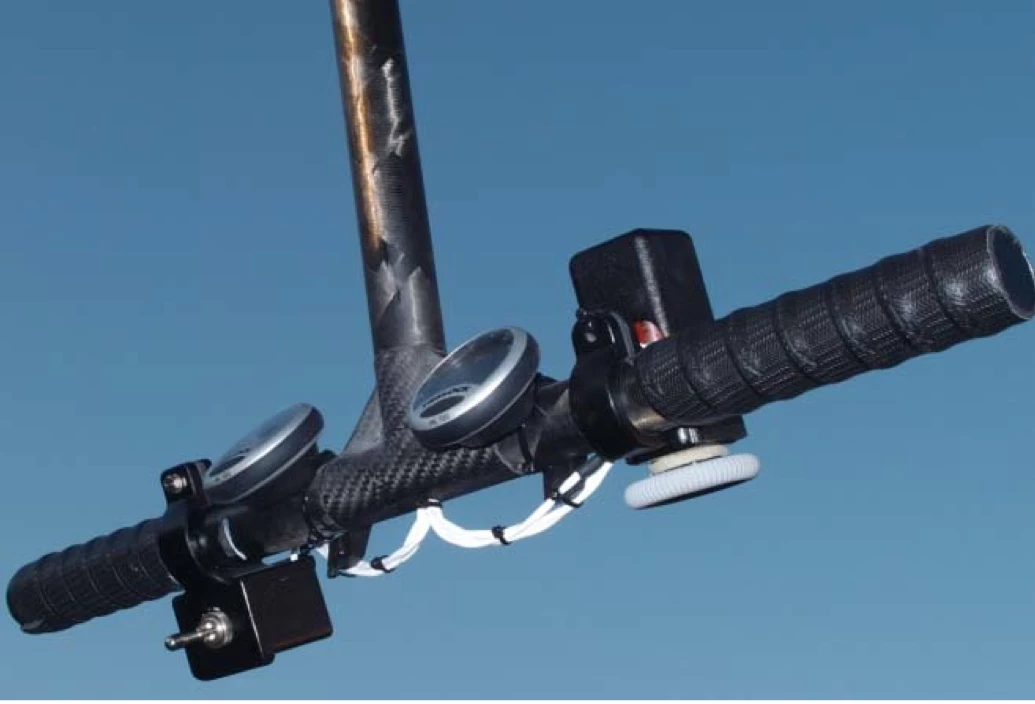
In place of the typical cyclic control, which uses an ingenious variable blade tilting system to control which way the helicopter tilts and advances, Chretien chose an extremely simple weight-shifting system - a big set of handlebars (incorporating the collective control) that literally tilt the main weight of the aircraft underneath the rotors - as his steering assembly. But this increased Chretien's risk factor by a significant margin - because it meant the controls would be reversed compared to a normal helicopter.
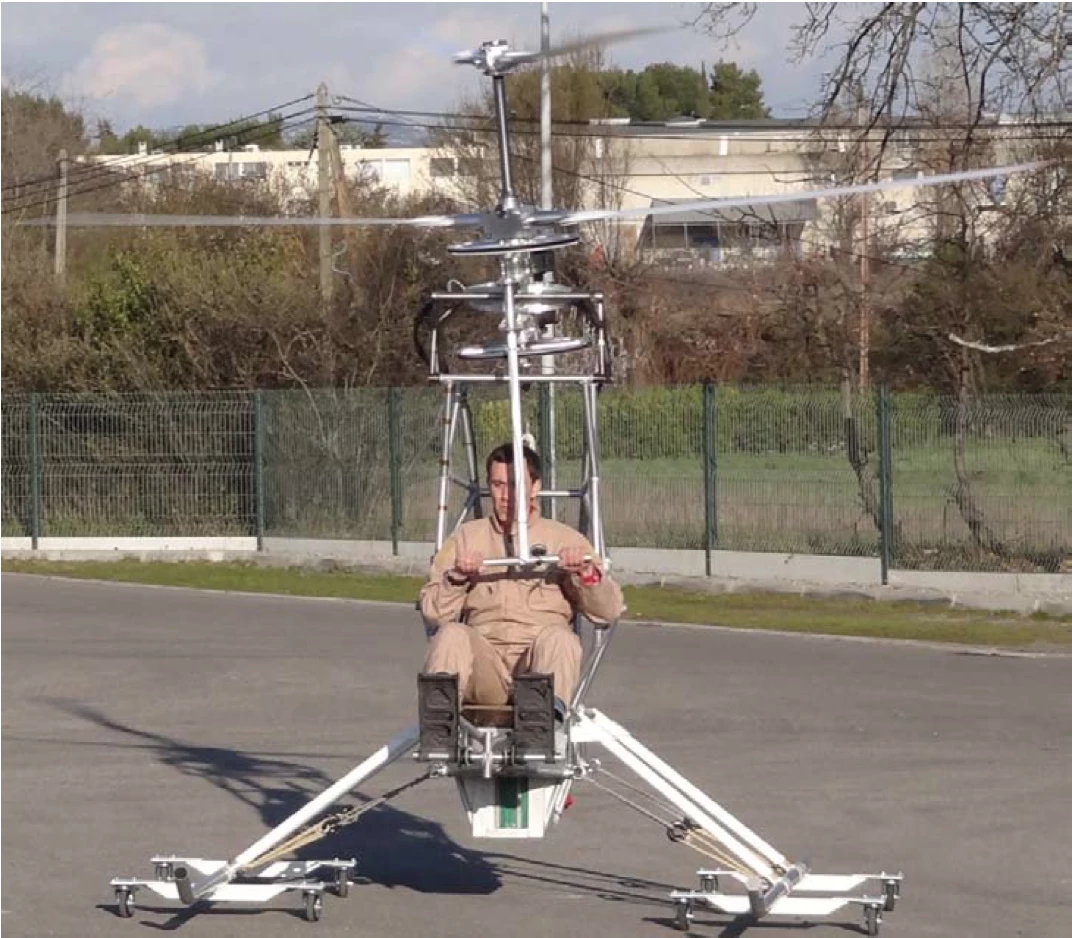
