Everybody but the oil companies wants electric aviation to take off as quickly as possible, if you'll pardon the pun. The aviation industry is a huge polluter, and electric aircraft will not only be cleaner, but significantly cheaper in terms of energy and maintenance. The problem is batteries, whose terrible energy density is simply not up to any practical aeronautical purpose at this stage, and there's no guarantee that the vast amounts of research going on in the battery sector will change that any time soon.
Many companies are now starting to view hydrogen as the answer. Batteries are still a much better solution for 99 percent of car usage, but hydrogen's outstanding energy density makes it a much better proposition for anything that flies, and you don't need to build a massive distribution network to commence medium-range hydrogen flights. Indeed, if you can get electricity to an airport, you can generate your hydrogen right there on site.
We caught up with Val Miftakhov, founder and CEO of ZeroAvia, a company that's betting heavy on hydrogen in the aviation space. Where some are focused on the short-range eVTOL air taxi market, ZeroAvia is getting started on mid-range regional flights by developing and retro-fitting fuel cell powertrains to small, 10-20 seat passenger planes. The company says it can reduce costs by as much as 50 percent on this kind of operation.
If you're in doubt that hydrogen aviation is going to be a thing, Miftakhov makes an excellent case for it in the lightly edited transcript below. He's not competing with batteries, he's competing with jet fuel, and the numbers look like they might really stack up in the very near future. We'll let Miftakhov take it from here in his own words.
New Atlas: Hi Val, where are you speaking to us from?
Miftakhov: I'm in Cranfield, UK, we have a location here at a small airport belonging to Cranfield University, one of the best aerospace schools in Europe. Cranfield Aerospace Solutions is one of the partners for us and we're doing some of our testing here.
Can you sum up how ZeroAvia came to be and where you're at right now?
My background is in physics, management consulting, Google, Uber, then I started my previous company in the electric vehicle space, eMotorWerks – we became the largest vehicle-to-grid integration company out there. That company was acquired two years ago and that's when I started ZeroAvia.
I'm a pilot myself, a private pilot flying airplanes and helicopters, so it's a personal passion for me. Having spent a number of years in the zero-emissions transport space, it made a lot of sense to focus on aviation, look at what sustainability in aviation might look like and how we can bring it to the world.
We thought early on about how we can address the large existing segments of aviation. There are a lot of companies focusing on urban air mobility, flying cars and so forth. We thought that these are all great projects, interesting technologically, but they wouldn't do anything to our emissions footprint in the existing aviation segment. If you're flying from Melbourne to Sydney, that's not going to be helped by any of the flying car companies today.
That was the motivation: how we can start bringing those segments into the zero emissions world. Once you do the math, and start trying to understand what technologies you can use to get there, pretty quickly you'll zoom in on hydrogen-fuel-cell-based powertrains. There's nothing else that really works that well.
Batteries are too heavy, biofuels cannot scale, hybrids with turbine engines don't really make sense – you're increasing the complexity of the powertrain for relatively limited gain on longer trips.
What remains are hydrogen-based propulsion methods. One is hydrogen-electric, and that's what we're doing with fuel cells. Another is synthetic fuel, which uses the same turbines as you have in aircraft today, but produces fuel from hydrogen into synthetic liquid jet fuel. The latter is more expensive, requires more energy and still has all the disadvantages of liquid fuel burning: particulate emissions, nitrogen oxides, turbine engine maintenance and so forth.
We think that hydrogen-electric is going to be the dominant force over time in clean aviation, and that's why we're doing it.
So where are you at with it?
We started at the end of 2017. In 2018, we put the initial team together and started ground testing of our powertrain. It's a California company, with a UK subsidiary. In February 2019, in the US, we put the first version of our powertrain in an aircraft, a six-seat, two-ton Piper Malibu M330.
We got initial FAA certification on that prototype, and got it up in the air in the spring of last year. Started flight testing, learned a lot. Earlier this year, we built the second prototype here in the UK. The UK operation is supported partially by government grants here from the Aerospace Technology Institute.
