Jetpack Aviation's David Mayman and Nelson Tyler have already brought honest-to-god jetpacks out of the pages of science fiction books and onto the market. Now, they plan to do the same with flying cars. We spoke with Mayman at length about Jetpack Aviation's new manned VTOL multirotor project.
The age of the flying car will soon be upon us. Thanks to a convergence of technology developments – lithium batteries, multirotor drones, electric aircraft, cheap and plentiful inertial sensors – the three-dimensional commuting revolution is beginning, and a number of companies are making serious progress in the embryonic stages of this very exciting space.
One of the best overviews and forward projections in this space we've seen is the Uber Elevate whitepaper, which specs out and puts some numbers around a VTOL air taxi service, and what it would take in terms of regulations, infrastructure and price point to make the concept viable.
One unexpected new contender has just thrown its hat into the ring: Jetpack Aviation (JPA), a small operation out of Van Nuys, California, run by personal flight pioneers David Mayman and Nelson Tyler. The JPA team has made stunning progress in the last few years by developing the world's first jet turbine backpack – a wild sci-fi dream come true.
Mayman, as CEO and chief pilot, has been staging spectacular public flights of the JB-9 and JB-10 jetpacks all around the United States and Europe, and the company recently announced that if you've got the cash, you can actually buy one now.
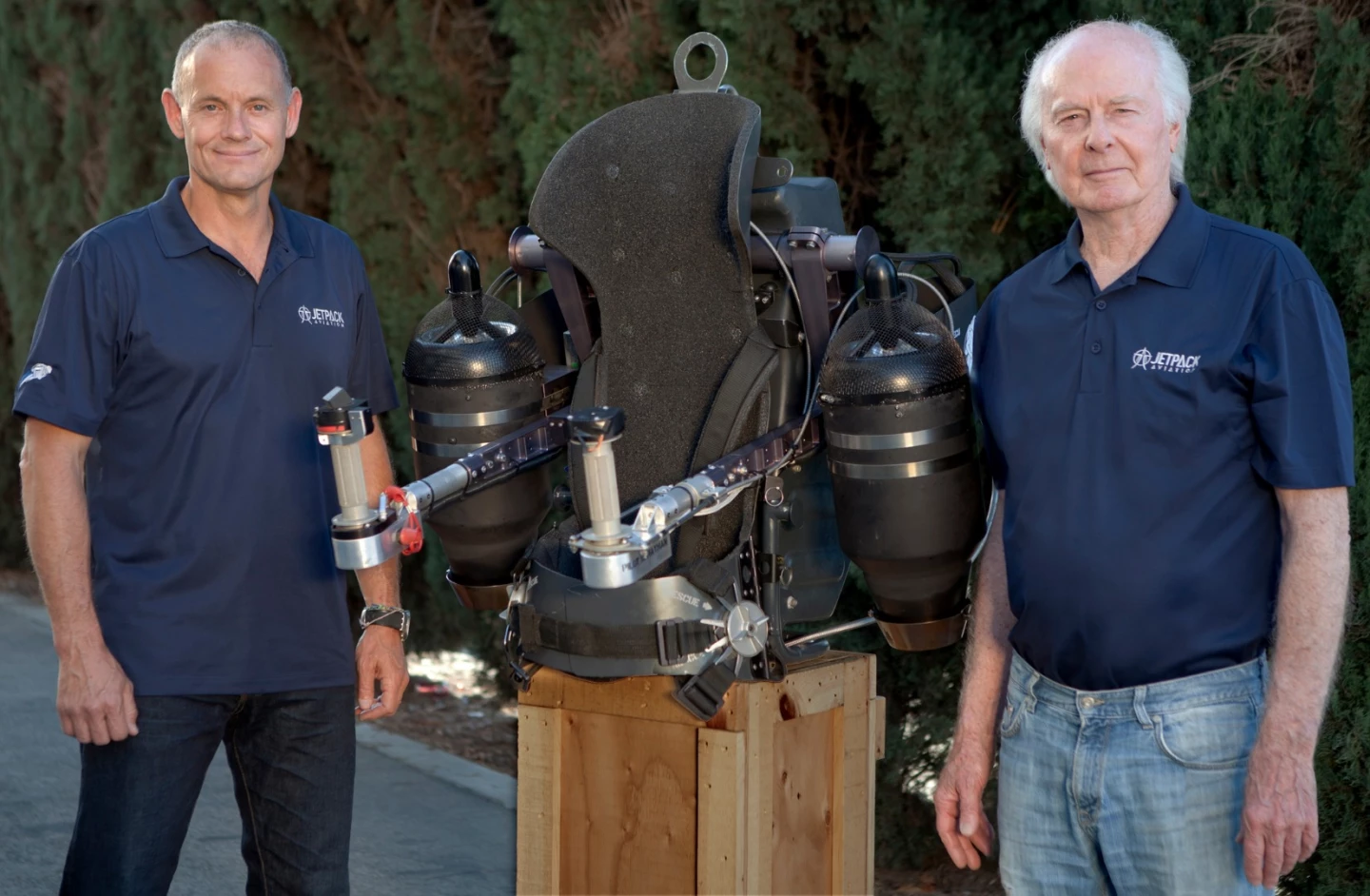
With a six-turbine JB-11 jetpack about to be built, some US Army contracts to fulfil and an all-electric JB-12 in development, the JPA team certainly has its hands full – but not too full to begin pressing ahead on a wild manned multicopter flying car concept that's yet to be named.