As Chretien puts it: "Weight savings were substantial - 4 to 5kg compared to a conventional arrangement... But habits being second nature, after 15 years of flying conventional machines the risks of crash were quite high." So during the development phase of the aircraft, Chretien built himself a pendular weight shift training machine to get himself used to the system and make sure he didn't react the wrong way when he first took to the air.
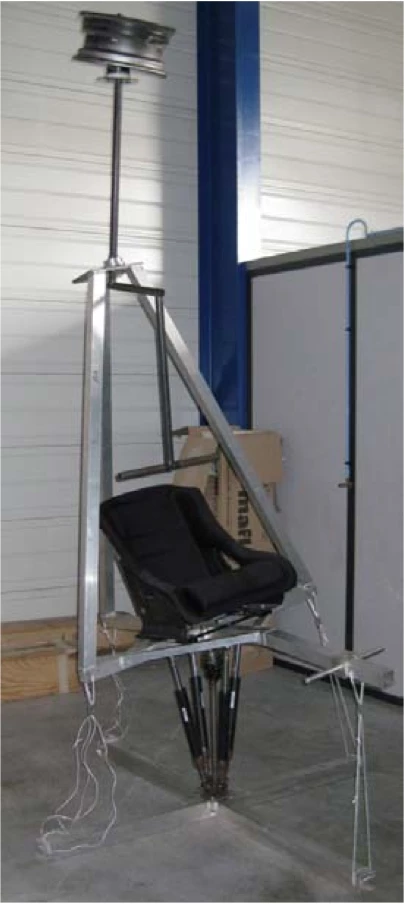
Yaw control was achieved with a combination of electric controllers (presumably varying the speeds of the two rotors) and a mechanical linkage that tilts the tail fin against the downwash from the main rotors - and the yaw controls are operated through pedals as in a conventional helicopter design.