Now I'm here in Cranfield kicking off flight testing for the second prototype.
Do you see any specific barriers to certification for hydrogen-electric powertrains?
Well, the main barrier really is the lack of standards for these new powertrains. If you build a new piston engine or a new turbine engine, you have a testing book. You can show up to the certification authorities and they'll pull out the book and say right, these are the tests we need to run, this is how long we need to run your engine, under these parameters, and everything is described. When you design and test the engine before the certification, you'll know what to expect.
From a technology and physics perspective, there are no physical barriers.
In the case of new engine types, and that includes battery-electric and any others that aren't traditional engines, and definitely hydrogen-electric, you don't have a book. So first and foremost, you need to work with the regulators to write the book. That's what we're doing now already with the FAA in the US and the CAA here in the UK, so that in 12-18 months, we can show up with a system that we think can be certified, and there will be a book against which it can be tested.
So this is the main barrier. From a technology and physics perspective, there are no physical barriers.
I was talking to the HyPoint turbo air-cooled fuel cell guys a couple of weeks ago. There seems to be a perception out there that a hydrogen powerplant is inherently dangerous in an aviation context. Can you speak to that?
Yeah, the HyPoint guys are great. We're partnering with them on a couple of things. But this is a frequently asked question for sure. A lot of times people bring up the Hindenburg from 80 years ago. But technology has moved on quite a bit.
Today, on the ground, hydrogen fuel cell vehicles are a real thing. Since about five years ago, Toyota started pushing hydrogen cars onto the market to regular consumers, with fueling and everything. So there's now maybe 15,000 hydrogen vehicles in circulation on the ground worldwide, plus maybe 30-35,000 material-handling equipment. Not in the air, but the technology, the storage and utilization of hydrogen in those vehicles is similar to what you have in the air. Fuel cell tech with compressed hydrogen storage that you produce electricity out of.
In our conversations with the FAA and CAA, hydrogen is something they find to be more conceptually similar to the other chemical fuels, compared to batteries. In the hydrogen-based powertrain, you have fuel storage where fuel is kept separate from the oxidizer – the air – at all times, except for a very small amount that flows in the fuel cell. That's versus batteries; what makes people worry is that the fuel and oxidizer are all in one package, impossible to separate if something goes wrong. So you have these runaway effects in large-scale, high-energy-density batteries that are very hard to contain. Once a battery fire starts, for example, it's very difficult to stop.
So it's conceptually quite different and, if anything, the certification authorities are unclear about how to deal with batteries as opposed to chemical-based fuels like hydrogen.
Then you look at things like ignition temperature of hydrogen – much higher than jet fuel. It's practically impossible to pool hydrogen in one place, or maintain a concentration in the open air. It's very lightweight, it escapes very quickly. Jet fuel and aviation gasoline have vapors that are really heavy, and they concentrate around the leaked fuel. Those can ignite much more easily.
So there are some fundamentals for hydrogen that are actually better than jet fuel from a safety perspective. Of course, we'll need to do the right amount of testing and so forth. But we're pretty optimistic.
So obviously, liquid hydrogen or compressed hydrogen can have a far greater energy density than a lithium battery at this point. But how does it compare, energy-density-wise, to something like jet fuel?
On the energy density per kilogram, it's very good. From a chemical energy or primary energy perspective, hydrogen is about three times better. Every kilogram of fuel contains three times more energy.
You get additional benefits from using it in a fuel cell, because small internal combustion engines are not efficient. You have typical efficiency of 25-30 percent for a piston engine or small turbine engine. In a fuel cell, you can have a 60-percent efficiency, and the entire powertrain can be about twice as efficient as compared to a classic internal combustion engine.
So now you have a six times advantage in terms of the propulsion you can derive from one kilogram of fuel.
The challenge with hydrogen is to store that fuel. A classic way to store it is with compressed gas cylinders. The ones that we're using, the tank technology allows us to achieve about 10-11 percent mass fraction, mass fraction being what percentage of weight of your tank system is actually fuel. So only 10 percent of our total tank weight is fuel. In order to store one kilogram of fuel, we need 10 kilograms of fuel system.
