East Coast aviation company Alakai made big headlines last year when it became the first eVTOL air taxi company to put hydrogen on the table as a way to get around the battery bottleneck that's holding so many competitors down to short flight times with long charging waits in between.
Hydrogen, as beautifully explained by ZeroAvia's Val Miftakhov in our recent interview, could well become the fuel that finally gets aircraft running clean. With a much higher energy density than lithium batteries, it offers genuine long-range flight capabilities, as well as fast refuelling. Used in a fuel cell electric powertrain, its only local emissions are water, and there are a growing number of ways to produce it in a completely green and sustainable fashion, some of which are beginning to become cost-competitive with jet fuel.
So Alakai was able to draw up a plan for a comfortable, very schmick-looking air taxi design in partnerships with BMW's DesignWorks, and make a credible claim that it could blow all its competitors' range figures out of the water using liquid hydrogen as an energy source.
What's more, it could hit its 400 mile, 4 hour flight endurance targets using the simplest possible airframe: a 6-rotor multicopter. No wings, no tilting rotors, no transitioning between flight modes; Skai's hydrogen powertrain had so much energy to spare that no such complicated efficiency measures were necessary. This simplicity, CTO Brian Morrison told us, was key to another Skai advantage: he believed it would be far quicker to certify than the competition. "It'll fly next week, and it'll be certified next year," he told us last year.
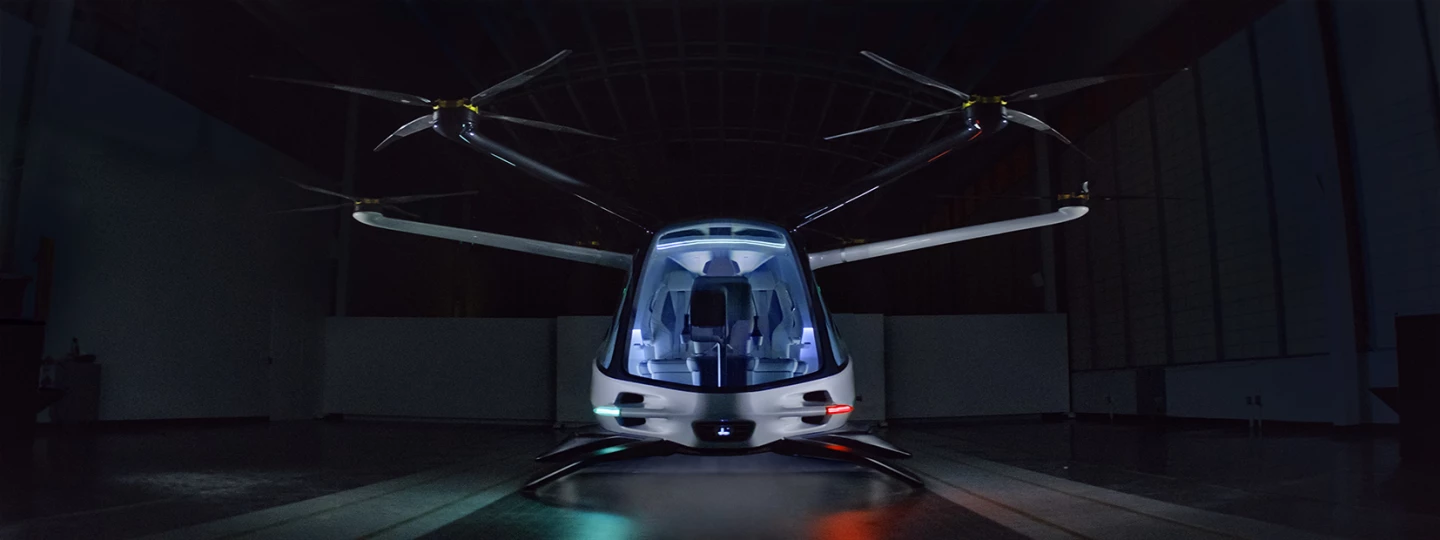
Where Skai is at right now
"I think some of the statements made previously were perhaps overly ambitious, made in the excitement of the moment," says Skai's Chief Marketing and Sales Officer Bruce Gunter, almost exactly a year later as we catch up with Skai for an update on where things are at. "But that's what happens when you're pushing the envelope in that respect. We're working hard to get there."
