When you burn as much fuel as an airline does, a single-digit fuel efficiency tweak adds up to massive savings. Take the drag-reducing Aeroshark film Swiss Airlines has stuck all over its 12 Boeing 777s – it delivers a 1% efficiency gain, and as a result, over just 12 aircraft, Swiss expects to use 4,800 tonnes less jet fuel every year, saving nearly half a million dollars per year, per plane at today's prices. That'd be closer to half a billion a year for an operator like American Airlines, closing in on 1,000 planes in its fleet, from a 1% efficiency gain.
So you can see how an airliner 30% more efficient than today's best single-aisle machines could be a bit of a big deal. We first ran across Boeing's "truss-braced wing" design concept back in 2010, as a part of the "Subsonic Ultra Green Aircraft Research" (SUGAR) Volt concept it designed as part of a NASA research program.
The idea takes advantage of the higher lift and lower drag you get with longer, slimmer, high aspect ratio wings – the sort you might find on an unpowered glider. A concept Boeing was testing in 2016, for example, had wings some 50% wider than comparable standard aircraft.
Structurally, that kind of thing simply doesn't work without reinforcement. So Boeing's design hangs the wings from the top of the fuselage, and braces them with long trusses coming up from the belly of the plane. These too are carefully shaped airfoils, adding extra lift as well as strength and stability.
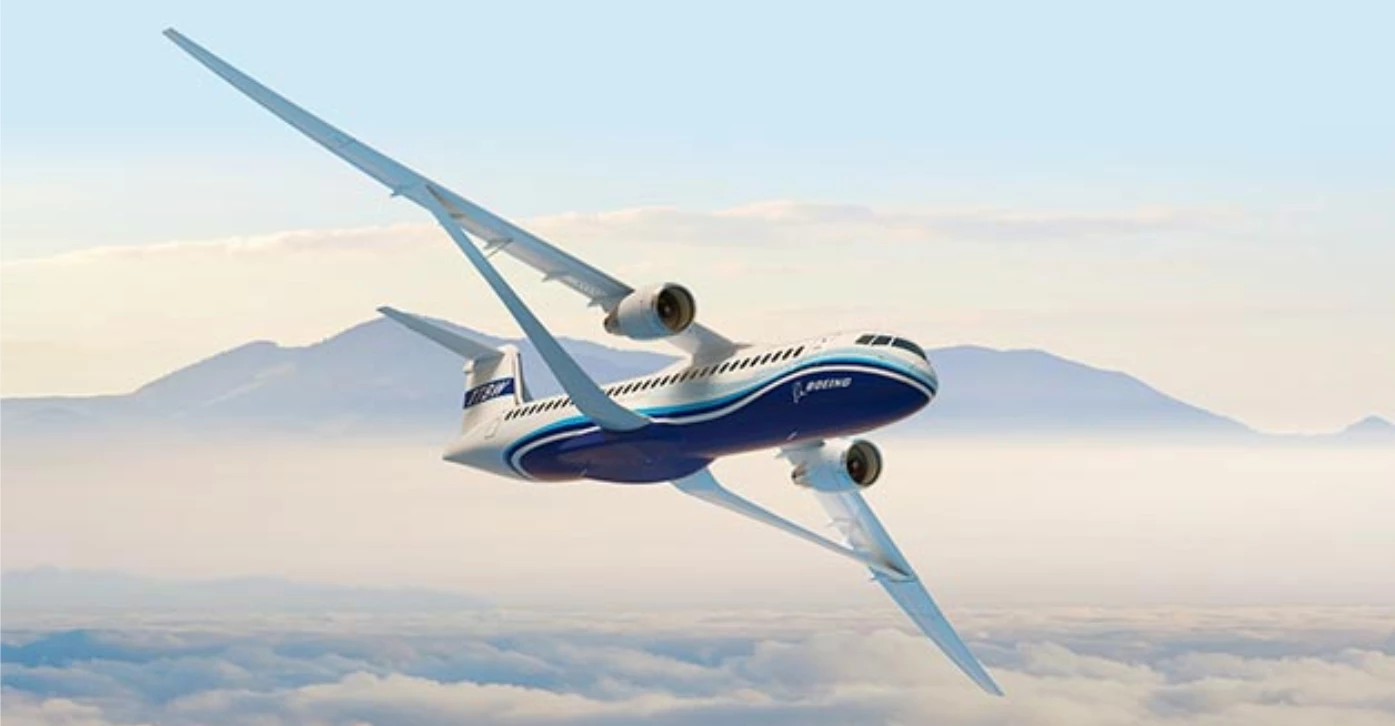
As a subsonic concept cruising at around Mach 0.70 to 0.75 (519 to 556 mph, 835 to 895 km/h), Boeing estimated these braced-wing airliners could burn 50% less fuel than a regular plane. In 2019, the concept was redesigned to cruise at the edge of transonic speed, around Mach 0.8 (593 mph, 955 km/h), and whether because of the added speed or simply from a better understanding of the aerodynamics, Boeing has walked the efficiency claims back.
"When combined with expected advancements in propulsion systems, materials and systems architecture," reads a Boeing press release, "a single-aisle airplane with a TTBW configuration could reduce fuel consumption and emissions up to 30% relative to today's most efficient single-aisle airplanes, depending on the mission."