That's an immediate factor of 10 reduction to our energy density per kilogram, so your six times advantage takes a 10 times disadvantage, and it works out to about half the utility of the jet fuel for the same mass of fuel system if you're using compressed hydrogen.
That highlights where the challenge really is at the system level with hydrogen. It's a very energy-efficient, energy-dense fuel, but containing it and storing it onboard is a real challenge.
That's why people think about various liquid hydrogen technologies that allow you to get mass fractions above 30 percent, three times better. Aerospace tanks used in rockets, for example, have mass fractions of 70-90 percent, but would, shall we say, require some modifications before you take them into the aircraft (laughs).
Even at a 30-percent mass fraction, which is relatively achievable in liquid hydrogen storage, you'd have the utility of a hydrogen system higher than a jet fuel system on a per-kilogram basis.
... there's significantly more hydrogen in one liter of water than in one liter of liquid hydrogen.
The only remaining challenge that you'll have at that stage is volume. Hydrogen, even in liquid form, is not very dense in terms of how many kilograms you can store in a unit of volume. Your tanks need to get bigger.
The fun fact, I guess, that's sometimes amusing, is that there's significantly more hydrogen in one liter of water than in one liter of liquid hydrogen. It's so lightweight that even when you liquefy it, it's just 80 grams per liter. Twelve times less density than a liter of water, and about nine times less than jet fuel.
And if you introduce that factor, you've got to build a larger airframe, which then adds to the weight again?
That's right. So the way we're approaching it initially is to say we're just going to take a hit on the max range of the vehicle. All the benefits of zero emissions and lower costs of fuel and maintenance are great, and we're going to deliver them with about half of the max range of a fossil fuel vehicle.
Our first targets in terms of aircraft are 10-20-seat aircraft, for example Cessna Caravans, Twin Otters, single- or twin-engine aircraft carrying 10-20 people. Those airframes are typically designed for about 1,000-mile (1,609-km) endurance on jet fuel. We'll be able to deliver a range of about 500 miles (805 km) in a 10-20 passenger aircraft using compressed hydrogen storage.
And that, we think we can put into commercial utilization within about three years. So yeah, the point is, there's a way to deliver a very meaningful utility to the market with this type of powertrain in a very short timeframe. That's what we're really excited about. And it can scale beyond those initial aircraft and ranges through utilization of liquid hydrogen and more efficient fuel cells.
OK. So your initial plan is to buy regular aircraft and retrofit them, or will you design your own airframes?
We're an engine company, so we'll produce powertrains or engines that could go into various types of aircraft. Initially probably into existing aircraft on a retrofit basis.
And from the start, some will go to new aircraft, say as people build new Cessna airplanes and send them to FedEx, for example – they're a big customer for Textron or Cessna, and flies possibly the largest fleet of small aircraft worldwide, for transporting packages into remote locations. That's a great example where we could go and re-power the fleet, so to speak, and as new aircraft get purchased, we could also power them.
Over time, especially as we move into the larger airframes, we expect the manufacturers to begin to optimize their airframes for this new propulsion type, just as happened with jet engines mid-last century. Initially it was applied to airframes that looked the same as the propeller planes, but they soon began morphing the aircraft to increase the advantages of that type of propulsion.
We're going to see the same thing here. We'll start to see higher volume airframes, some manufacturers are already experimenting with some things. Airbus MAVERIC, if you've seen an announcement a couple of months ago, they're doing some flight testing on a couple of small prototypes with a wing-body design that has a lot of volume. Great for storage of a fuel like this.
We're going to see more distributed propulsion, which is easy to do with electric powertrains, since you can separate a large number of motors around and not suffer the efficiency and complexity penalties you have trying to do the same with turbine engines. Small turbines are less efficient than big ones, so every time you break one large engine down into two smaller ones, you lose efficiency, and you take a double hit when you have to do twice the maintenance. That's one reason why you're seeing the retirement of a lot of the four-engine aircraft like the 747, in favor of planes with two large engines.