"At that time," says Skai CEO Steve Hanvey, "we were running on the ground, putting all the systems in, but we were basically proving the science of a hydrogen powered vehicle of that size – between 3-4000 pounds. We're not aware of anyone in the world doing a liquid hydrogen powertrain at these kinds of weights right now."
So where is Skai actually at right now in the development cycle? Well, the original Skai airframe made it to the tethered flight stage, and now the company has iterated to a second generation design, which is approaching completion with mainly systems work remaining. The testing, up to this point, has been unmanned, and Hanvey has been flying the full-sized airframe with a drone-style controller. We've seen video footage of this, although it's not for public release as yet. The team is currently approaching 40 people, but has expanded as high as 70 with various contractors.
The target for manned flight has shifted to early 2021, but Hanvey won't be surprised if it takes longer: "Igor Sikorsky once said to me, when you're doing these kinds of technology projects, don't try to predict the future, because it tends to change," he says. "Right now, we're capable of flying it from the ground. In fact at this point I'm flying it about 50 feet away from the aircraft. Very quiet, very little air wash compared to a traditional helicopter. I'm flying it with my thumbs like you'd fly a drone. In the software, it's capable of taking off and hovering by itself, but we prefer to have physical control."
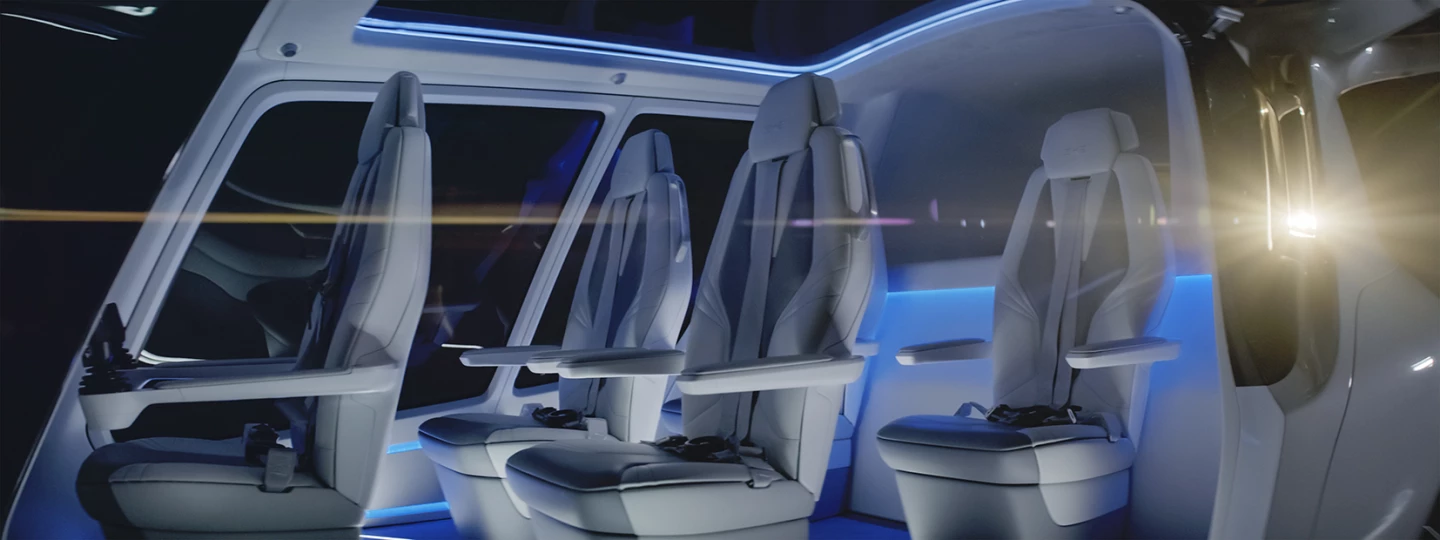
As for certification, Skai is about two years into what's typically a five-year process with the United States FAA. The company has an experimental ticket application ready to go for when its airframe is ready to fly off tethers and take a pilot, but hasn't asked the FAA to approve it yet. There's an approved FAA project plan, and the team is working with FAA regulators on how the certification process for these radically new eVTOL aircraft will be certified.