Currently at the CAD render stage, the JPA VTOL concept is an early vision of a three-dimensional single-seat commuter. It's a manned multirotor, with 12 props mounted coaxially on six arms. For all intents and purposes, it's a single-seat electric multicopter that'll fit in a single car garage thanks to the center arms folding in.
We caught up with JPA CEO David Mayman on the phone to discuss the development of the VTOL concept, the race to build the first commercially-viable flying car, the future of personal aviation and the challenges the team faces in making these kinds of aircraft safe in the event of failure.
Here's what Mayman had to say, in his own words.
The race is on: who's going to own the upcoming flying car market?
Larry Page has two separate bets on the table, with Zee.Aero and Kitty Hawk. Airbus is having a go with the Vahana. You've got eHang in China and e-Volo in Germany making manned multicopters. Dezso Molnar's doing his thing with the Street Wing and the Gyrocycles – he's an amazing individual, although from my discussions with him, it seems he's not interested in anything that's not roadable.
Our Chief Engineer Stefano went up to Northern California and actually managed to get out on a full tour of the Joby Aviation facility – he said what they're doing out there with the S4 is amazing. He and JoeBen Bevirt, I think they both went to UC Davis together. Stef was pretty open about our intentions in this space, and it was actually all cool.
There's two schools of thought. You've got your winged aircraft with distributed electric propulsion – the Joby, the Airbus, the Zee.Aero – the advantage here is high speed. They can cruise at 2-300 miles an hour (320-480 km/h), so you get speed and range out of that.
We're on the other side. We're taking the manned multirotor approach. More than anything else, because some of the technology's already proven enough. The speeds are lower – you might be talking about 90 miles an hour (145 km/h), but the size factor is so much smaller because you don't have a wing to deal with.
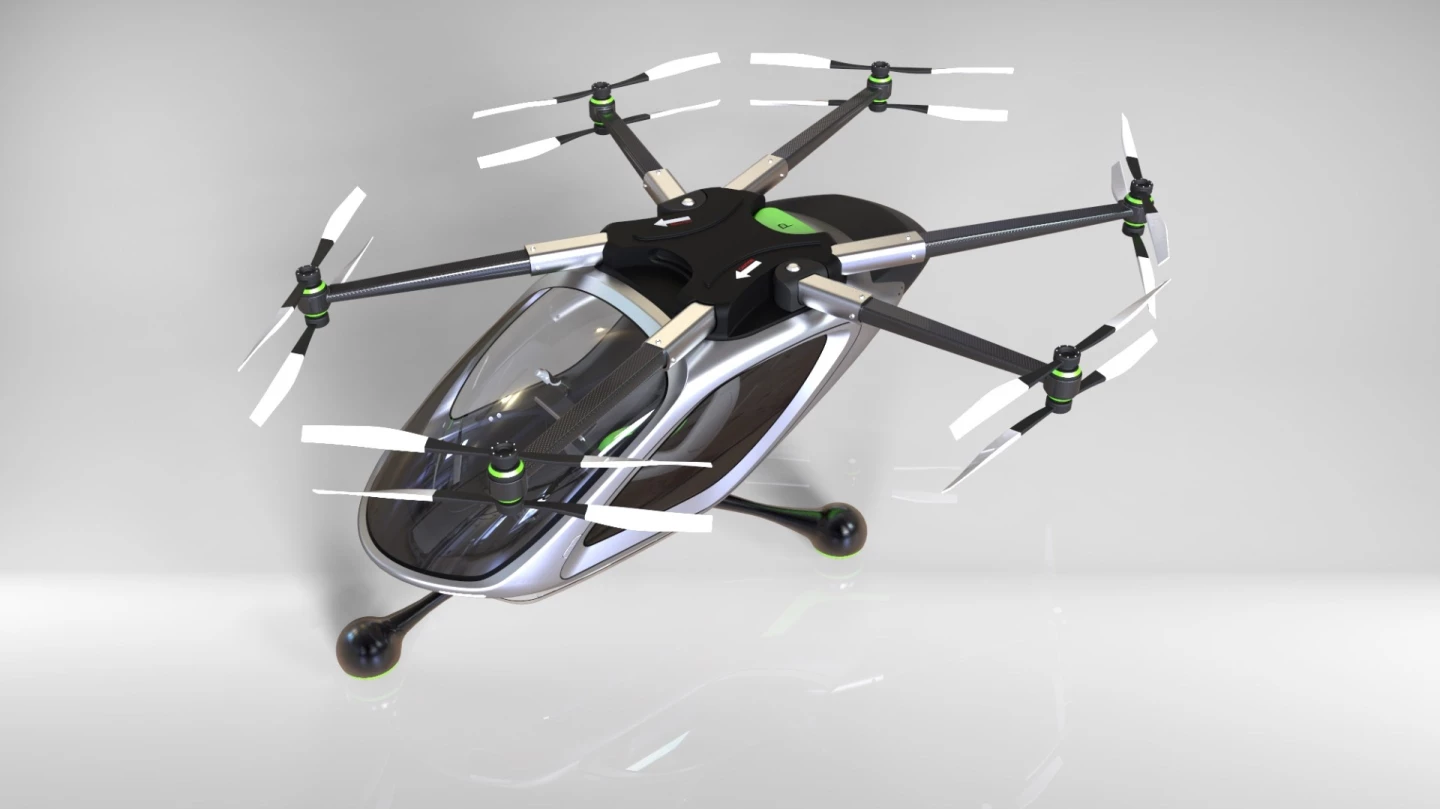
Jetpack Aviation's own VTOL flying car design
The way we're designing ours, there are actually six arms that come out from the top of the chassis – two at the front, two in the middle and two at the rear. The middle one can fold in. The design direction I've given is that it's gotta fit inside a single car garage. It'll be low enough and thin enough to do that, because the side arms and motor pods fold in against the chassis.