With electric, you don't have that problem, you can scale very easily up and down, and aerodynamically distributed propulsion makes a lot of sense. You can make a much more efficient aircraft by placing more propulsive elements around the airframe.
So that's going to happen over time. But initially, you take the existing types of aircraft in the installed base, and you start re-powering them.
Initially propeller planes?
Initially, yes.
What other options are there down the track apart from props and ducted fans? You can only get up to a certain speed with a propeller, yeah?
It's true. That's an interesting question. The semantics is a big tricky, but maybe you can say you have three types of propulsive element types. Propellers, where all thrust comes from a propeller. Then you have jet engines of various types, where they thrust comes mostly from the jet exhaust – those are not speed constrained, but not very efficient.
Then there's turbofan engines, which are kind of a hybrid in between. Part of the thrust coming from the jet exhaust, part of the thrust coming from the rotating propulsor, which is structured as a fan to work better in high speed environments. But still subsonic. That's what exists today.
We probably won't see supersonic electrified any time soon.
To go supersonic, you almost always need relatively low bypass engines; you have high exhaust velocity, so a significant proportion of the exhaust needs to be composed out of the jet exhaust high-speed air. You can blend some of the low speed fan-pushed air, but not a huge fraction.
For the initial time for sure, we're going to see similar approaches in electric. We probably won't see supersonic electrified any time soon.
Will this technology be able to go as fast as an airliner? They get around at 900-plus km/h (559-plus mph), how fast can a hydrogen plane be in comparison?
You can definitely mate the electric motors to a fan like you'd find in a typical turbofan engine on a classic 737 or whatever. It's just a matter of what propulsor you use, instead of a propeller you can use a fan and rotate that.
With time, maybe within 10-15 years, we can get there. We, meaning ZeroAvia as a company. We can get to a turbofan replacement engine that can be fitted into something like a 737 and propel it to similar speeds to what they do today.
From a physics perspective, the energy density is in a good place, the storage is possible with liquid hydrogen, to match or exceed the energy content of jet fuel. All those things are possible given enough engineering time.
So definitely subsonic, but we see hydrogen matching the utility of the jet-fuel aircraft over time. For smaller aircraft, it'll be sooner, so the first product to production is three years out. Probably five or six years, we'll see similar ranges to jet fuel in small aircraft.
In 15 years, let's say, we're going to see similar ranges in larger aircraft. These are all relatively small amounts of time in the aviation world, where they typical lifespan of a vehicle is 30 years. If you sell a brand new 737 today, it'll be just retiring in 2050. So on that timeframe, within a generation, within that 30 years, you can give all forms of air travel a hydrogen-electric option.
It's a matter of how quickly it gets adopted. That depends on government policies, cost of technology, cost of fuel, prevalence of fuel and all those things. But it's technologically possible over that period of time to have solutions for all segments.
Do you have a sense, taking the FedEx model you raised earlier, of what sort of cost savings an operator might enjoy based on the reduced maintenance, cheaper fuel, all that sort of thing?
This is a bit of a moving target, as the cost of green hydrogen is reducing quite quickly. The learning curve is just starting on green hydrogen electrolysis, it's getting cheaper. Energy is already pretty cheap from the renewable assets.
So already, three years out from our first commercial offering, we're easily seeing hydrogen at equivalent jet fuel prices around US$1.50 per gallon. I talk in terms of equivalent prices, because when I talk about it as $2.50 per kilogram, nobody has any reference. So we convert it into the equivalent jet fuel price, meaning it gives the same amount of mobility. Passenger kilometers. How much jet fuel you'd burn, and that converts to the price of hydrogen.
So $1.50, which is lower than what we've seen over the last few years for even large operators like FedEx and major airlines. Of course, now, during COVID-19, with the oil prices a little on the low side, the jet fuel will be a little bit cheaper.
But already it gives you an idea that hydrogen is quite competitive on the fuel price even three years out. And when you talk about 10-15 years out, when electrolysis equipment and renewable energy is at lower cost than today, you can see for smaller operators, easily a 50-70 percent advantage. For larger operators, maybe a 20-40 percent advantage.
