German steel giant Thyssenkrupp is investing US$1.9 billion in a hydrogen-powered direct-reduction system that can create high-quality steel without needing the rare, high-grade iron ore required by most green steel processes. This could open the floodgates.
Every ton of conventionally produced steel puts nearly two tons of carbon dioxide into the atmosphere, and humankind uses so much of the stuff that steel production contributes somewhere between 7 to 8% of global carbon emissions every year. Cleaning up this massive emissions disaster over the next quarter century is imperative, and a daunting challenge.
But the technology to make green steel is well understood and already in use. You stop using fossil-fired blast furnaces to release the oxygen from iron ore, and you stop using baked coal, or coke, as a reductant to add the critical small percentage of carbon to your iron. Instead, you use green hydrogen in a direct reduction process, both as your reductant and to power an electric arc furnace to supply the heat. Instead of tons of carbon dioxide, this process emits water.
Sweden's H2 Green Steel has the jump on the green steel market for the time being. Its $3 billion facilities are expected to pump out some 5 million tons of high-quality zero-emissions steel annually by 2030. But the mainstream is making moves to catch up; ArcelorMittal, the world's second-largest steel producer, will be producing 1.6 million tons of green steel a year by 2025 at a new zero-carbon plant in Spain.
Now Germany's Thyssenkrupp has committed the funds to replace one of the giant blast furnaces at its Duisburg site with a direct-reduction system, which will begin producing around 2.5 million tons of "low-CO2" steel from 2026.
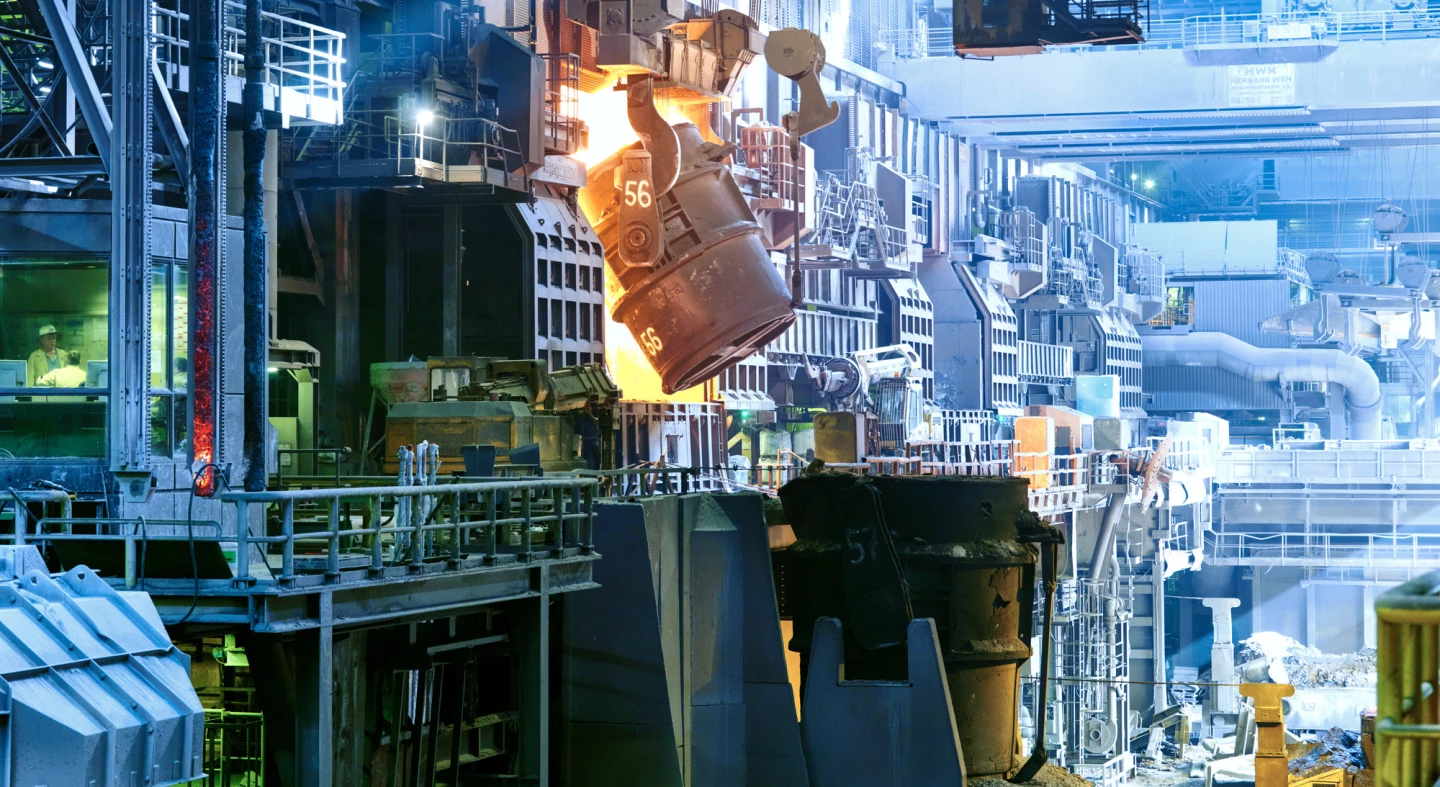
While it's not totally green – Thyssenkrupp plans to feed the iron produced in the direct-reduction facility into melting units, and send the hot iron back through its existing plant structure – this design could still be of enormous significance to the wider steel industry, because it can reportedly produce high-quality steel using lower-grade iron than other direct reduction processes, as Renew Economy points out.
That's a big deal, and not just because the super-high-quality (>67% Fe) iron ore required by most electric arc furnaces is more expensive than lower-grade ore, pushing up the price. More importantly, only some 4% of today's global iron ore supply meets this mark, so the raw materials don't exist to decarbonize the entire steelmaking sector.
Thyssenkrupp's process allows it to use blast-furnace-grade iron, according to the Institute for Energy Economics and Financial Analysis, removing any chance of a materials bottleneck and clearing the path for a much quicker shift to green – or at least low-emissions – steelmaking.
Source: Thyssenkrupp via Renew Economy