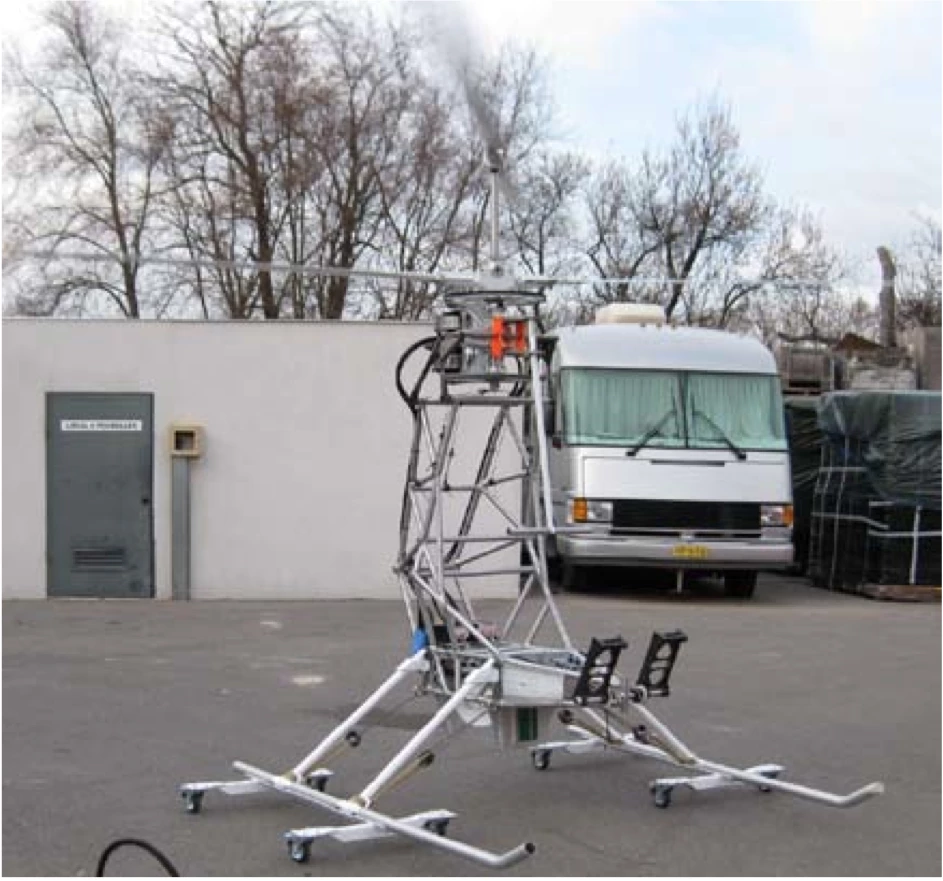
The frame of the helicopter was built from welded 7020 aluminum tubing - composite materials would have been lighter, but time was of the essence, and crash-worthy aluminum frames can be built in very short timeframes - plus, this decision helped keep the cost of the vehicle down.
The Powerplant
Chretien had been given a target of 10 to 12 minutes' flight time by Solution F, so the most critical part of the aircraft design was working out how to store enough power for this kind of flight, as well as how to use that power most efficiently. Early on, he sought the help of Lithium Balance , who supplied the battery management system and consulted on power storage issues.Chretien chose brushed DC motors for the rotor shafts, even though the required power output was "just on the edge of what can be achieved with brushed motors" - because brushed motors are exceptionally efficient, and their simple controller units are significantly lighter than those of more powerful, less efficient brushless motors.
With these in place, Chretien was able to achieve an 87.5% energy efficiency between the battery terminals and the rotor shafts.
The rechargeable battery cells are Lithium ion polymer pouch cells, with an energy density of 160 Watt-hours per kg. Although reasonably lightweight, these cells presented probably the biggest danger to Chretien in the test flight phase. As he puts it: "The infamous thermal instability of lithium/cobalt chemistry does not leave room for error... It is important to take it slowly, if I don't want to wreck tens of thousands of Euros worth of hardware; but also, in case of crash I stand good chances to end up in kebab form, as LiPo batteries are notoriously infamous for bursting to flames once distorted. The chemical reaction is violently exothermic. This machine looks like a toy, and flies like a toy, but there is a raging tiger under the seat, waiting to bite at the first mistake."
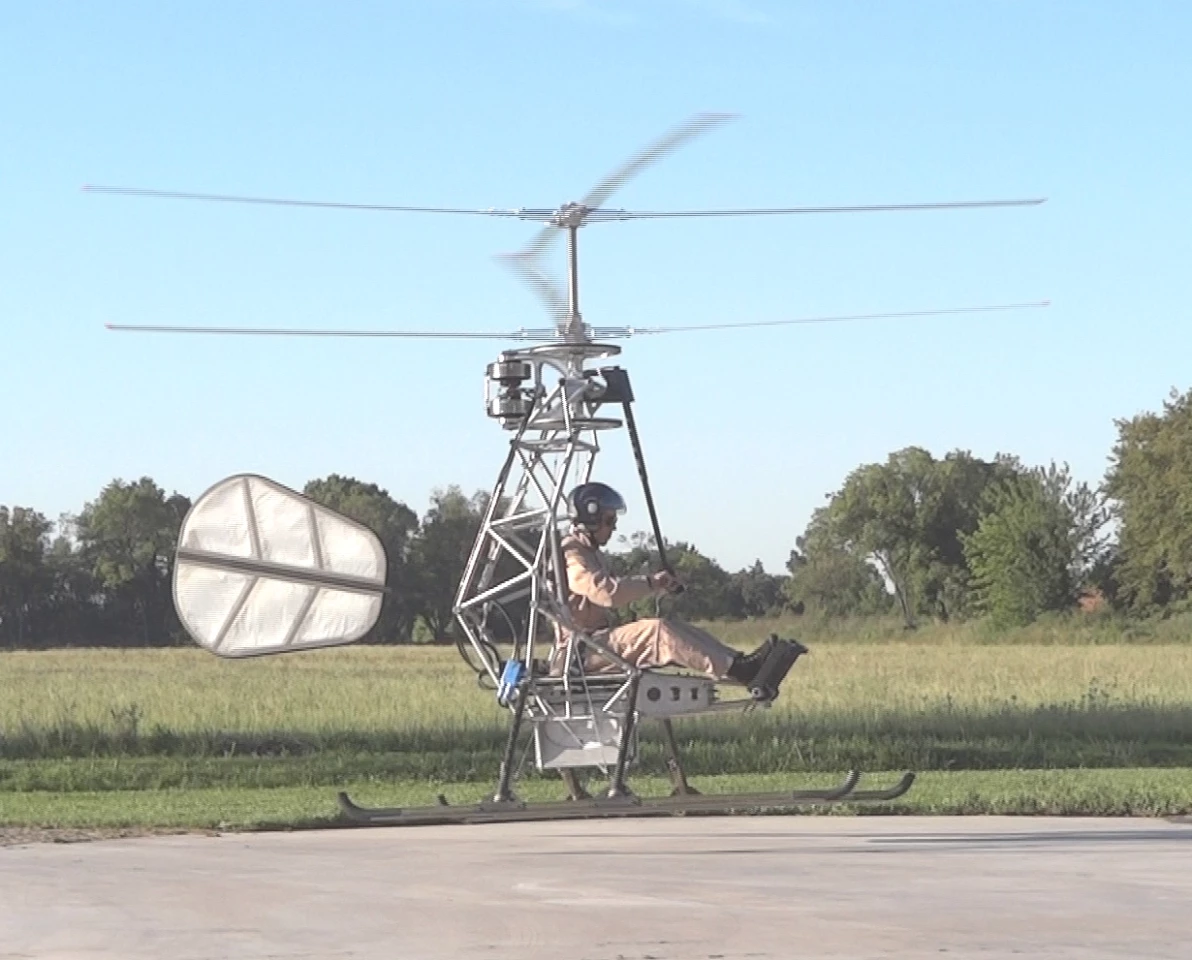
Test flights
Chretien initiated a few tethered test flights earlier this year, and was able to test the action and torque balance of the rotor controllers, the weight-shift directional tilt system and the ground effect behavior of the aircraft.And then, on August 12, it was time for the main event - the world's first untethered, manned flight of an electric helicopter, an event which lasted 2 minutes, 10 seconds up to a maximum height of 1 meter.