One of the interesting benefits on top of that is stability of pricing. The volatility of jet fuel price is a big problem for the aviation industry in general, and people have all kinds of hedging schemes that cost money. With this, you won't have to do that. If you're sourcing your fuel from electricity, then there's potentially multiple sources, and renewable electricity is relatively reliable over time. That's an interesting advantage there.
On the maintenance side, it's an electric powertrain – electric motors and energy distribution – which is much more reliable in general than internal combustion engines.
You see that in cars; what happens is you just stop going to the mechanic if you have an EV. You can have it for three years and never have to do anything with it. That's not a good look for internal combustion. There are very few moving parts and everything just works, and it's kind of similar for the aviation side of electric powertrains.
We see at least a 30-50 percent improvement in the times to overhaul, and even bigger improvements for smaller engines. The overhauls would be cheaper than for today's jet engines, because the main thing you'd be worrying about is the hydrogen fuel cell stack, which is only a part of the powertrain, and can be made in a relatively modular way so you can diagnose and replace it pretty easily when you need it, which would again be over a longer timeframe.
What about the fueling side?
Obviously it's a new kind of fuel, so we need to build or orchestrate the fueling infrastructure around it. There's a lot of comparison that people make to the ground-based hydrogen fueling infrastructure for cars, which had a lot of challenges being built out across the world.
It'll be a much easier situation here with aircraft. You have relatively few locations you need to enable worldwide: the airports, right? You know where they are, and the energy consumption is quite concentrated. That's a very different situation compared to ground transport, where everything is highly distributed. You need to place a lot of low-volume stations, which kills your economics.
Here, in aviation, you can start with a limited number of locations, work with initial operators, and scale from there. It's a much more scalable way to introduce a new fuel, and it works quite well even at low scale. So it's a very different proposition to ground mobility, and I think it'll play to the advantage of hydrogen aviation.
Assuming some of these sites will be electrolyzing water into hydrogen on site at an airport, how quick is that process? Would you need large storage facilities on site, or could you almost electrolyze straight into the aircraft's fuel tanks?
There's an optimal amount of storage, depending on your energy source. Typically, you'd have at least a couple of days' worth of storage on-site, or near-site, and you'd dispense from there. There are economic reasons for that too; you ideally want to minimize the electrolyzer size, as that's directly related to capital expense, so you'd provide a 24/7 electricity source and have the electrolyzer running near its max setting full time.
The way you provide that 24/7 renewable power source is you have some battery storage on site, so it might allow you to take your standard five or six hours of solar per day and spread it out over a 24-hour period, and do that every day. So there are some system optimization algorithms we're working on with our fueling partners to minimize the end cost of the fuel. That's how you get to the really good numbers that compete with jet fuel.