There's only one seat in it at the moment, but the beauty of distributed electric propulsion is that it's very, very scalable. The way that electric motors work, it's hey, you wanna make something for two people? OK, you just add power to the electric motors. The ultimate limiting factor comes from battery storage density.
We all – Tesla, everybody working in this space – need it to be higher than the current 200-odd Watt-hours per kilogram we can get at the moment. But they're talking about in four years, maybe it hits 400. That's huge, that's where these electric aircraft will all become very realistic.
We started with landing skids, but we've ended up with little spheres – landing balls.
The Volocopter is a much bigger concept, using the same German Hacker brushless DC motors we're looking at. They're using 18 rotors, I think, which are spread out on six arms that split into 12 arms, and it's quite a large footprint. But they're not mounting the motors coaxially like we're planning to.
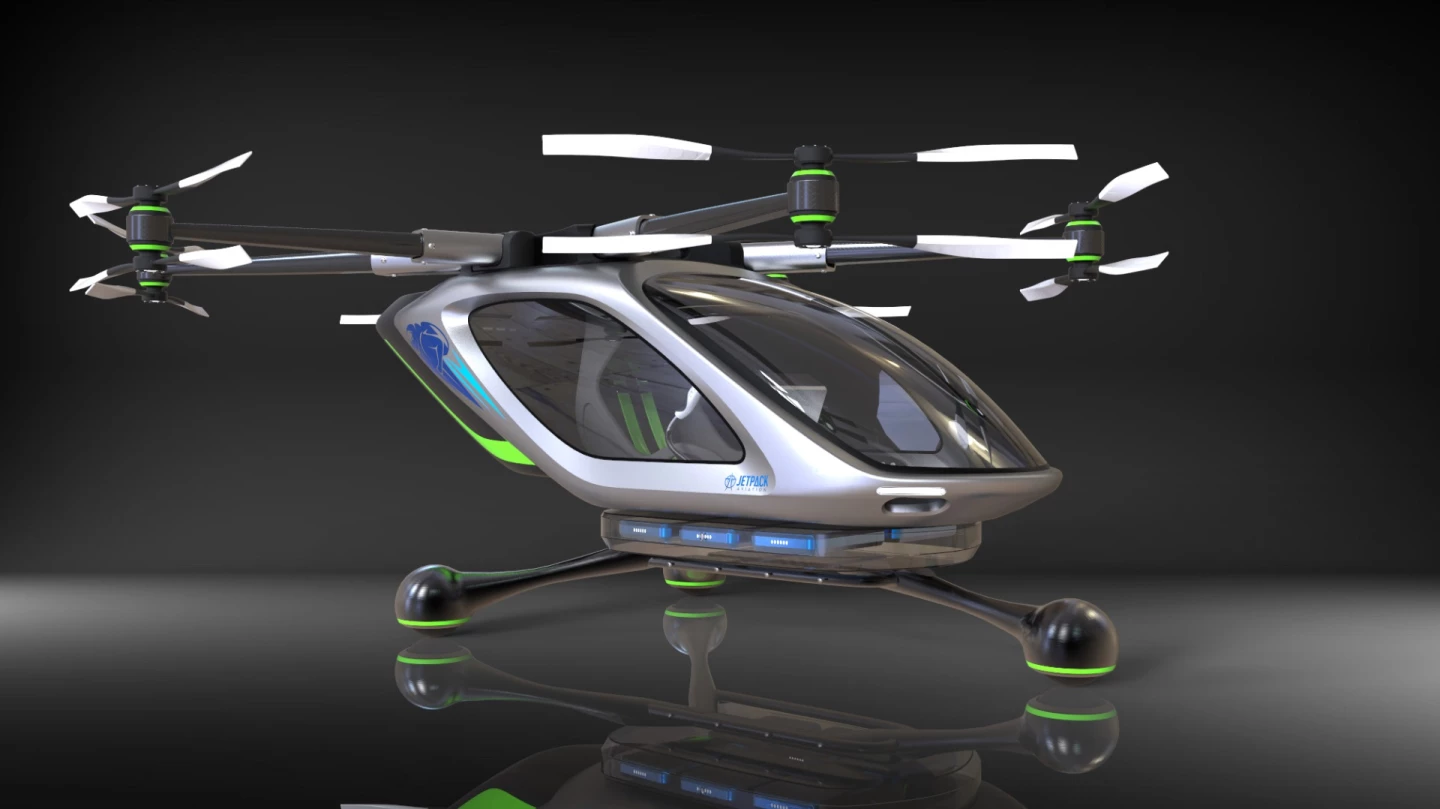
Coaxially mounted double props on each arm
Our concept is that on the end of each of our six arms, you've got a motor on top, and a motor underneath. They spin in opposite directions. It does come with inefficiencies, because the air that's being pushed from the top one down has already been accelerated. So the pitch angle on the lower blades has to be different. But it leads to a much smaller form factor. You can see how instead of having to find real estate for 12 rotors all mounted so the props don't hit each other, this way we can use half the space.