It's been a long time in digital modeling and subscale wind tunnel testing, but NASA has now awarded Boeing funding through the SFD Space Act agreement to the tune of $425 million, to be thrown in with some $725 million from Boeing and various other business partners, to actually go and build the thing at full scale and get it properly flight tested.
NASA says it plans to complete testing on the Transonic Truss-Braced Wing demonstrator aircraft "by the late 2020s, so that technologies and designs demonstrated by the project can inform industry decisions about the next generation of single-aisle aircraft that could enter into service in the 2030s."
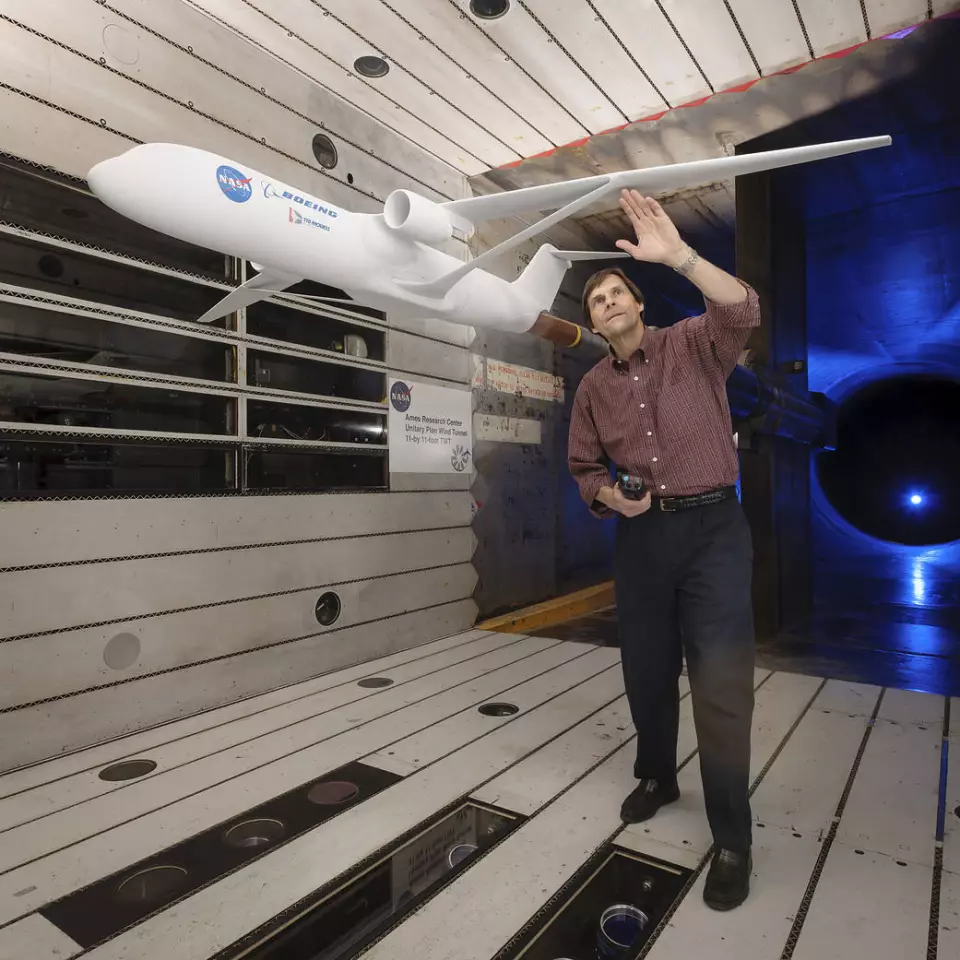
There will certainly be challenges. For starters, these super-long wings might simply not fit with existing airport terminals or hangars. Boeing hasn't said anything about the demonstrator aircraft, but on the 2019 concept it spoke of using foldable wings to get around this issue on the ground.
And then there's the fact that the huge, thick, lower aspect ratio wings on standard airliners create a perfect hollow space for their fuel tanks. Keeping the fuel out in the wings places a lot of weight out wide, closer to the center of lift, reducing engineering stresses where the wings meet the body. It contributes to safety somewhat in a crash, keeping burning fuel further from the passengers. And from a pure brass-tacks perspective, it frees up room in the cabin for extra money-making seats. The truss-braced design uses such slim wings that fuel tanks will likely have to go back into the fuselage.
On the other hand, Boeing says that the high-mounted, braced wings "could eventually accommodate advanced propulsion systems that are limited by a lack of underwing space in today's low-wing airplane configurations" – although this demonstrator won't be testing any fancy new motors straight away.
And it goes without saying, anything that can take planes further on a given amount of energy has exceptional relevance to decarbonization efforts. Battery-electric, hydrogen-electric, hydrogen-combustion, ammonia and other clean powertrain technologies are all constrained by lower range figures than traditional jet fuel power, and designs like these could definitely make a big contribution.
You can see some of the CFD (Computational Fluid Dynamics) and wind tunnel work that's gone into this design in the video below, including a rather gnarly looking flutter simulation that makes us feel like trains might be a pretty good option.