Hanvey stresses that he and the Skai team have a wealth of experience in this area. "I've been certifying aircraft since 1980," he says. "Military programs, helicopters, fixed wings, small and large, Our whole team brings experience from the aerospace business around what it takes to get an aircraft successfully certified, and what does it take to support it."
With battery-powered competitor Joby Aviation targeting 2024 for certification, and Germany's Lilium among several companies talking about 2025 as a launch date for air taxi services, it now seems unlikely that Skai will gazzump the field and be first to market. But Skai's liquid hydrogen special sauce could still confer it some huge advantages if it's ready around the same time.
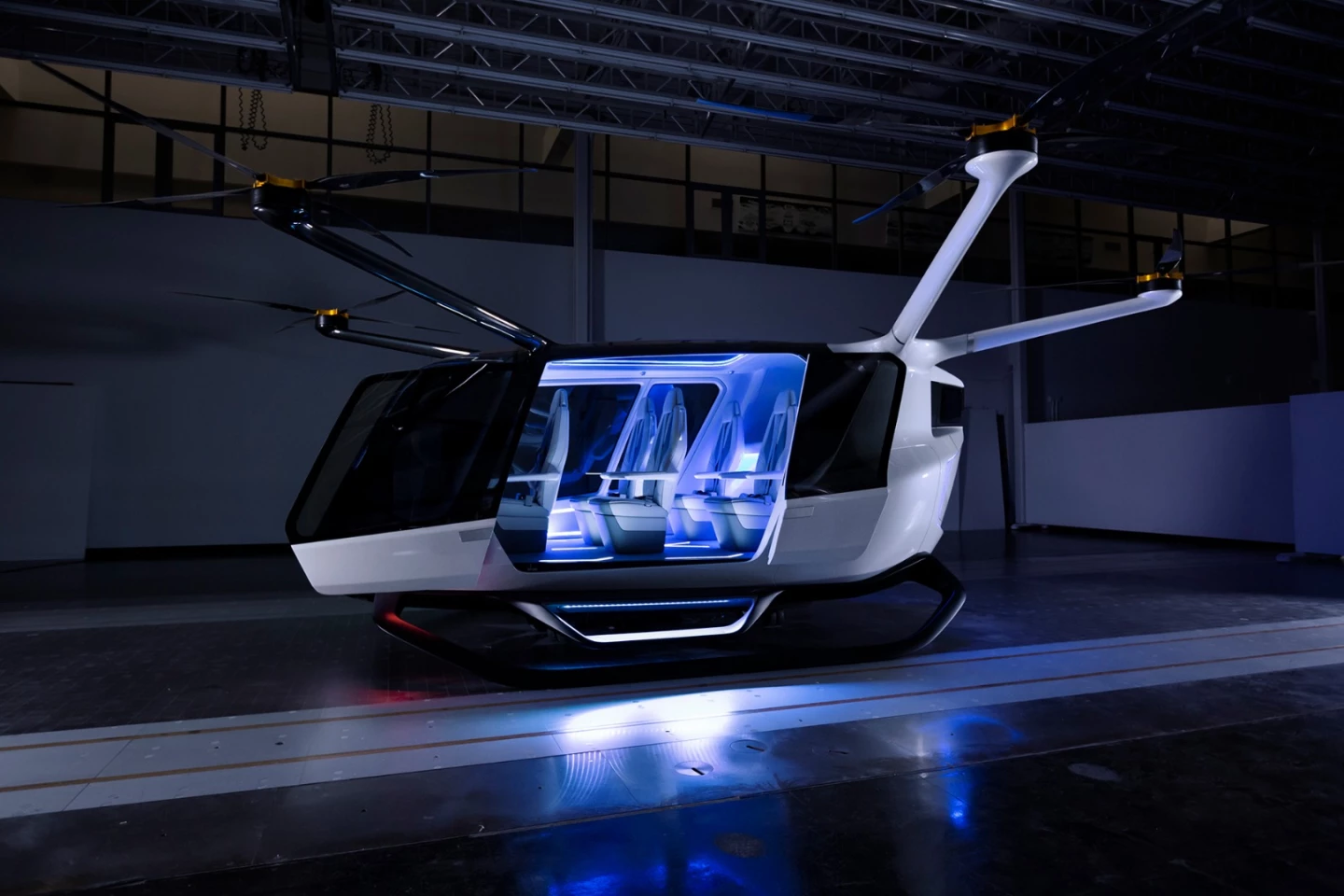
Skai's liquid hydrogen system
The decision to use a liquid hydrogen powertrain is unusual, but based upon the simple fact that you can carry more energy for a given volume and weight of tank space if you use liquid rather than compressed gas hydrogen. The fuel weight itself becomes almost negligible with hydrogen, it's the weight of the tanks themselves and the accompanying apparatus that count.
Where ZeroAvia talks about its gaseous hydrogen systems offering a 10-11% mass fraction (the proportion of the total full tank weight that represents actual fuel), and Val Miftakhov speaks of mass fractions as high as 30% being realistically achievable with liquid hydrogen, the Skai team isn't ready to talk much about its tank technology just yet.
"The specific numbers are proprietary to what we're doing," says Hanvey. "We're working with our tank people as to how much we can get in a tank, what the weight of the tank is, and what percentage of the total aircraft weight that is. We're working with folk that are leading edge on this, but it's premature to be giving numbers now."
One challenge for anyone who wants to work with liquid hydrogen is that you need to keep it extremely cold to keep it in its liquid state. At atmospheric pressure levels, we're talking just 20.28 kelvins above absolute zero (−252.87 °C, or −423.17 °F).