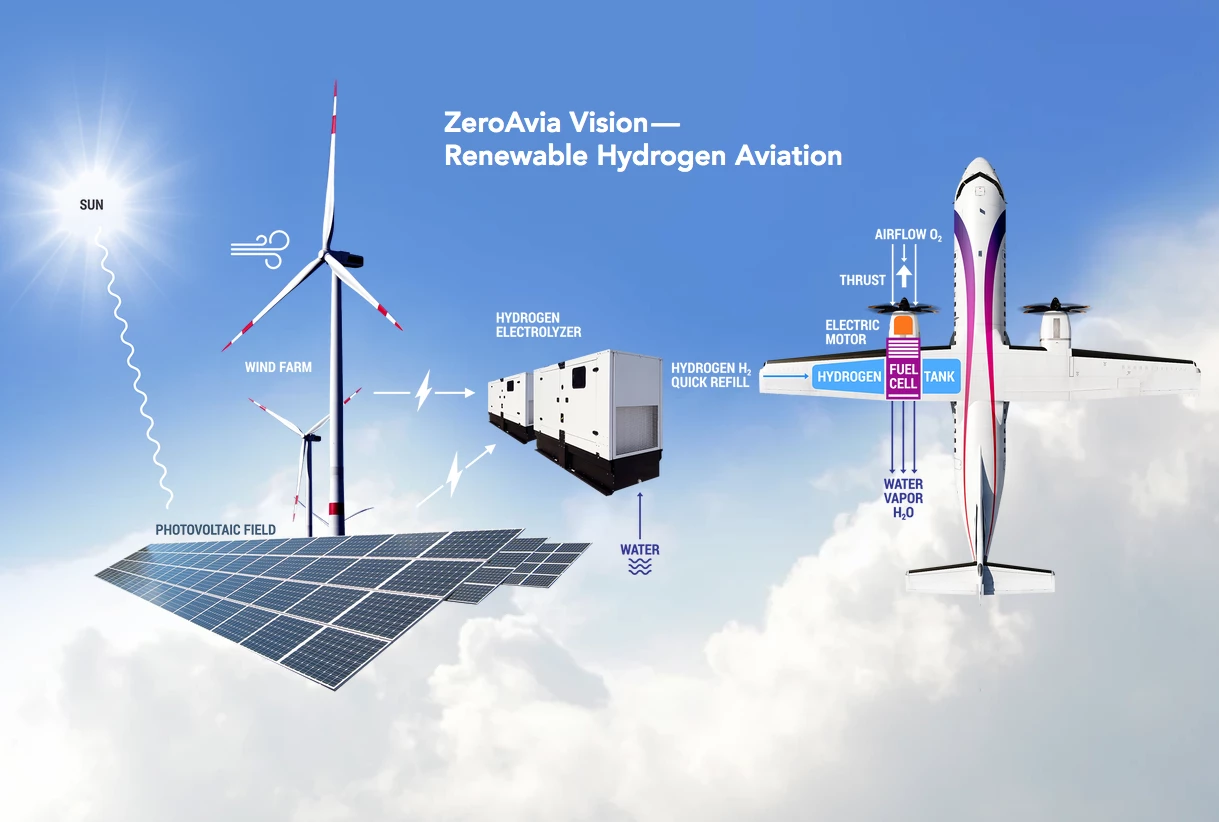
Solar on site at an airport? You'd need a lot of space.
We've done a few back-of-the-envelope calculations for a lot of different airports, and we've found for the vast majority of the south-western United States (and probably the same for Australia actually), you can re-power all regional flights with the electrolysis generated from solar energy from solar panels located only within airport property.
There's a large amount of unused space at airports, and if you covered it with solar panels, the energy would be sufficient to re-power all regional flights out of those airports – regional meaning sub-500 mile flights. So there's already an amount of space available. Now, will you be able to put that large of a solar array on the airport property, near the runways and all that? That's a question. But the space is there.
I guess I always figured that space was there for a reason.
Well, you can't build anything tall there. It has to be on the ground. No structures, pretty much, in that space. But solar panels lying on the ground would clear the height requirements. Then you'd have things like reflections off the solar panels that you'd need to deal with. But from a height perspective, you wouldn't have a problem.
And you need to have access of course, to runways and taxi ways, so you'd need to figure that out, but I think that's doable. But if anything, solar panels are probably the easiest thing to place on the ground at an airport.
Generally, the reason that airports have that much space on the ground is that they typically have multiple runways, which are at angles to one another due to the wind directions. Take SFO International, that has four runways, two pairs at almost 90 degrees to one another, because the wind direction changes. You always want to be taking off or landing your aircraft into the wind, so they switch runways when the wind changes.
So if the runways are two miles long, then you have a 2x2-mile surface, give or take. That's the main reason why the surface requirements are so high for large airports. And even smaller airports, a lot of times, have multiple runways at angles, and they have a lot of space.
The airport we're using for our flight testing in the US, Hollister, has two runways at about a 70-degree angle, and even that small airport takes up a lot of space. That space can be used, and probably will be used over time, for some useful purpose. We hope it'll be generating the electricity for hydrogen planes.
We thank Val Miftakhov for taking the time to speak to us.
Source: ZeroAvia