Concrete is one of the most common materials on Earth, thanks to its high strength and low cost – but it’s also one of the largest single sources of carbon dioxide emissions. Engineers at Washington State University (WSU) have developed a new method for making concrete that absorbs more carbon than it emits.
The process of making cement requires very high temperatures, and that usually requires burning fuels which, of course, emits CO2. That can be partly offset by switching to renewable energy sources, but chemical reactions in the mixture also release huge amounts of CO2, and this is harder to avoid. All up, it’s estimated that cement production accounts for as much as 8% of humanity’s total carbon dioxide emissions.
Scientists have been tweaking the formula to try to reduce concrete’s carbon footprint, by substituting limestone for volcanic rock, or adding ingredients like titanium dioxide, construction waste, baking soda or a clay commonly discarded during mining. Other teams have even tried using microalgae to grow the required limestone.
For the new study, the WSU researchers investigated a new method involving biochar, a charcoal made from organic waste. While biochar has been added to cement before, this time the team treated it first using concrete washout wastewater. This boosted its strength and allowed a higher proportion of the additive to be mixed in. But most importantly, the biochar was able to absorb up to 23% of its own weight in carbon dioxide from the air around it.
In experiments, the team created cement that contained 30% treated biochar, and found that the resulting concrete was carbon-negative – it actually absorbed more carbon dioxide than was emitted during production of the material. By the researchers’ calculations, 1 kg (2.2 lb) of the 30%-biochar concrete removes about 13 g (-0.5 oz) of CO2 more than its production releases. That might not sound like much, but considering regular concrete is usually responsible for releasing about 0.9 kg (2 lb) of CO2 per 1 kg of material, it’s a stark difference.
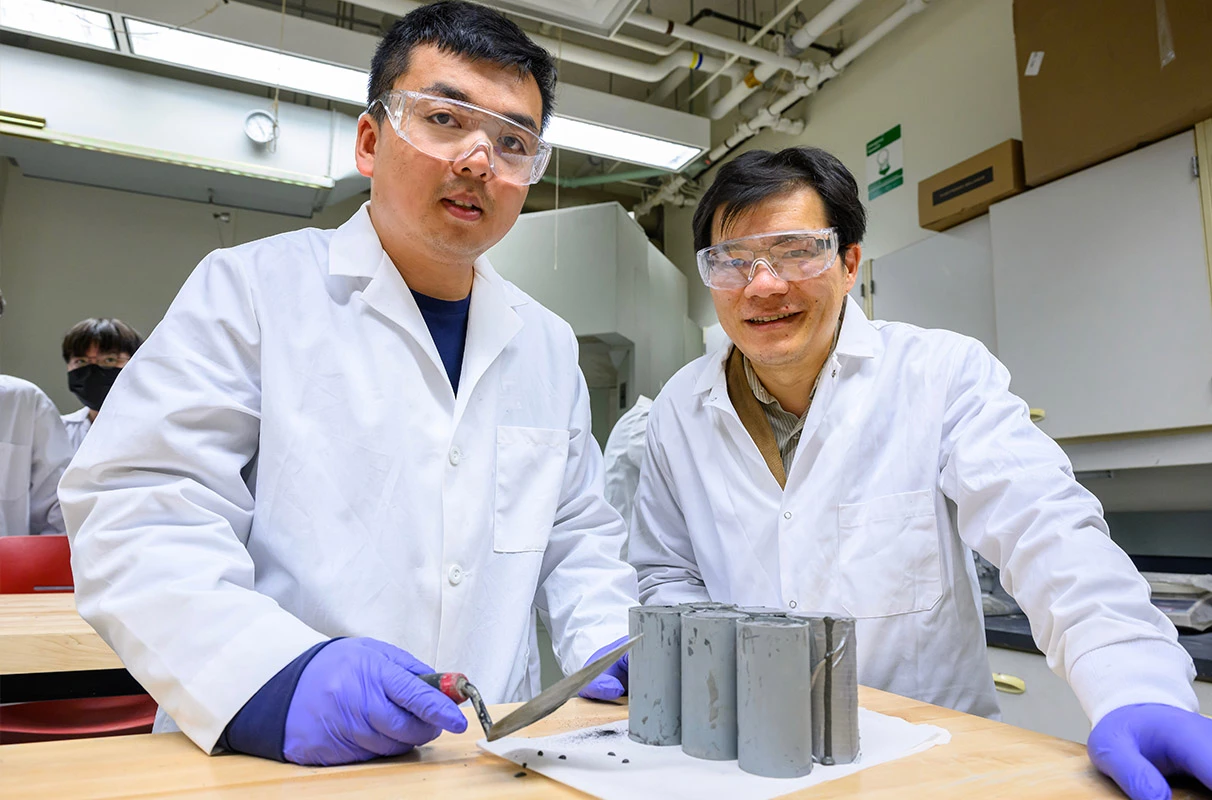
The total gains could be even better, the team says, if downstream differences were accounted for in their analysis. For example, using biochar for environmentally friendly purposes like this concrete diverts the biomass it’s made of away from other fates that could potentially release more CO2. Plus, the new concrete would be expected to continue absorbing CO2 during its working lifetime of several decades.
Importantly, the biochar-concrete also retains its strength. When measured after 28 days, the compressive strength of the concrete was 27.6 MPa (4,003 psi), which is around that of regular concrete.
The researchers plan to continue optimizing and scaling up the method, and testing how well the resulting concrete resists weathering and other types of damage.
The research was published in the journal Materials Letters.
Source: Washington State University