We're still doing the math on the coaxial design in terms of efficiency. We know it works, I mean there's DJI drones out there using it right now. But we just don't know exactly how much efficiency we lose by running it that way.
At this stage we're going for custom wooden props instead of carbon props. You can get them incredibly light, and they're much more resistant to damage. With a carbon prop, if you get any damage, like a little stone, or something, they're pretty much stuffed. A wooden prop is very easy to repair, and there are fantastic little prop makers who can make them any size you want, so they're not very expensive.
These things operate relatively close to the ground, you're talking about 2 meters (6.5 ft) off the ground. There's always the risk of them picking up stuff. I mean, if you look at the eHang 184 out of China, their lower props are literally, they look like 8 inches off the ground. I don't see how that's going to work. If you land on ground that's not perfectly level, or if you come it at a bit of an angle, the prop's the first thing that's gonna hit the ground. I'm not quite sure what the thinking was there. But they have raised a lot of money, I've heard somewhere around US$80 million.
So our props come off the top. Obviously that means some added weight, because you have to have that extra strength through the whole airframe structure to carry the load from the top rather than the bottom.
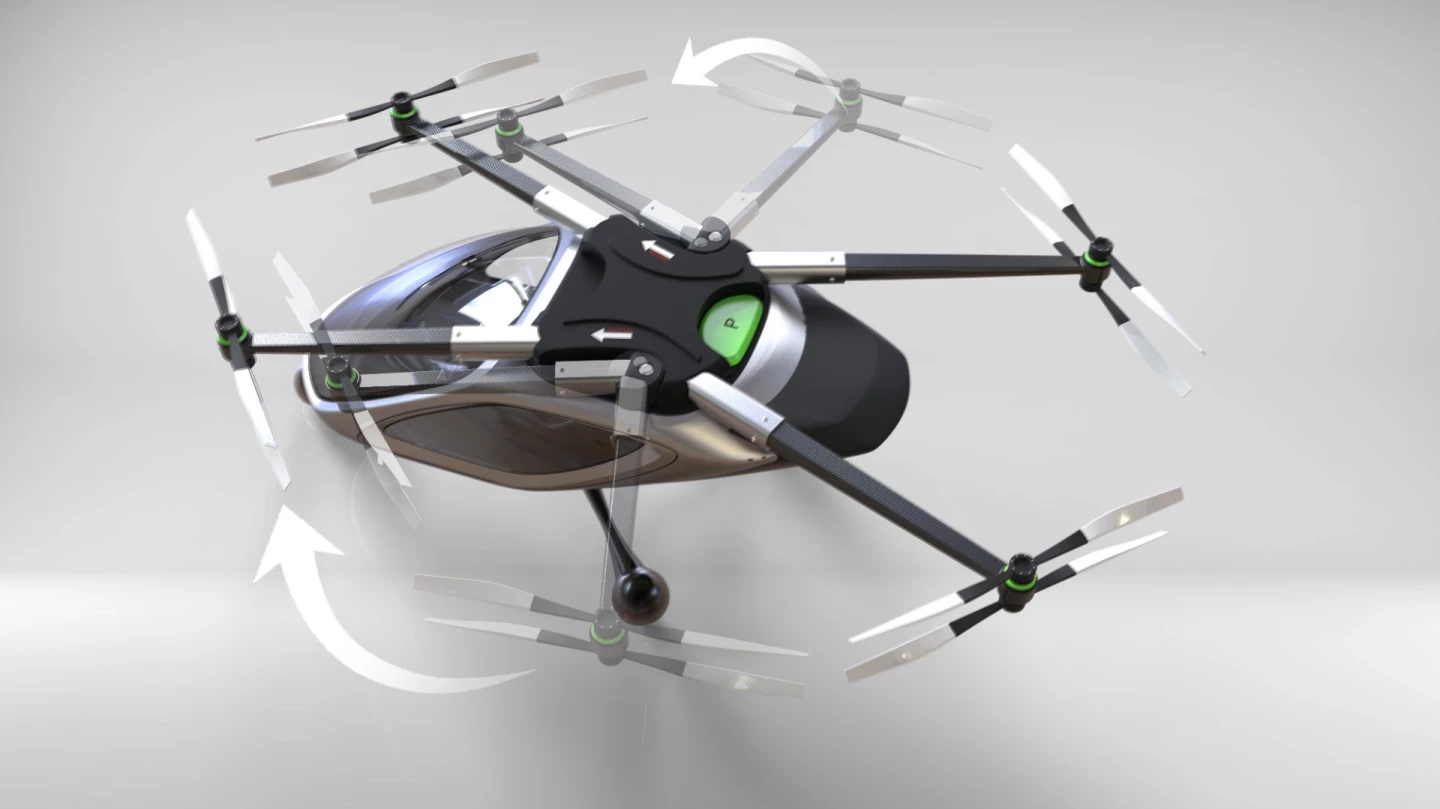
What can you do to extend flight times while battery tech catches up?