That temperature can rise a little if you're willing to pressurize as well as cool (using a cryogenic system running between 250 and 700 bar of pressure), but Gunter says that's not part of Skai's plans, as "even a moderately pressurized system has significant weight penalties."
So, super-cooling it'll be, and while that entails extra energy losses in the liquefaction stage, the cooling equipment, the conversion back into gas for use in the fuel cell and in boil-off in the tank itself, the net result will still be a much longer range aircraft than anyone dealing with gaseous hydrogen – or certainly lithium batteries – will be able to deliver.
It'll be interesting to see how Skai gets the job done, as really you've got to look to NASA and other space programs to find liquid hydrogen being used in serious volumes.
"The good thing in all of this," says Gunter, "is the notable developments that occur in this space on an increasing basis. The efficiencies we’ve seen in fuel cells and the same the industry is seeing regarding H2 production all point to increasing effectiveness of any form of H2 as a future focused solution."
"There's a number of naysayers about what we're doing with hydrogen," says Hanvey, "but we believe we've gone from the question to the possible, and it's now the probable. We know we can fly with hydrogen, and the question is just how quickly we can get it to the market. And based on our experience, we think we can get there a lot quicker than perhaps the market will give us credit for."
We look forward to following Skai's progress, along with the rest of the growing hydrogen aviation industry. If Skai and its partners can get liquid hydrogen safely and effectively working in aircraft, then not only could the dream of air taxis become a more practical reality, but the door would then open up a crack to the possibility of long-range zero-emission airliners as well.
Source: Skai