In this moment, Chretien and Solution F beat aviation goliath Sikorsky to the punch - Sikorsky has been working on its own project to get the first manned electric helicopter in the air, and unveiled its pre-flight Firefly prototype at the Experimental Aircraft Association AirVenture exhibition in July 2010.
But the Firefly is a much more conventional helicopter than Chretien's creation - it uses a conventional enclosed body shape, a single top rotor with a conventional swashplate and cyclic control, and a tail rotor - all of which add considerable weight, requiring additional heavy battery packs. This may have contributed to the fact that Sikorsky hasn't been able to run its first manned flight yet.
It's perhaps a little ironic that Chretien beat Sikorsky to the punch using a coaxial twin-rotor design, as Sikorsky is one of the leading proponents of coaxial helicopters - notably pushing a demonstrator version of its X2 to an unofficial helicopter speed record of 250 knots just last year.
Where to from here?
While he works on expanding the device's flight envelope, Chretien has a few things to think about after his pioneering test flight. The electric drive train needs more work, for example, and Chretien believes that "looking at the excellent power reserve we have today, it appears that we could have used a conventional cyclic [control] stick." Before he takes the helicopter out of the ground effect zone - or above about 4 meters - he wants to refine the current yaw control setup.
Eventually, Chretien sees a hybrid drive train being the ultimate outcome of this project. To understand why this is important, you need to understand that at present, helicopter flight is nearly 40 times as dangerous as airplane flight, at about 23 deaths per million flight hours versus just 0.6 for aeroplanes.
Current figures, Chretien says, put engine failure and internal/mechanical failures down as responsible for over 40% of helicopter crashes. But if a helicopter was to use a hybrid power system, you could store backup power in the battery. Chretien says a simple system could offer 3-4 minutes of battery powered flight if the petrol engine failed, enough to land the craft safely and help to reduce that 40% of crashes.
So as he works on patents in that area and further developing his prototype electric helicopter, Chretien is certainly a busy man - he's had just six days off since last August and it's hard to see how things will slow down from here!
We wish him all the best and congratulate him on his new place in the history books.