We're looking at designing something similar to an extended-range electric car, with a generator on board. In fact, we were looking at perhaps building in a turbine motor, thanks to our experience with turbines on the jetpacks. A very small one, a tiny one, the size of a coke can, can produce a lot of power as a generator.
They do consume fuel faster than, say, a two-stroke motor, but they're so much lighter that you can carry more fuel. Anyway, it's one of the concepts we're looking at. And it could take something from a 20-minute flight time up to an hour with a hybrid range extender.
What's the end game with this design?
I don't want to sound overly optimistic or sci-fi, but these things will be practical. Once the battery density technology advances, these things will be a practical form of transport. We know the infrastructure has to catch up. We know the regulations have to catch up.
But I think that the Uber Elevate whitepaper is right on the money. We all know that this stuff is gonna take time, but at the moment, as we're talking, I'm sitting on the 405 in LA… We're working as if it's a two dimensional world, traveling in serial, car after car after car. All this airspace above us is completely unutilized between 100 and 1,000 feet.
One day, that space will be used. We've got plans on being a part of that. We know it's not gonna be the gas turbine engine that makes sense for that. We know it'll be electric. The technology with battery storage capacity will catch up, and it'll take time. But in the meantime, we work on the other stuff: the airframe. The motor systems. The stabilization.
Drone technology has advanced all of that stuff – the autopilot, the stabilization – to the point where we nearly don't have to do any R&D for that. We can just about start from off-the-shelf products and customize it for our use.
And of course mobile phones – that's generated such a leap in accelerometers and sensors. The power you're carrying around now in terms of inertial measurement and GPS – it used to cost a hundred thousand dollars. Now an iPhone's got three, and they probably cost 20 cents each. And that's driven drone technology.
Then there's the software. Honestly, we could probably build this thing initially using standard hobby-grade DJI software, and it'd work, and it'd probably be pretty much bulletproof, the way they make these things these days. It's just that we want to have redundancy, and we want to be really, really sure that if some circuit board fries, it's got a backup. That's where the engineering effort becomes pretty serious.
But just 15 years ago, it would have been an incredibly daunting undertaking. You would've had to go to Lockheed Martin or Northrop Grumman for every component. Now you could probably build a whole prototype for a million bucks.
Of course, people are doing it a lot cheaper – I've seen some of the videos. For 10 grand you could get something together if you were crazy enough to fly the thing. But if you want to make something that's a little more mil-spec in terms of reliability and redundancy and what have you, and you want to do the carbon fiber work properly, and the engineering studies, it's a more expensive exercise.
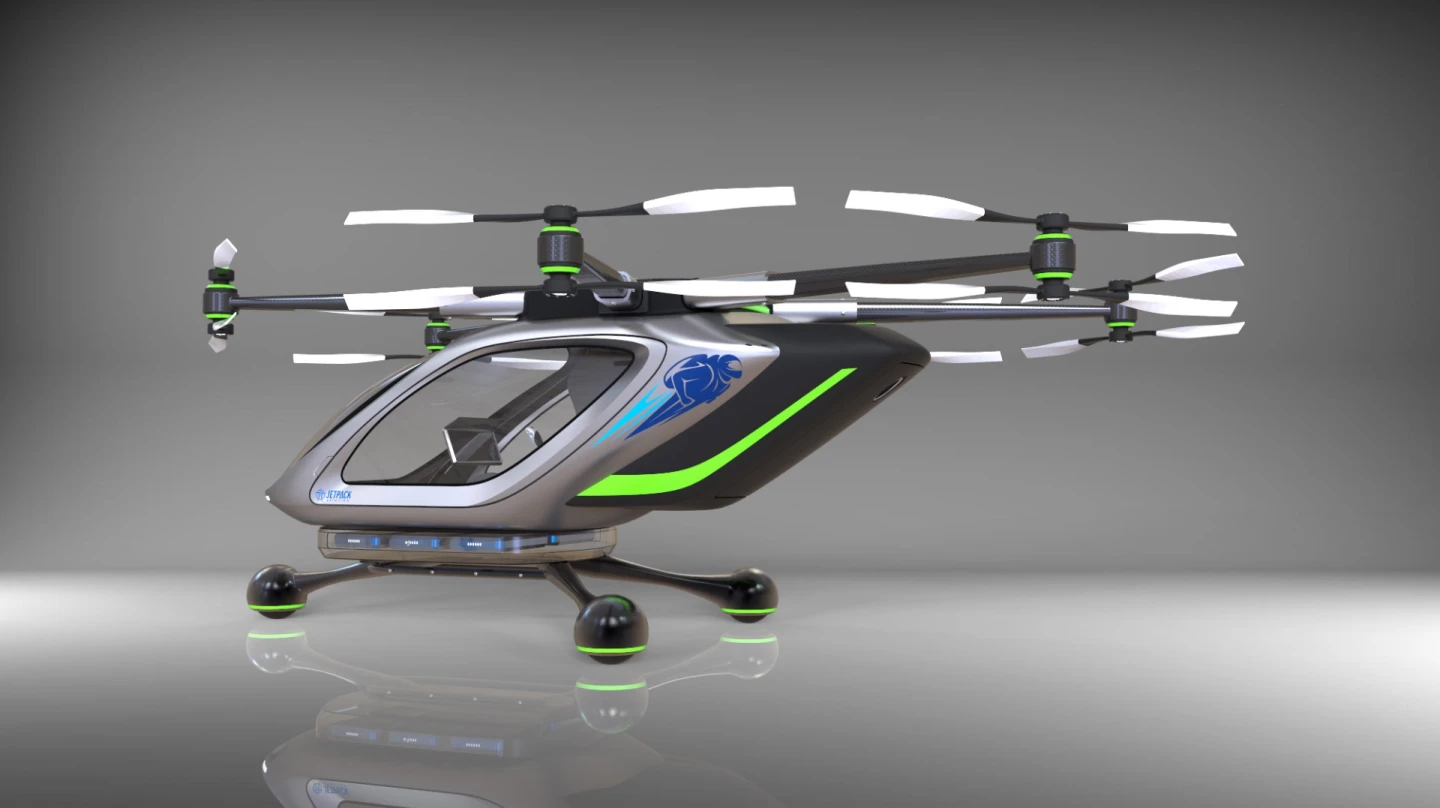
What's the timeframe on getting a prototype built?
Our head engineer Stefano, he gets to work on this as his third priority after the electric six-fan jetpack (the JB12) and the six-turbine jetpack (JB-11). Poor bugger! The JB-11 should be finished by the end of February.
The electric fan jetpack is next. And it won't just be a training rig – it should be able to fly under battery power for about five minutes. It's going to be a pretty awesome machine. You get the redundancy benefit from multiple fans, we get to play with stabilization systems because it's electric and that's really easy, and it's a lot quieter – and frankly it's part of the deal we've got with the US military guys.
In fact, that's how we bumped into Jamie Hyneman, formerly of Mythbusters, who was working on a similar concept for the same guys. Now we're going to work on the same concept together.
The JB-12 won't be much heavier than the JB-10 turbine jetpack – maybe 15 percent – but it will be physically larger, because each of those six fans is 10 inches (25 cm) in diameter. We've got a bunch of them.
For a company of four people, the pace is insane. We're getting an amazing amount done. These VTOL renders are pretty accurate, we believe. We know where we can get the motors, we know where we can get the props, we know where we can get the control systems… We just haven't started building it yet. I think maybe six months is a reasonable estimate on when we'll start. To some extent it's a bit cash flow dependent, but assuming all goes well it'll be in that sort of timeframe.
And it shouldn't actually be a long build. The carbon fiber work is a known entity. The accelerometers and the autopilot, that sort of thing, we know exactly which systems we want to use. The build time on a prototype shouldn't be that long.
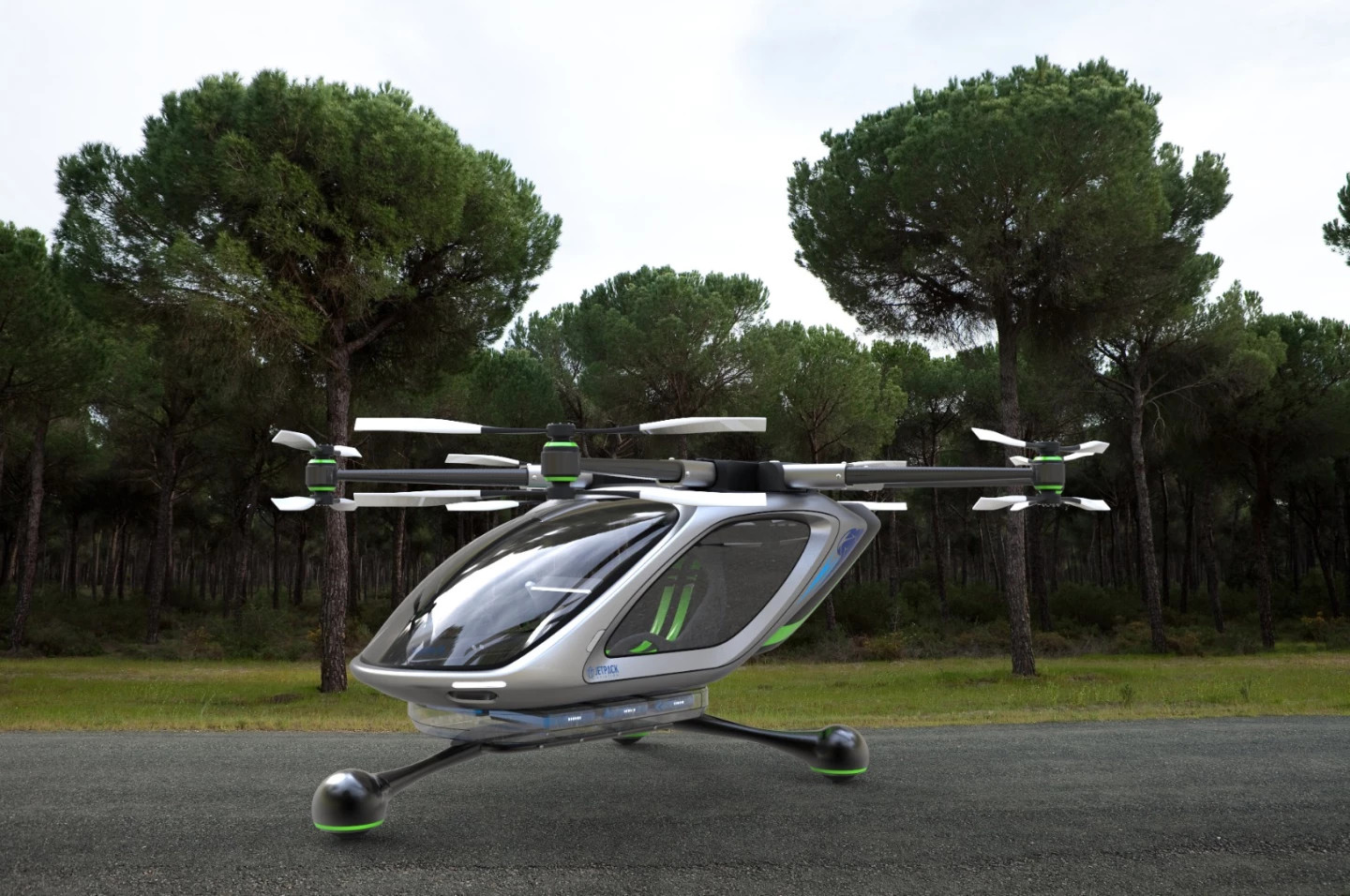
How can you ensure pilot safety?
In terms of redundancy, with the VTOL, we've got 12 props. And while it does depend on which side you get the failures on, we're working on the basis that you could lose half your motors and still come down at an acceptable descent rate. Then it goes to the undercarriage system – something that can collapse in a certain way.
Most of these will probably have a ballistic parachute, but parachutes are only effective above a certain height, which depends on your horizontal velocity and height. If you're in a hover, then with the fastest stuff any of the companies we're talking to can build – Parazero and what have you – it'd only be effective if you're above 50 or 60 feet (15 or 18 m), which is actually really low. They can bring you down safely from that kind of height.
There's a bunch of companies working on a solution to get a canopy out for when you're moving slowly and you get an immediate stable descent. They might punch it out with an airbag, or drag it out with a tractor rocket. They might fire out weights, like lead balls, that open the canopy out immediately.
The problem with all of that stuff is that it works really well when you're in a slow, stable flight or a hover. As in, it works in ideal conditions. But if you're flying along at 80 mph (129 km/h), and you have a massive asymmetric thrust event, and you start toppling, then it doesn't work so well. Then you've got a canopy that's firing while you might be upside down. You might open the chute too fast and it rips it to bits.
There's a lot of people struggling with it – what's the ultimate rescue system for a manned VTOL aircraft, something that works slowly enough to be effective at 200 mph (322 km/h), and yet can fire out quickly enough to be effective in a stable drop from about 50 feet (15 m). It's really interesting stuff.
What about below 50 feet? That's still a deadly fall.
Then you've got the whole concept of airbags. We're actually working with Takata, the big automotive airbag company – they've got an aviation division out in Florida. So it's a question of filling in the safety gap below 50-60 feet - if you drop from, say, 15 feet (4.5 m), how do you immediately get an airbag out to cushion that fall?
With the jetpacks, we're looking at a system that actually jettisons the aircraft from the pilot's corset with explosive bolts, and then protects the pilot with an airbag, something like a giant Zorb ball. You can think of it a bit like the hedgehog thing they had in the Tomorrowland movie. But the challenge is, you have to generate a huge literage of gas in a very short time to be able to fill it.
But with the jetpack jettisoned, you're dealing with about 100 kg (220 lb) instead of, say, 160 (353 lb). Of course, the first thing the FAA says is "well what happens to the jetpack? Does that just fall out of the sky on somebody's head and blow up?" So then you need a little drogue 'chute for that. That's not hard to do, we've got a lanyard that pulls a pin when the pilot separates, and then the drogue 'chute can bring that down at an acceptable descent rate.
But every one of these things, it's weight. Weight is the enemy. We'll have some more power with JB-11, so we'll have more payload capacity. It's all there, it's just time and money.
It must be exciting, pushing forward at the beginning of the personal flight revolution.
It's gonna be a really interesting space over the next 20 years, to track how this VTOL space develops. These things are gonna fly, there's no doubt about that. In 20 years' time, they'll be well and truly out there. We don't know how many, we don't know exactly which designs will prevail, but hopefully it's companies like ours, taking these first tentative steps, that lay the foundations.
We won't be the only ones. We may not be the first ones. But the buzz I get out of it is just being part of the process and working with some of these guys you've been talking to who are so amazing. Everybody has their own view of things.
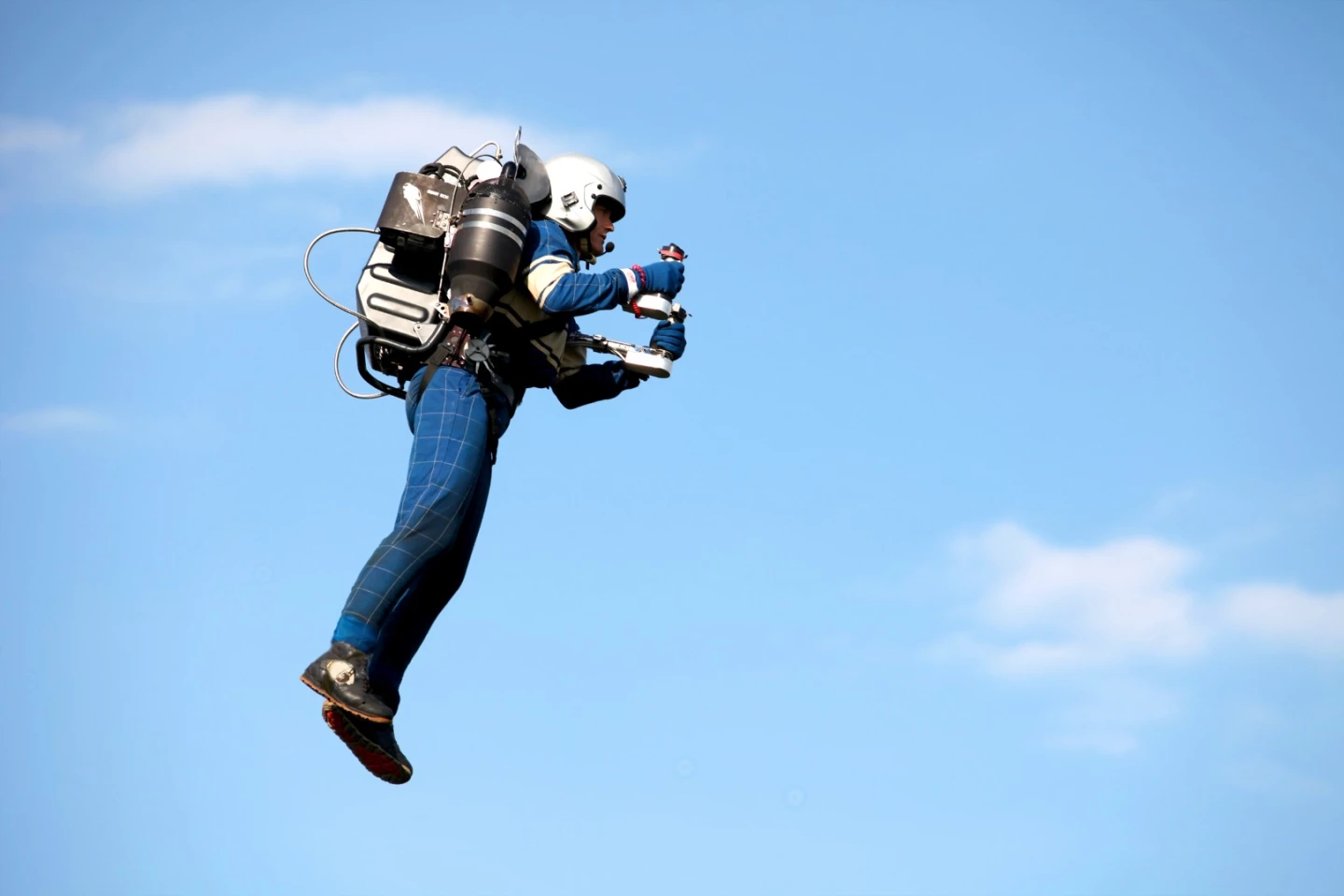
We wish David Mayman, Nelson Tyler and the rest of the Jetpack Aviation team all the best with this project, as well as their other extraordinary ventures.
More information: Jetpack Aviation.